Raw glazing involves the application of a glaze directly onto unfired or “green” ceramic clay. This technique bypasses the need for a bisque firing, integrating the bisque and glaze firing into a single, efficient process. For potters, this approach reduces firing costs and time consumption and opens the door to achieving unique aesthetic finishes that are difficult to obtain with traditional methods.
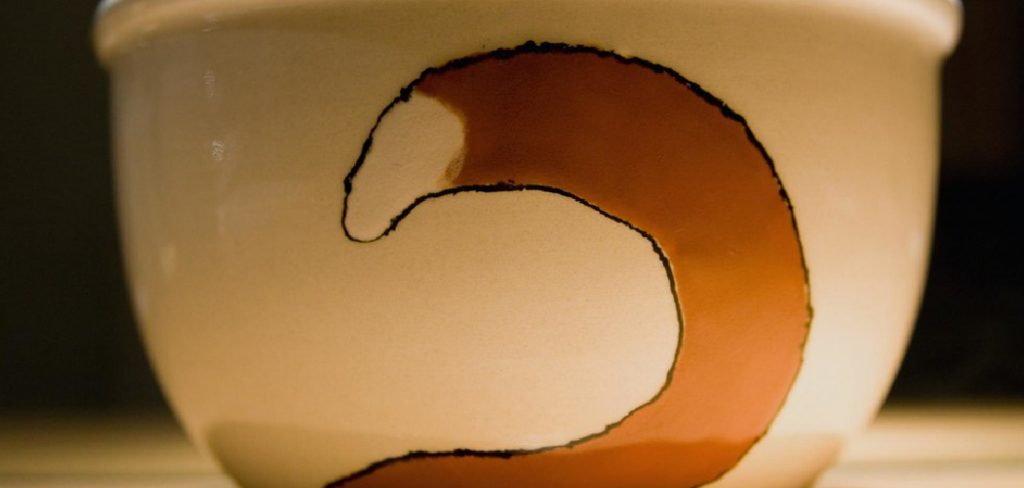
The potential for rich textures and striking glaze patterns makes raw glazing appealing for many ceramic artists. This article aims to guide readers through the essential steps, benefits, and considerations surrounding the practice of raw glazing. By exploring how to use raw glazes on ceramic pieces, readers will gain insights into mastering this innovative technique, enhancing both their creative endeavors and practical understanding of ceramic artistry.
Understanding Raw Glazes and Their Composition
What Raw Glazes Are
Raw glazes, known as greenware, are specially formulated to be applied directly onto unfired ceramic surfaces. Unlike traditional glazes, which are applied to bisque-fired pieces, raw glazes bypass the initial bisque-firing phase. This unique formulation involves selecting materials that can handle the complete firing process in one go, requiring careful attention to the chemical interactions that occur during the single firing. The chemical reactions in raw glazes necessitate controlled compositional adjustments to ensure they bond correctly with the clay body. As the glaze undergoes melting and fluxing, these reactions contribute to the final finish, producing vibrant colors or subtle textures that are distinct from raw glazing.
Types of Glazes Suitable for Raw Glazing
Choosing the right type of glaze is crucial for successful raw glazing. Commonly used varieties include high-fire and stoneware glazes, known for their stability and ability to develop rich, complex surfaces. High-fire glazes typically contain higher fluxes, promoting a durable and smooth finish. On the other hand, stoneware glazes offer a broader range of finishes, from matte to glossy, making them versatile for artistic expression. When selecting a glaze, considerations like desired color, texture, and clay body type are essential, as these factors determine the overall aesthetic outcome of the finished piece.
Pros and Cons of Using Raw Glazes
Advantages of Raw Glazing
One of the primary advantages of raw glazing is its economic and time-saving aspect, as it eliminates the need for separate bisque firing. Potters can effectively reduce energy consumption and overall production costs by integrating both the bisque and glaze firing into a single process. Moreover, raw glazing offers the potential to create unique aesthetic results, allowing for intricate designs that feature dramatic layering and captivating textures. This technique can produce dynamic finishes, enhancing ceramic pieces’ tactile and visual appeal, which are often difficult to achieve through traditional glazing methods.
Limitations of Raw Glazing
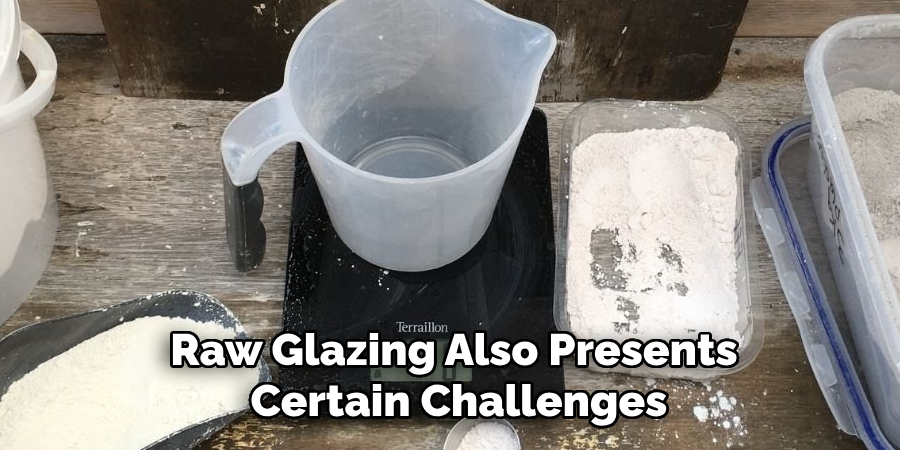
Despite its advantages, raw glazing also presents certain challenges. Applying glaze directly to unfired clay poses a risk of cracking, crawling, or other defects during firing. Greenware’s susceptibility to moisture and handling errors can result in imperfections in the final product. Additionally, selecting suitable glazes is limited, requiring a comprehensive understanding of their chemical properties to ensure they adhere properly during the single firing process. Careful handling and precise application techniques are essential to minimize problems and achieve consistently successful results with raw glazing.
Preparing the Ceramic Surface for Raw Glazing
Prepping Greenware
Preparing greenware for raw glaze application is a critical step to ensure success. Begin by carefully smoothing the ceramic surface using fine-grit sandpaper or a soft sponge to remove any roughness or imperfections. This process helps achieve an even glaze coat by eliminating areas where the glaze might pool. Equally important is removing all dust and debris, which can be accomplished by gently wiping the piece with a slightly damp cloth. Ensuring that the surface is clean and dry before applying the glaze is essential, as any residue can affect adhesion and create defects in the glaze finish.
Choosing the Right Glaze Application Method
Selecting the appropriate method for applying raw glaze can significantly influence the final outcome. Common techniques include dipping, brushing, and spraying. Dipping involves submerging the piece into the glaze, which is efficient for uniformly covering simple shapes. Brushing is suitable for intricate designs, allowing for precise control over glaze placement on detailed areas. Spraying is ideal for large or complex surfaces, providing an even coat without direct contact. Consider the ceramic piece’s size, shape, and detail when choosing an application method, as these factors will guide you to the most effective technique for achieving your desired texture and finish.
How to Use Raw Glazes on Ceramic: Techniques for Applying Raw Glazes
Brushing Raw Glaze
When applying raw glaze with a brush, use a soft-haired brush to gently and evenly cover the surface of the greenware. Start from the middle of the piece and work outward in smooth, overlapping strokes to ensure an even application. Select a finer brush for detailed or small pieces to navigate precise areas without over-saturating. To control thickness, apply multiple thin layers, allowing each to dry slightly before proceeding to the next. This approach reduces the risk of runs and maintains clarity in intricate designs, ensuring a consistent finish.
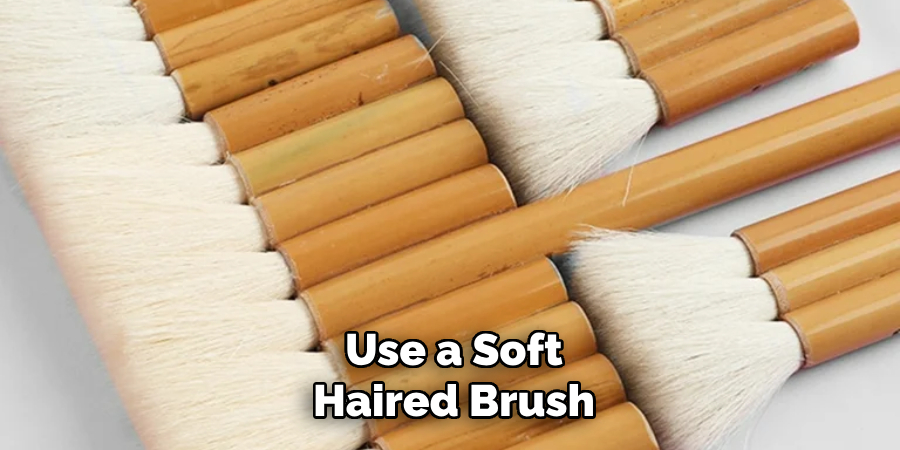
Dipping Greenware into Raw Glaze
Dipping is an efficient method for glazing simple shapes. Begin by filling a wide, stable bucket with your chosen glaze, ensuring it is well-mixed for uniformity. Hold the greenware firmly and dip it into the glaze, fully immersing it in a smooth, steady motion. Keep the piece in the glaze briefly, then slowly lift it out, allowing excess glaze to drip off. To prevent bubbles and uneven spots, gently tap the bottom edge of the piece on the bucket’s rim or lightly blow across the surface. Rotate the piece if needed to ensure balance and even coating.
Spraying Glaze
Spraying glaze is ideal for large or complex surfaces, providing a uniform coat with minimal handling. Use a spray gun or airbrush for precise control over coverage. Always wear a mask and spray in a well-ventilated area or spray booth to ensure safety. Adjust the spray nozzle for a fine mist, and maintain a consistent distance from the piece while spraying in overlapping passes. Test the spray on a sample piece to calibrate the thickness. By moderating the pressure, distance, and speed of the spray, you can achieve a smooth, even layer that enhances the aesthetics of the raw-glazed piece.
Drying and Handling Raw-Glazed Pieces
Allowing Glaze to Set on Greenware
Letting the glaze fully dry on greenware minimizes handling risks and prevents defects. Adequate drying time ensures that the glaze adheres properly, reducing the likelihood of smudging or uneven surfaces. To facilitate drying, set the glazed pieces on racks or drying boards with ample airflow, taking care not to overcrowd them. Ensure the racks are stable and level to prevent imbalances that could lead to distortion or damage before firing.
Avoiding Common Handling Mistakes
When moving or storing raw-glazed pieces, caution is essential to prevent chipping or cracking. Padded supports or soft cloths to cushion the pieces, especially around delicate edges or thin sections. Store pieces in a low-traffic area to avoid accidental bumps or drops. Ensure there’s enough space between items to prevent contact during storage. By taking these precautions, you safeguard the integrity of the glaze and prepare the pieces optimally for a successful firing.
Single-Firing Raw-Glazed Pieces
Firing Temperature and Schedule
Successfully single-firing raw-glazed ceramics requires careful attention to the kiln settings and firing schedule. Begin with a slow ramp-up to reach the desired bisque temperature, allowing the greenware to gradually adjust and minimize moisture-related issues. Aim for a gradually increasing temperature curve to reduce strain on the piece. After reaching the peak temperature necessary for glaze maturation, ensure a controlled cooling process to avoid rapid temperature changes that could cause warping or thermal shock. Adjust your schedule based on the specific clay and glaze combination used to optimize results and avoid potential imperfections.
Monitoring the Kiln
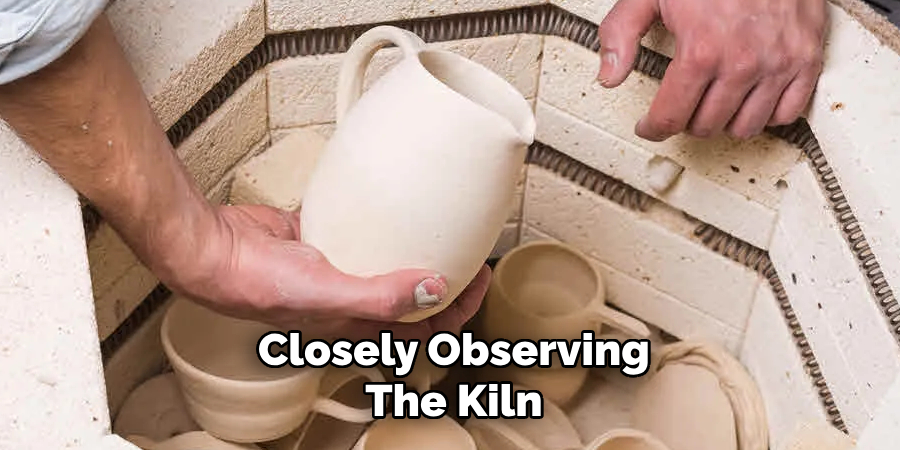
Closely observing the kiln during the early stages of firing is crucial for identifying any immediate glaze defects, such as cracks or pinholes. Visual inspections through the kiln’s peephole or small test pieces can provide early warnings. If issues arise, be prepared to make mid-firing adjustments by altering the temperature or extending hold times to correct discrepancies. This proactive approach allows for immediate corrections, ensuring the quality and integrity of the final ceramic piece.
Post-Firing Tips: Assessing the Results and Troubleshooting
Inspecting Finished Pieces
Once the firing process is complete, it’s essential to thoroughly inspect each piece for any glaze defects like pinholes, crawling, or uneven texture. Carefully examine the surface under good lighting, looking for any irregularities that might have developed during firing. Pay special attention to areas that are prone to defects, such as edges and detailed sections. Evaluate the overall finish and durability of the glaze, assessing factors like smoothness, color consistency, and adherence. The success of the raw glazing technique can be measured by a uniform, durable glaze that enhances the aesthetic appeal of the ceramic piece.
Troubleshooting Common Glaze Defects
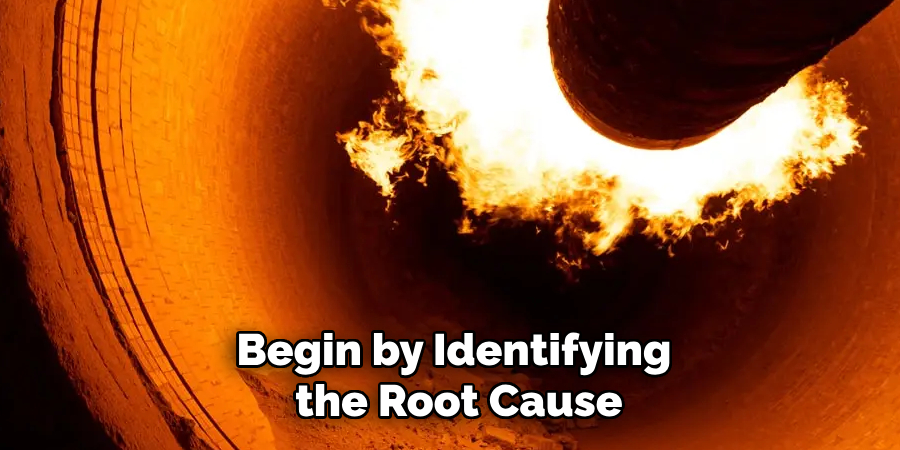
Encountering issues such as cracking, bubbles, or uneven color is not uncommon and allows you to refine your glazing techniques. Begin by identifying the root cause, which could be due to application errors, firing schedule, or the specific glaze formula used. For future projects, experiment with altering the thickness of the glaze application or adjusting the firing ramp-up and cooling rates. Ensuring that the glaze is well-mixed and the application is consistent can prevent many defects. By systematically analyzing and adjusting your methods, you can enhance the quality of the glaze finish and improve results with each subsequent firing.
Safety Considerations When Working with Raw Glazes
Handling Glaze Materials Safely
Ensuring a well-ventilated workspace and utilizing appropriate protective gear, such as gloves, masks, and eye protection, is crucial when working with raw glaze materials. These precautions help prevent dust inhalation and safeguard against skin contact with potentially hazardous chemicals that may be present in certain glazes. Routine cleanup and storage protocols also aid in maintaining a safe environment, reducing the risk of contamination and exposure.
Firing Safety Tips
To ensure safety while firing raw-glazed ceramics, maintain regular kiln inspections to detect any mechanical issues early. Consistent monitoring throughout the firing process can help address potential problems promptly. Additionally, proper ventilation in the kiln room is vital to prevent the buildup of harmful fumes. This can be achieved by using exhaust fans or ensuring that ventilation systems are working efficiently, providing a safe and comfortable space for frequent operations.
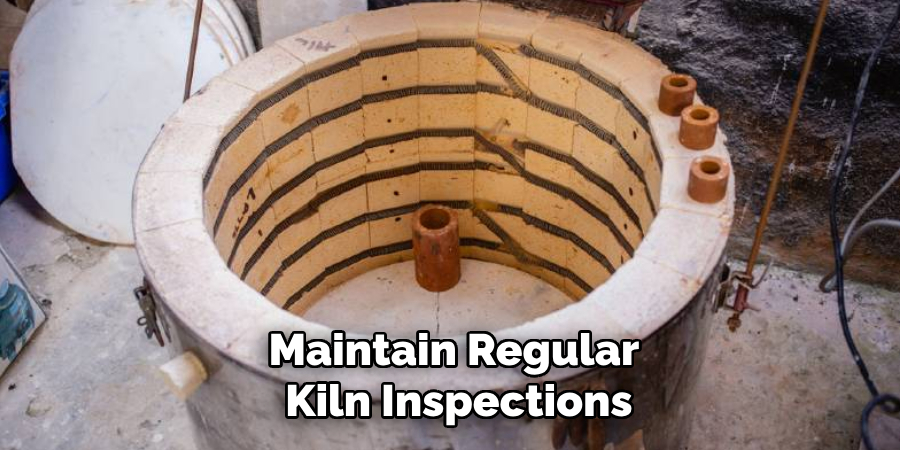
Conclusion
The raw glazing process offers a transformative approach to ceramic artistry, enabling potters to achieve unique and vibrant finishes in a single firing. Understanding how to use raw glazes on ceramic involves carefully managing glazing techniques, drying, and firing schedules to minimize defects and maximize results. Continuously practicing and experimenting with different applications and materials will refine your skills and open up new creative possibilities. Embrace the craftsmanship and patience required for this method, allowing each piece to express its own story. Enjoy the journey of exploration and the satisfaction of crafting exquisite, one-of-a-kind ceramics.
Specialization:
- Master of wheel-throwing, hand-building, and advanced glazing techniques
- Focus on creating both functional pottery and decorative art pieces
Recognition:
- Celebrated by collectors and art enthusiasts for creating one-of-a-kind pieces that blend artistry with functionality
- Participates in local and national exhibitions, earning accolades for his innovative designs and craftsmanship
Passion:
- Deeply committed to exploring and pushing the boundaries of ceramic artistry
- Continuously experiments with new materials, firing techniques, and artistic concepts to evolve his craft
Personal Philosophy:
- Believes in the transformative power of art, aiming to evoke emotions and connections through his ceramic creations
- Advocates for sustainability in ceramics, using eco-friendly materials and practices whenever possible