Ceramic pipes have been used throughout history for a variety of applications, from plumbing to artistic expressions. Crafting these pipes involves a blend of traditional techniques and modern innovations, offering a rewarding experience for both beginners and seasoned artisans. In this guide, we will explore how to make ceramic pipes. Whether you are pursuing this craft as a hobby or with a functional purpose in mind, understanding the foundational processes will set you on a path to success.
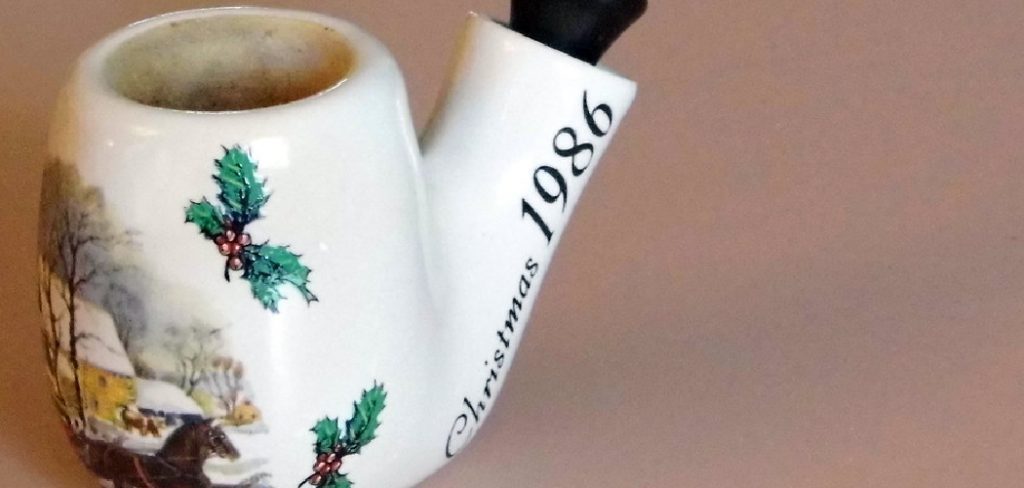
Ceramic Pipes and Their Popularity in Crafts
Ceramic pipes have garnered widespread popularity in the craft world due to their versatility and aesthetic appeal. Artisans appreciate the ability to shape them into intricate designs, allowing for a high degree of artistic expression. Whether used as decorative items or functional pieces, ceramic pipes continue to captivate hobbyists and professionals alike. The popularity of ceramic pipes also stems from the variety of finishes and glazes available, which offer an extensive palette of colors and textures to experiment with. This adaptability has led to their prominent presence in crafting communities, where they are celebrated for both their historical significance and contemporary flair.
Materials and Tools Needed
Before embarking on the journey of making ceramic pipes, it’s essential to gather the right materials and tools. The primary material is clay, which can be sourced in various forms such as earthenware, stoneware, or porcelain, each offering unique properties and finishes. Alongside clay, you will need a kiln for firing the pipes, which solidifies the clay and can enhance its durability and aesthetic quality.
It’s also essential to have a potter’s wheel if you plan on creating symmetrical and rounded designs. Basic tools include a rolling pin for flattening the clay, needle tools for carving and detailing, and sponges for smoothing and finishing surfaces. To add intricate designs, consider acquiring modeling tools of various shapes.
Preparing to Make Ceramic Pipes
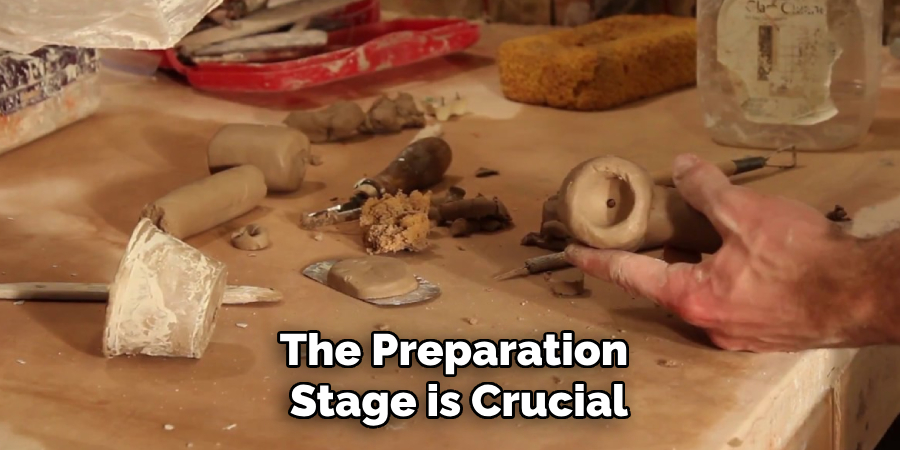
The preparation stage is crucial to ensure success in making ceramic pipes. Start by setting up a clean, organized workspace that allows for easy access to your materials and tools. Ensure the area has a sturdy table and adequate lighting. Begin by kneading the clay to remove any air bubbles, a process known as wedging, which promotes an even texture and prevents cracks during firing.
Once the clay is pliable, measure out the amount needed for your project, considering the size and thickness of the pipe you wish to create. Familiarize yourself with your tools, practicing with them on scraps of clay to build your confidence. Additionally, establish a clear plan or design for your pipe. Sketching out your intended design helps visualize the final product and guides you through each step of the crafting process.
10 Methods How to Make Ceramic Pipes
1. Gather All Necessary Materials and Tools
The first step in making ceramic pipes is gathering the essential materials and tools. You’ll need high-quality clay, a pottery wheel (if desired for symmetrical pipes), hand tools like rib tools and wooden paddles, as well as a kiln for firing. Basic shaping tools, such as a sponge, wire cutter, and shaping sticks, are also helpful. For finishing touches, consider getting some glazes, brushes, and sandpaper to achieve the desired surface and color. Having these items on hand will streamline the entire process and keep you focused on crafting.
2. Choose the Right Type of Clay
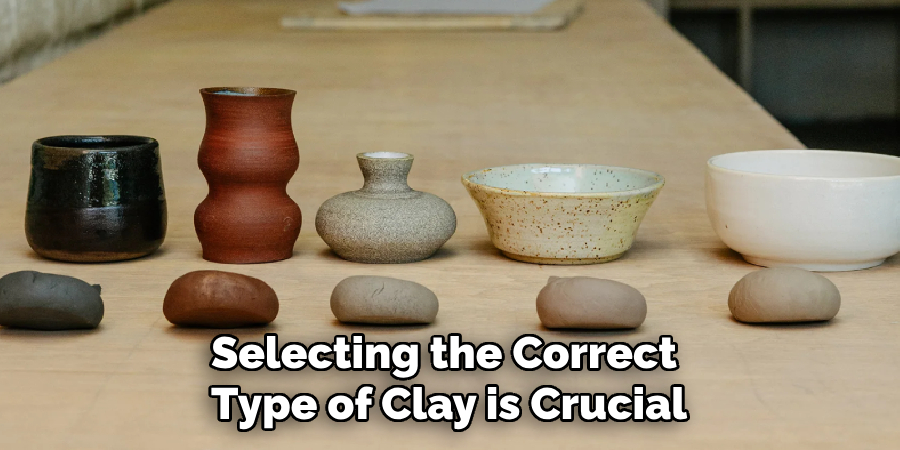
Selecting the correct type of clay is crucial to ensure that the pipe is durable and functions as intended. Stoneware clay or porcelain is generally recommended because these types are non-porous and can withstand high temperatures. Stoneware, in particular, is highly durable, making it ideal for creating long-lasting pipes. Porcelain clay, while more delicate to work with, can yield a smoother, more refined finish. Whichever clay you choose, make sure it’s appropriate for functional ceramics that will be fired to high temperatures.
3. Prepare the Clay by Wedging
Properly preparing the clay through a process called “wedging” helps remove air bubbles and improves its consistency. To wedge, press and knead the clay on a flat surface, rotating it with each press. This process aligns the clay particles and reduces the likelihood of cracks or imperfections during firing. Spending time on this step is essential, as trapped air bubbles can cause the pipe to break or explode in the kiln. Aim for a smooth, even texture to ensure easy shaping and durability.
4. Shape the Pipe’s Main Body Using Hand Techniques or a Pottery Wheel
Depending on your comfort level and style, you can shape the pipe by hand or with a pottery wheel. For hand-building, use techniques like coiling, slab building, or pinch potting to form the pipe’s main body. Roll coils and stack them to create the walls, or roll out flat slabs and wrap them around a cylindrical mold. If using a wheel, center the clay and create a cylinder, thinning the walls until you achieve the desired size and shape. Take your time to maintain even walls, as this is crucial for a sturdy pipe.
5. Create the Pipe’s Chamber and Airway
The chamber and airway are integral to a functional ceramic pipe, as they allow for airflow. Use a shaping stick or hollow tube to carve out a bowl at the top of the pipe body. Next, carefully insert a thin wooden dowel or metal rod horizontally through the clay to create an airway from the bowl to the mouthpiece area. Take care not to create any blockages, and ensure the airway is clear. Remove any clay clinging to the tool after making the airway to keep the channel smooth and open.
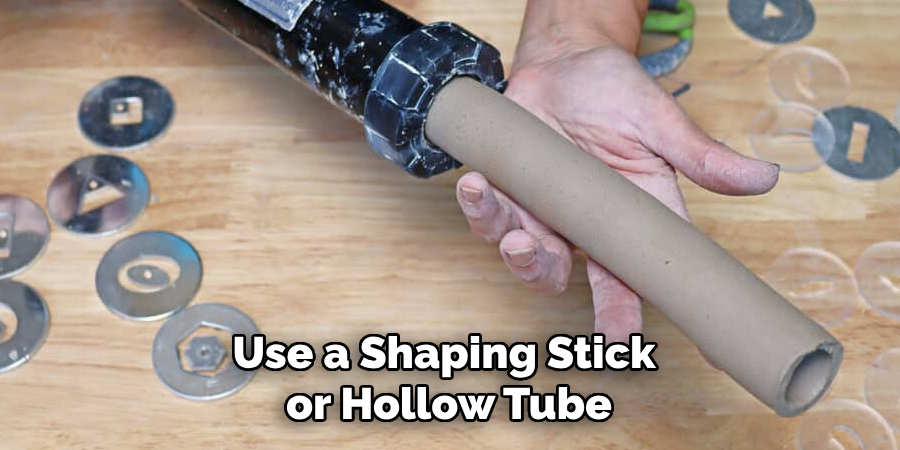
6. Refine the Shape and Smooth the Surface
After forming the basic shape, refine the pipe by smoothing out rough areas and perfecting its symmetry. Use a damp sponge to gently smooth the surface, addressing any visible marks or inconsistencies. A rib tool can also help refine curves and edges, especially around the bowl and mouthpiece. This step adds to both the appearance and the functionality of the pipe, as a smooth surface is not only more attractive but also more comfortable to hold and use.
7. Allow the Pipe to Dry Slowly to Leather-Hard Stage
Drying is a crucial stage in ceramics, and it should be done gradually to avoid cracks or warping. Place the pipe in a cool, dry place away from direct sunlight and cover it lightly with plastic to slow the drying process. Allow the pipe to reach a leather-hard stage, where it’s firm enough to hold its shape but still contains some moisture. At this stage, the clay is easier to work with for further detailing or attaching additional elements, and it reduces the chances of breakage in the kiln.
8. Apply Finishing Touches and Optional Decorations
Once the pipe is leather-hard, you can add any final decorative touches. Carving designs, adding slip (liquid clay), or using underglaze for detailed patterns are popular methods for personalization. Be mindful of the pipe’s function when adding decorations, avoiding any protrusions or elements that might make it uncomfortable to hold or use. These finishing touches not only enhance the pipe’s visual appeal but also allow you to express your personal style, making each piece unique.
9. Bisque Fire the Pipe to Prepare it for Glazing
The next step involves bisque firing, a preliminary firing that hardens the clay and prepares it for glazing. Place the dried pipe in a kiln and fire it to the recommended bisque temperature, typically between 1730°F and 1940°F (945°C and 1060°C), depending on the clay type. Bisque firing removes moisture and makes the clay sturdy enough to handle glazes. Allow the kiln to cool fully before removing the pipe, as sudden temperature changes can cause cracking or breakage.
10. Glaze and Final Fire the Pipe
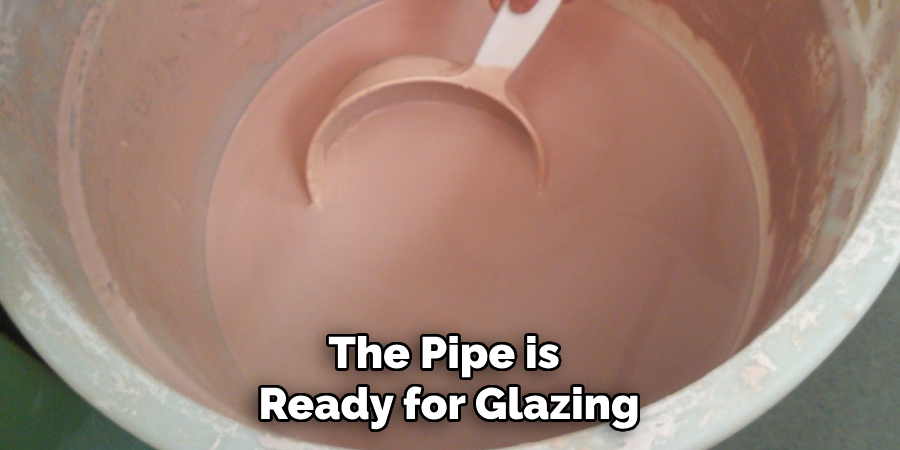
After bisque firing, the pipe is ready for glazing and a final firing. Choose a glaze that is food-safe and can withstand high temperatures, as pipes need to be functional and non-toxic. Apply the glaze with a brush, sponge, or by dipping the pipe into the glaze. Be sure to leave the bowl area unglazed if you plan to use the pipe, as direct heat may affect the glaze’s durability. Once the glaze is applied, place the pipe back in the kiln for a high-temperature glaze firing, typically between 2165°F and 2345°F (1185°C and 1285°C). Let the kiln cool completely before handling the finished piece.
Conclusion
Creating a ceramic pipe is both an art and a science that requires meticulous attention to detail throughout each step of the process. From selecting the right clay to mastering the techniques of shaping and decorating, every phase is crucial in ensuring a functional and beautiful end product. Taking the time to properly wedge the clay, carefully shape the pipe, and apply the right glazes contributes to both the durability and aesthetic appeal of the final piece. Thanks for reading our blog post on how to make ceramic pipes! We hope you found it helpful and informative.
Specialization:
- Master of wheel-throwing, hand-building, and advanced glazing techniques
- Focus on creating both functional pottery and decorative art pieces
Recognition:
- Celebrated by collectors and art enthusiasts for creating one-of-a-kind pieces that blend artistry with functionality
- Participates in local and national exhibitions, earning accolades for his innovative designs and craftsmanship
Passion:
- Deeply committed to exploring and pushing the boundaries of ceramic artistry
- Continuously experiments with new materials, firing techniques, and artistic concepts to evolve his craft
Personal Philosophy:
- Believes in the transformative power of art, aiming to evoke emotions and connections through his ceramic creations
- Advocates for sustainability in ceramics, using eco-friendly materials and practices whenever possible