Setting up kiln shelves correctly is a crucial step in achieving consistent and even firing results in your ceramic projects. Proper shelf arrangement not only ensures adequate airflow but also prevents potential issues like uneven heating or warping.
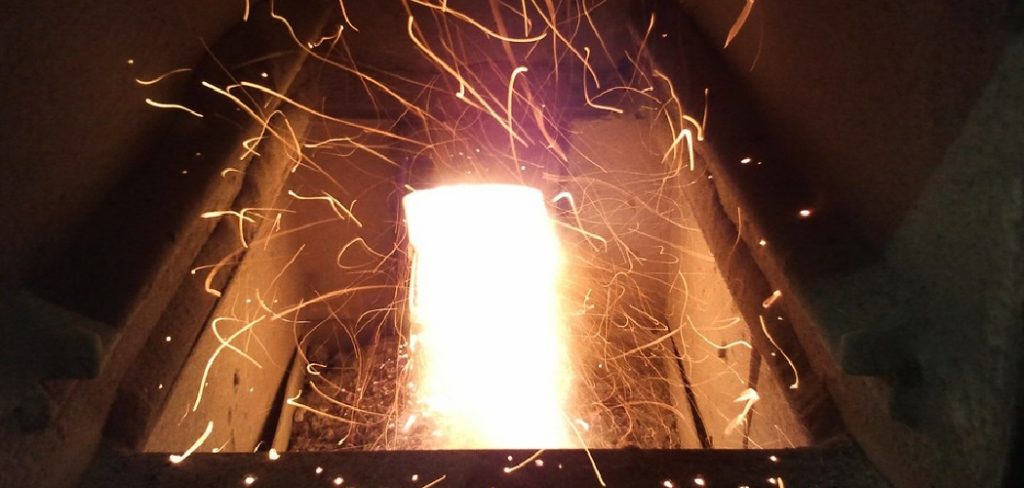
Whether you are firing pottery, sculpture, or glazed work, understanding the basics of kiln shelf organization can make a significant difference in the quality of your finished pieces. This guide will walk you through how to set up kiln shelves for even firing.
Importance of Proper Kiln Shelf Setup
The way you arrange your kiln shelves plays a critical role in the firing process. Proper shelf setup ensures that heat is distributed evenly throughout the kiln, preventing issues like underfired or overfired pieces. Uneven shelf placement can disrupt airflow, creating hot or cold spots within the kiln, which can lead to defects such as cracking, pinholing, or incomplete glaze maturation.
Additionally, a well-organized shelf layout maximizes kiln space, allowing you to fire more pieces per load efficiently. Taking the time to carefully plan and position your kiln shelves ultimately leads to better results, improved stability during firing, and a reduced risk of accidents or damage to your work.
Understanding Kiln Shelves
Kiln shelves are flat, heat-resistant surfaces that serve as the foundation for placing your ceramic pieces inside the kiln. They are typically made from durable materials like cordierite or silicon carbide, which can withstand the extreme temperatures of firing.
Kiln shelves come in various shapes and sizes, allowing them to fit different kiln models and configurations. When choosing shelves for your kiln, consider factors such as thickness, size, and material, as these can significantly impact the overall performance during firing.
Thicker shelves are more durable and resistant to warping, making them ideal for heavy or large ceramic pieces, but they take longer to heat and cool. Thinner shelves, on the other hand, heat up and cool down more quickly, which can save time during the firing process, but they may not support heavier loads as effectively.
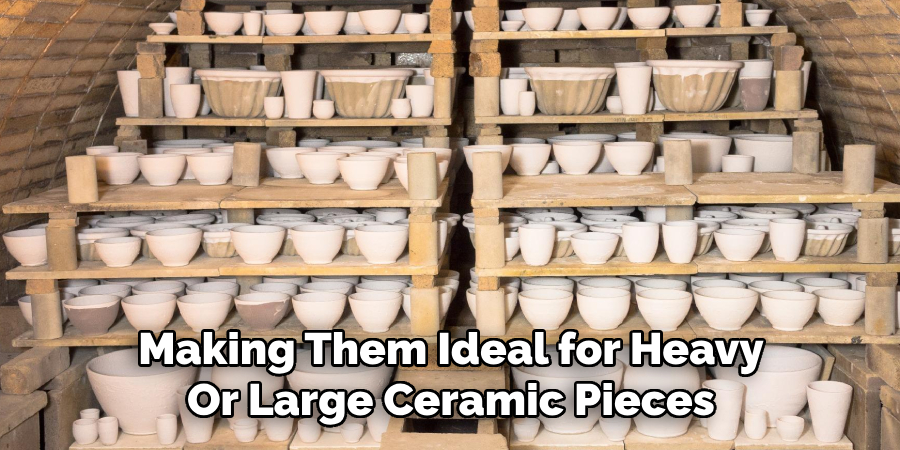
10 Methods How to Set up Kiln Shelves for Even Firing
1. Understand Kiln Shelf Placement Basics
The first step in setting up kiln shelves for even firing is understanding the role of shelf placement within the kiln. The kiln’s interior is divided into several zones, each of which can experience slight temperature differences due to the heating elements. It’s important to note that the bottom and top of the kiln tend to heat more intensely than the middle.
To counteract this natural heat distribution, place the larger pieces near the center of the kiln, and distribute smaller items towards the top and bottom where heat is more concentrated. By understanding these dynamics, you can better arrange your shelves to promote uniform firing and prevent pieces from being overexposed to intense heat.
2. Consider Shelf Material and Size
Choosing the right materials for your kiln shelves is a crucial factor in ensuring an even firing process. Most kiln shelves are made of ceramic material such as cordierite or silicon carbide, both of which are durable and heat-resistant. However, the thickness of the shelf can also impact the firing process.
Thicker shelves can hold heat more effectively but may cause heat to transfer unevenly if stacked incorrectly. For best results, use shelves that are appropriately sized for your kiln, ensuring that they allow for proper airflow while preventing excessive heat buildup. Shelf material and size should align with the kiln’s firing capacity and the types of ceramics you’re working with.
3. Ensure Adequate Air Circulation
Proper airflow within the kiln is essential for even firing. Without good air circulation, heat can become trapped, causing uneven firing, slower heating, and potentially flawed results. To encourage airflow, it’s important to space the shelves evenly within the kiln and avoid overcrowding.
Make sure there’s enough space between the shelves for air to flow freely around the ceramic pieces. In addition, consider the arrangement of the kiln shelves so that there are no blockages or obstructions that could restrict the flow of heated air. A well-ventilated kiln setup promotes uniform heat distribution and helps to achieve consistent firing temperatures throughout the kiln.
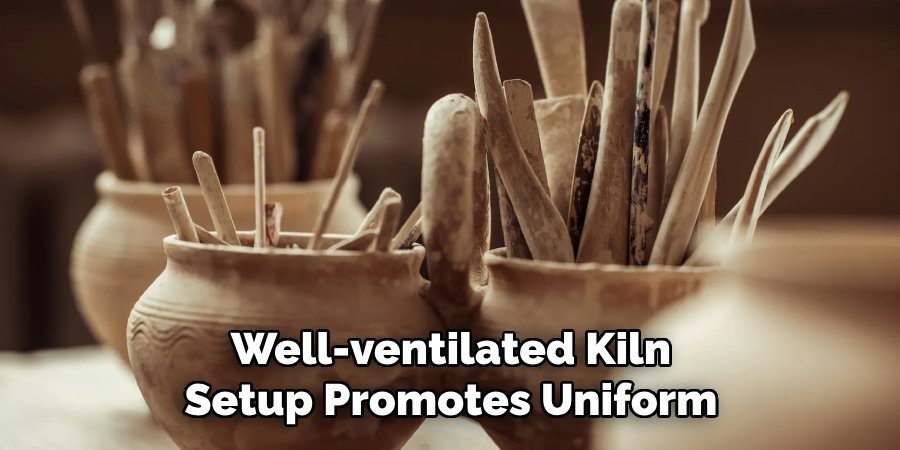
4. Use Kiln Posts for Shelf Support
Kiln posts are essential for elevating and supporting your kiln shelves. These posts prevent the shelves from sitting directly on top of one another, which could cause uneven heating or a lack of airflow. The size and spacing of the posts are crucial for maintaining balance and stability within the kiln.
Use kiln posts that are the appropriate height for your kiln size, ensuring that there is enough clearance between each shelf. Additionally, posts made from high-temperature resistant materials, such as refractory materials, are the best choice for ensuring a reliable and durable shelf setup. Kiln posts also provide essential support for heavy ceramic pieces and prevent shelf warping under intense heat.
5. Arrange Shelves in a Staggered Pattern
When setting up multiple shelves, avoid stacking them directly on top of one another in a perfectly aligned pattern. Instead, stagger the shelves slightly to promote better airflow and reduce the chances of creating “hot spots” or uneven heat distribution. Staggering the shelves will create gaps in the vertical arrangement, allowing air to circulate more freely between them.
The staggered design helps maintain a uniform temperature throughout the kiln, resulting in a more even firing process. The staggered pattern also prevents the possibility of one shelf blocking the heat from reaching others, ensuring all your ceramic pieces receive the appropriate amount of exposure to heat.
6. Leave Space for Larger Pieces
If you plan to fire large pieces, it’s important to leave adequate space around them to avoid overcrowding. A cramped setup can inhibit airflow and prevent the piece from firing evenly. When setting up your kiln shelves, position the larger pieces towards the center of the kiln, as this area typically experiences the most even heat distribution.
Be mindful of the size and shape of your pieces, ensuring there is sufficient space around them to allow for air circulation. You may need to adjust the shelf placement or add additional posts to accommodate larger pieces without disrupting the kiln’s overall balance.
7. Organize Shelves Based on Firing Phases
Different stages of the firing process can affect your pieces in different ways. For instance, in the early stages of firing, the pieces are more sensitive to heat, and during the cooling process, thermal shock is a potential risk. To address this, consider organizing your kiln shelves based on the firing phase your pieces are in.
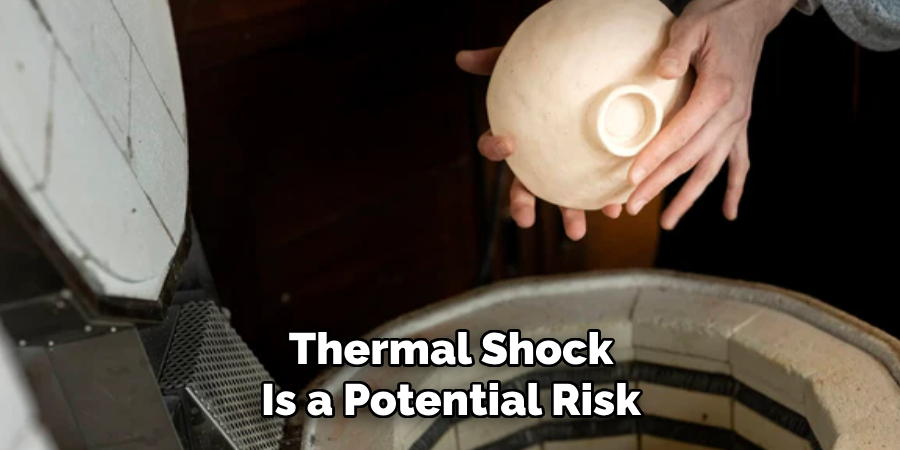
For example, during the bisque firing phase, place more delicate, smaller pieces on the upper shelves where heat is less concentrated. As the firing moves toward higher temperatures, you can adjust shelf placement to allow for optimal heat exposure. Managing shelf placement based on firing phases helps to protect the ceramics and encourages more even firing outcomes.
8. Monitor Shelf Positioning with a Thermocouple
Using a thermocouple to monitor temperature at different points within your kiln can provide valuable insights into how heat is being distributed. This device measures the temperature at various locations within the kiln, helping you assess if there are any hot spots or areas that may require adjustment.
By strategically placing the thermocouple near the shelves, you can gain a clear understanding of how evenly the heat is distributed and adjust the shelf arrangement if necessary. This method is particularly useful if you find that some pieces are over-fired or under-fired due to uneven heat.
9. Avoid Overloading the Kiln
One of the most common mistakes when setting up a kiln is overloading it with too many pieces. While it may seem tempting to maximize the kiln’s capacity, this can result in uneven firing and insufficient airflow, leading to poor results. Instead of overstuffing the kiln, carefully arrange your ceramics to allow for optimal space between them.
By leaving space between each piece, you ensure that heat can reach every part of your ceramic ware. Overloading can also affect the efficiency of the firing process, leading to longer firing times and potential firing issues. A properly loaded kiln promotes consistent temperatures and more predictable results.
10. Regularly Rotate and Reorganize Shelves
Even with careful planning and arrangement, the firing process can create subtle imbalances or uneven wear on your kiln shelves. It’s important to regularly rotate and reorganize the placement of your shelves to ensure that all shelves are exposed to the same conditions.
Over time, the shelves may warp or accumulate residue from the glaze or firing materials, which could impact heat distribution. Periodically inspect the shelves for any signs of wear and make adjustments as needed. Regularly rotating and cleaning your kiln shelves ensures that the kiln performs optimally for each firing, leading to consistent results across different batches of ceramics.
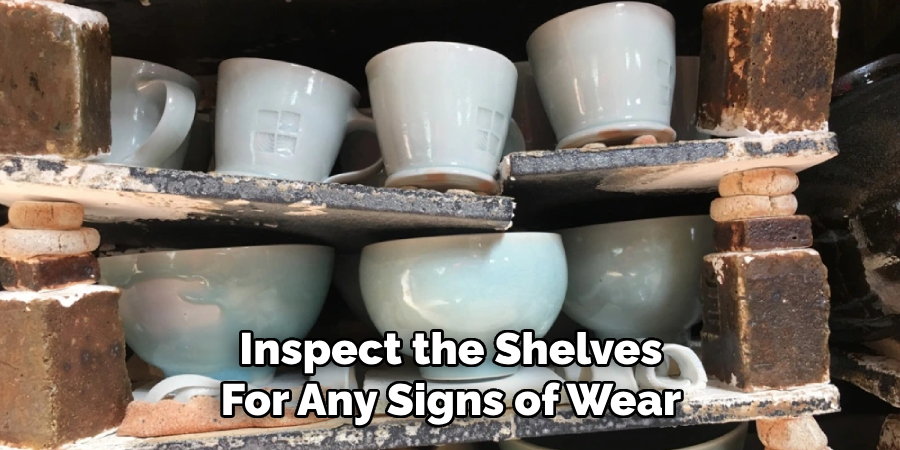
Conclusion
Setting up kiln shelves for even firing is an essential skill for any ceramicist. Properly arranged shelves not only enhance airflow and temperature distribution but also protect your work and ensure that each piece is fired to perfection. So, there you have it – a quick and easy guide on how to set up kiln shelves for even firing.
Specialization:
- Master of wheel-throwing, hand-building, and advanced glazing techniques
- Focus on creating both functional pottery and decorative art pieces
Recognition:
- Celebrated by collectors and art enthusiasts for creating one-of-a-kind pieces that blend artistry with functionality
- Participates in local and national exhibitions, earning accolades for his innovative designs and craftsmanship
Passion:
- Deeply committed to exploring and pushing the boundaries of ceramic artistry
- Continuously experiments with new materials, firing techniques, and artistic concepts to evolve his craft
Personal Philosophy:
- Believes in the transformative power of art, aiming to evoke emotions and connections through his ceramic creations
- Advocates for sustainability in ceramics, using eco-friendly materials and practices whenever possible