Pottery slip is a versatile and essential liquid clay mixture used extensively in ceramics. It serves various purposes, from decorating and joining pieces to casting intricate forms and creating unique textures. Pottery slip can be applied to both greenware and bisque ware, enhancing the aesthetic qualities and functional aspects of ceramic pieces. Understanding “how to make slip for pottery” is fundamental for anyone looking to explore the world of ceramics, whether for creative expression or functional crafting.
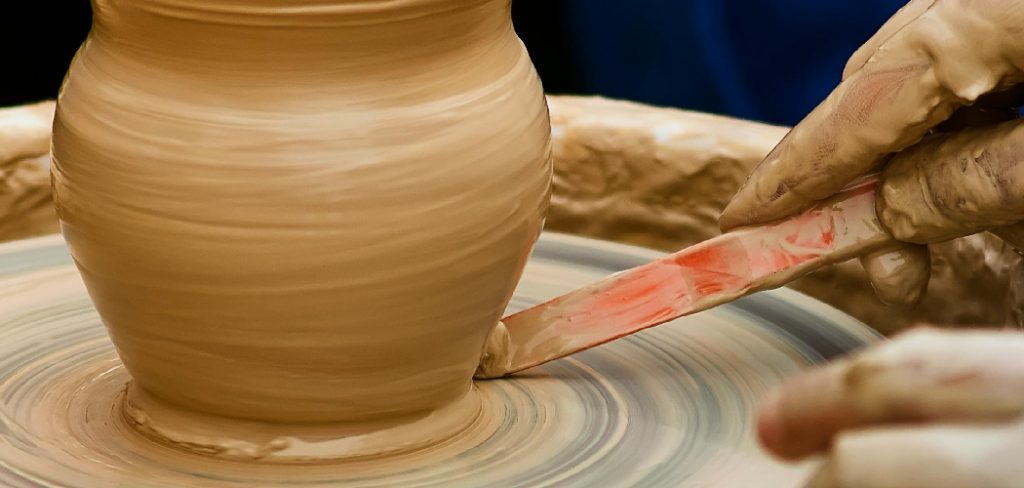
This guide is designed with beginners in mind, offering step-by-step instructions to make slips at home using basic materials. With a focus on practical techniques and accessible advice, readers will learn to create slips suitable for slip casting and creative decoration, thereby unlocking a range of possibilities in their pottery projects. Mastering slip-making becomes a valuable skill in any potter’s repertoire through experimentation and practice.
Understanding Pottery Slip
What is Slip?
Slip is essentially a suspension of clay particles in water, which makes it fluid and easy to manipulate. This medium is crucial in various pottery processes, providing the flexibility needed for joining pieces, decorating surfaces, and creating smooth finishes. The fluidity of slip enables potters to seamlessly blend elements together or enhance the aesthetics of their work through decorative applications.
Types of Slip
- Casting Slip: Utilized in creating ceramics through molds, casting slip is perfect for crafting both hollow and solid forms. It is specifically formulated to maintain a fluid consistency while offering structural integrity to the molded piece.
- Decorative Slip: Applied to the surface of pottery, decorative slip adds texture or color. Techniques like slip trailing, where slip is applied in intricate patterns, allow for unique artistic expressions.
- Joining Slip: This type of slip is essential for attaching separate pieces of clay, such as handles or additional components, ensuring robust and secure bonds.
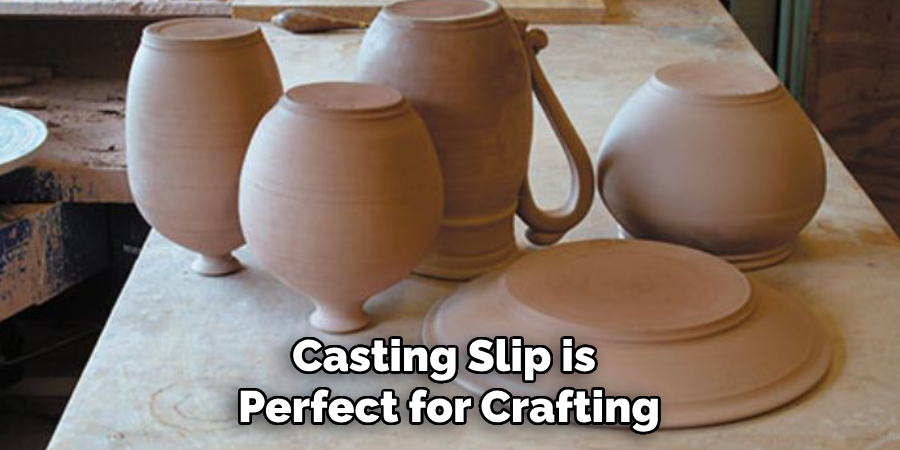
Why Make Your Own Slip?
Making a slip at home gives you control over its consistency and composition. You can customize slips for different uses, from casting to decoration, allowing for a tailored approach to each project and enhancing your creative possibilities in pottery making.
Materials Needed
Having the right materials on hand is crucial when preparing slips for your pottery projects. This will ensure the desired consistency and functionality.
- Clay Body: To ensure compatibility, it’s important to use the same type of clay as your ceramic piece. Depending on your project needs, this can be stoneware, earthenware, or porcelain clay.
- Water: Distilled water is recommended as it is free from minerals and impurities that might affect the clay. Using tap water can introduce unwanted elements that may alter your slip’s performance and quality.
- Sodium Silicate or Deflocculant (Optional): These additives can be particularly helpful for casting slip, as they maintain fluidity and reduce the water required, allowing for smoother pouring and stronger finished pieces.
- Blender or Mixer: A blender or mixer helps integrate clay and water seamlessly, ensuring an even, lump-free slip mixture.
- Sieve: Straining the mixture through a sieve ensures a smooth consistency by removing any remaining clumps or particles.
- Bucket or Container: Essential for mixing and storing the slip, a durable bucket or container provides the space and stability needed to create and keep your slip ready for use.
How to Make Slip for Pottery: Preparing the Clay for Slip
Step 1: Collect Clay Scraps or Powder
Begin by gathering leftover clay scraps from your pottery studio or cutting fresh clay from a block. It’s beneficial to use smaller clay pieces or dried clay scraps that are more convenient to dissolve in water, which will streamline the slip-making process.
Step 2: Dry the Clay (Optional)
For those using wet clay, consider allowing it to dry completely before creating slip. Dry clay absorbs water more readily, leading to a smoother and more consistent slip mixture. This step is optional but can be advantageous when seeking a refined finish in your pottery projects.
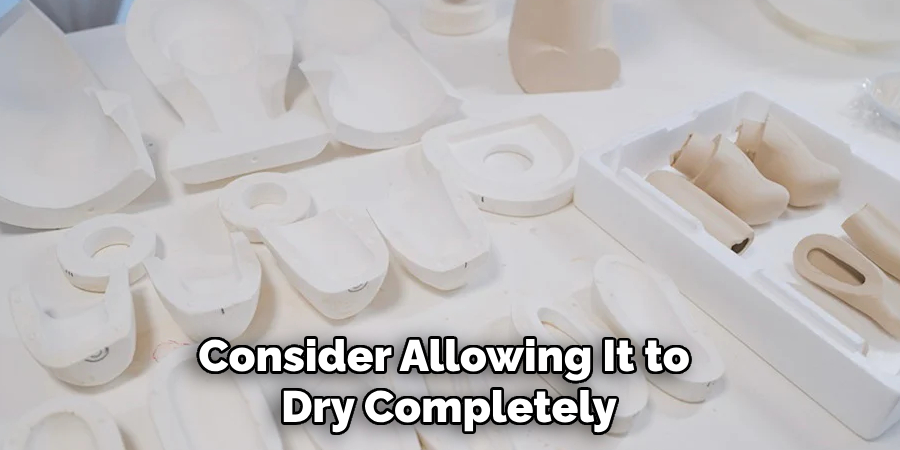
Step 3: Crush the Clay
Once your clay is dry, break it into smaller fragments to expedite the slip-making process. Employing a hammer or rolling pin can be effective for crushing larger pieces of clay, thus enhancing the ease of dissolution and ensuring a lump-free mixture.
Step 4: Weigh the Clay
Accurately weigh the dry clay pieces to achieve the correct water-to-clay ratio, which is vital for the consistency of your slip. A commonly recommended ratio is 1 part clay to 1.5 parts water by weight. This ratio can be adjusted based on your specific needs, depending on whether you desire a thicker or more fluid slip for your pottery endeavors.
How to Make Slip for Pottery: Mixing the Slip
Step 1: Add Water
Place the dry clay pieces into a bucket or container. Add distilled water to the clay using the recommended ratio of 1.5 parts water to 1 part clay. For instance, if you have 1 kilogram of dry clay, incorporate 1.5 liters of water into the mix. Allow the mixture to sit for several hours, or even overnight, to enable the water to penetrate and soften the clay thoroughly.
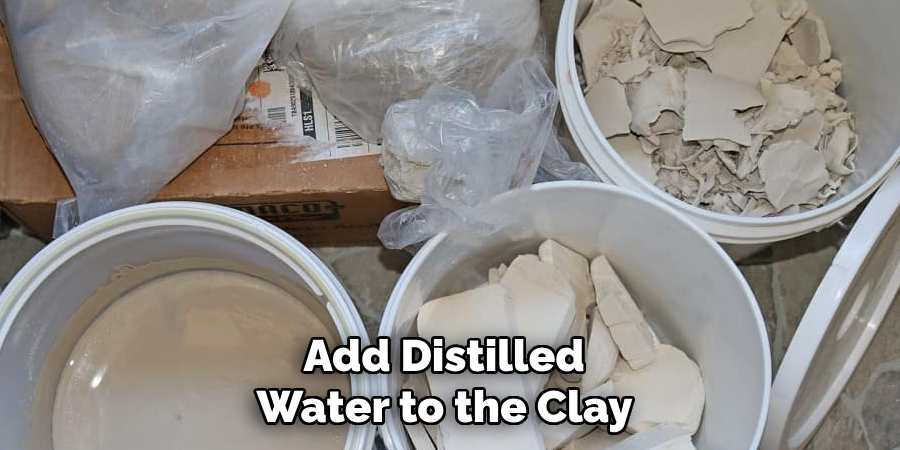
Step 2: Blend the Mixture
Once the clay has softened, employ a blender or hand mixer to convert the softened clay and water into a uniform, thick liquid. A hand blender will suffice for small batches. For larger quantities, consider using an electric drill attached to a mixing bit to enhance the blending process.
Step 3: Strain the Slip
After blending, pass the mixture through a fine mesh sieve to eliminate any lumps or irregularities. This step is crucial for achieving smooth and even consistency in your slip. A spatula gently pushes the mixture through the sieve, ensuring all particles are adequately filtered.
Step 4: Adjust the Consistency
Evaluate the slip’s consistency and make any necessary adjustments. If the mixture is too thick, introduce a small amount of water and re-blend until it reaches the optimal consistency. Conversely, if the slip is too thin, either allow some of the water to evaporate naturally or incorporate more dry clay, blending thoroughly to rectify the thickness.
Step 5: Add a Deflocculant (For Casting Slip)
If your goal is to create a slip specifically for slip casting, introduce a minuscule quantity of sodium silicate or a similar deflocculant into the mixture. This component aids in maintaining the fluidity of the slip without necessitating excess water, thus preserving the structural integrity of the eventual ceramic piece. Exercise caution to avoid using too much deflocculant, as an excess can render the slip overly runny.
Step 6: Let the Slip Rest
Finally, allow the slip to rest for a few hours. This interlude helps to eradicate air bubbles and permits the clay particles to settle uniformly throughout the mixture, ensuring an even distribution of texture and smoothness. This resting period is pivotal for attaining the ideal state of readiness for your pottery endeavors.
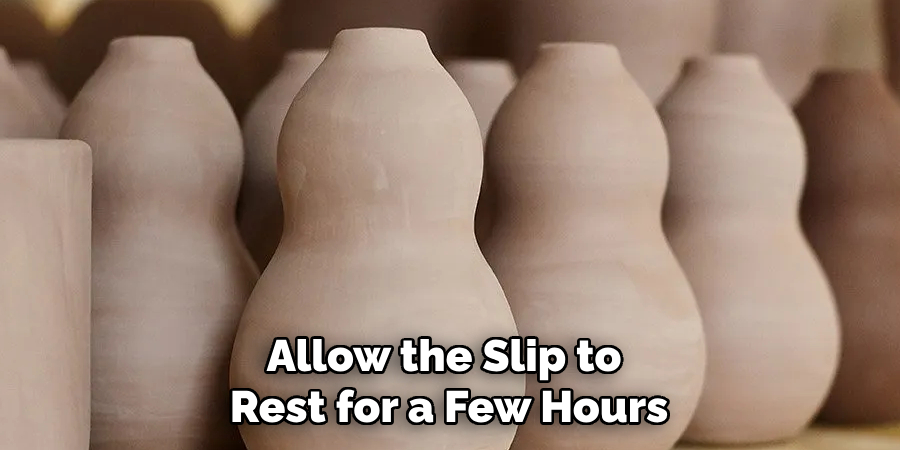
Using Pottery Slip
The versatility of pottery slip extends beyond mere functionality, serving as a critical tool in both crafting and artistic expression. There are myriad slip applications in the pottery process, from casting to decoration, each allowing for unique outcomes in ceramic work. Below are some of the primary uses of pottery slip:
1. Slip Casting
Step 1: Pour the slip into a plaster mold, which will naturally absorb moisture from the slip and create a thin, solid layer on the mold’s interior walls.
Step 2: Let the slip rest in the mold for 10-15 minutes or more, depending on how thick you want the walls of your ceramic piece to be.
Step 3: Carefully pour out the excess slip, leaving a coat adhered to the mold. Allow this adhered layer to dry within the mold.
Step 4: Remove it from the mold once the formed clay has dried sufficiently and is firm enough to handle. It is now ready for further trimming, refining, or applying glaze.
2. Decorative Slip
Slip Trailing: Use a slip trailer, squeeze bottle, or even an applicator to apply slip-in decorative patterns on greenware. This can include intricate designs, themes, or abstract concepts.
Slip Brushing: Employ a soft brush to paint slip onto the surface of your pottery, either as a smooth, even layer or with expressive, textured brushstrokes for added visual interest.
Sgraffito: Apply a uniform layer of colored slip onto your pottery piece and carve into this layer to create designs. The technique exposes the clay body underneath, allowing for contrast and intricate detailing.
3. Joining Pieces with Slip
Step 1: Score the surfaces of the two clay pieces you wish to join, such as fixing a handle onto a mug. This ensures a better adhesion surface.
Step 2: Apply a generous amount of slip to the scored areas. The slip acts as a bonding agent between the two surfaces.
Step 3: Press the pieces together firmly, smoothing out the seam with a tool or finger. This step is crucial to create a seamless and robust connection, ensuring the joined structure can withstand further handling and firing processes.
Utilizing these techniques with pottery slip enhances both the practical and aesthetic attributes of ceramic creations, making slip an indispensable component in the potter’s toolkit.
Storing Slip
Proper storage of pottery slip ensures it remains usable and maintains its desirable consistency. For short-term storage, it is crucial to keep the slip in an airtight container to prevent it from drying out. Before each use, give the slip a thorough stir, as the clay particles tend to settle at the bottom over time, which may affect its texture and application. For long-term storage, periodically check the slip’s moisture level to maintain consistency.
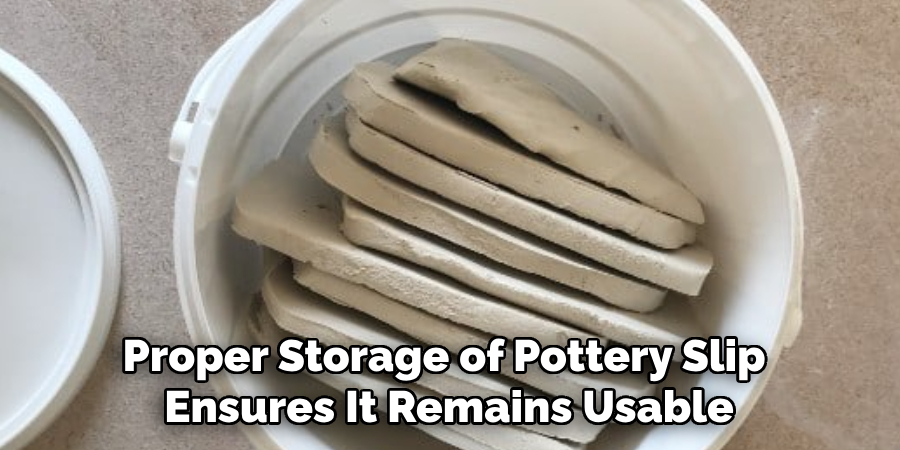
If it appears to be thickening, slowly incorporate water, stirring until the slip returns to its optimal state. Additionally, a small amount of deflocculant can be added if necessary to keep the slip fluid. With careful management, slip can remain viable indefinitely. However, regular maintenance is key to ensuring it does not lose its quality or become overly thick, thus saving time and resources in future pottery projects.
Conclusion
In conclusion, understanding “how to make slip for pottery” is fundamental for both novice and experienced potters. The process begins by preparing a balanced clay and water mixture, followed by careful blending and straining to remove impurities, ensuring a smooth, uniform consistency. Each step, from slip casting to creative decorative techniques like slip trailing and sgraffito, demands precise consistency to achieve desired results.
Whether you are joining pieces or exploring decorative styles, the integrity of your pottery relies on the slip’s quality. Achieving the perfect slip consistency is crucial, as it must align with each specific application to ensure success. Moreover, don’t shy away from experimenting with various clay types and slip techniques to discover unique artistic effects. With dedicated practice and attention to detail, mastering the art of slip-making can significantly enhance your pottery endeavors, resulting in exquisite and personalized ceramic creations.
Specialization:
- Master of wheel-throwing, hand-building, and advanced glazing techniques
- Focus on creating both functional pottery and decorative art pieces
Recognition:
- Celebrated by collectors and art enthusiasts for creating one-of-a-kind pieces that blend artistry with functionality
- Participates in local and national exhibitions, earning accolades for his innovative designs and craftsmanship
Passion:
- Deeply committed to exploring and pushing the boundaries of ceramic artistry
- Continuously experiments with new materials, firing techniques, and artistic concepts to evolve his craft
Personal Philosophy:
- Believes in the transformative power of art, aiming to evoke emotions and connections through his ceramic creations
- Advocates for sustainability in ceramics, using eco-friendly materials and practices whenever possible