Are you a pottery enthusiast? Or perhaps you’re just starting to dabble in glazing and want to ensure your pieces turn out perfectly every time.
How to seal a glaze properly properly is a crucial step in ensuring the longevity and durability of your finished surface, whether it’s pottery, woodwork, or another creative project. A well-applied sealant enhances the appearance by providing a smooth, glossy finish and protects the material from wear, moisture, and damage over time. This process requires attention to detail, the right tools, and understanding the type of glaze and surface you’re working with.
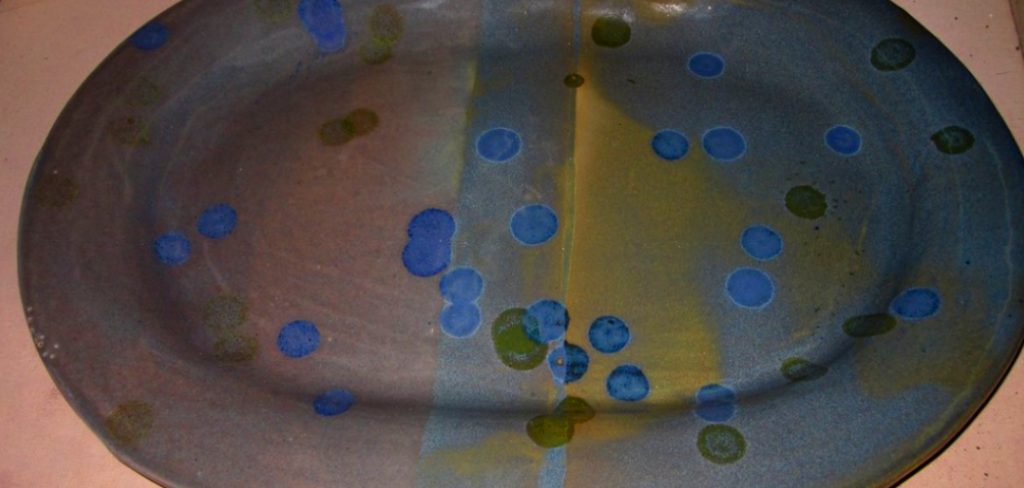
By following the correct techniques, you can achieve professional-quality results that stand up to the test of time.
What Are the Benefits of Sealing a Glaze?
Before we dive into how to seal a glaze properly, let’s first discuss why it’s important. There are several benefits to sealing a glaze:
- Protection: As mentioned before, sealing a glaze protects against wear and tear, moisture, and damage from UV rays. This is especially important if your piece will be used outdoors or in high-traffic areas.
- Durability: A sealed glaze has an increased level of durability compared to an unsealed one. It can withstand everyday use without showing signs of wear or discoloration.
- Appearance: A sealant not only protects but also enhances the appearance of a glazed surface by providing a smooth, glossy finish. This is especially important for pottery pieces that are meant to be admired and displayed.
- Longevity: A properly sealed glaze can extend the lifespan of your project by protecting it from environmental factors that may cause damage over time.
These benefits make sealing a glaze an essential step in the finishing process for any creative project.
What Will You Need?
Before you begin sealing your glaze, make sure you have the following materials on hand:
- Sealant: There are various types of sealants available, such as polyurethane, lacquer, and varnish. Make sure to choose one suitable for the type of glaze and surface you’re working with.
- Paintbrushes: You’ll need different paintbrushes depending on your project’s size and intricacy.
- Sandpaper: This will smooth out imperfections or rough areas before applying the sealant.
- Tack cloth: This sticky cloth removes dust or debris from the surface before sealing.
- Safety equipment: Depending on the type of sealant you choose, you may need to wear gloves, a mask, and protective eyewear while applying it.
Once you have the necessary materials, you can start sealing.
10 Easy Steps on How to Seal a Glaze Properly
Step 1: Prepare Your Workspace
Start by setting up a clean and well-ventilated workspace. Lay down a protective covering, such as newspaper or a drop cloth, to protect your surfaces from spills or drips. Ensure the area is free from dust and debris, as these can affect the final finish of your project. Suppose you’re working indoors, open windows or use a fan to improve air circulation, mainly if your sealant emits strong fumes. Assemble all your materials within easy reach to streamline the process.
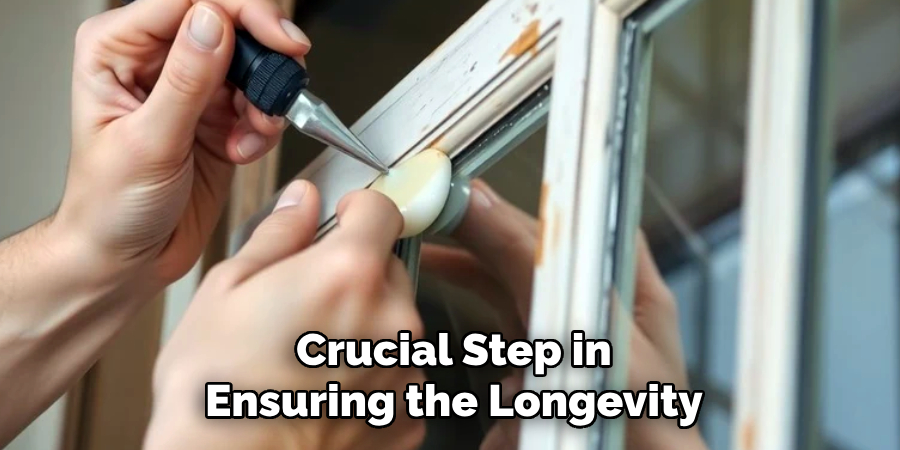
Step 2: Clean the Surface
Thoroughly clean the surface you are planning to seal. Use a mild detergent and water to remove dirt, grease, or any other contaminants. Rinse the surface with clean water and allow it to dry completely before proceeding. If the surface has old sealant or grime that won’t come off, consider using a scraper or sandpaper to ensure a smooth and even base for the new sealant. Cleaning is essential for proper adhesion and a flawless finish.
Step 3: Apply the Sealant
Once the surface is clean and dry, it’s time to apply the sealant. Begin by cutting the tip of the sealant tube at a 45-degree angle using a utility knife, then pierce the inner seal with a long nail or similar tool. Load the sealant tube into your caulking gun. Hold the gun at an angle and apply an even bead of sealant along the area you want to seal, moving steadily and avoiding gaps. Use a gloved finger or a caulking tool to smooth the sealant, ensuring it adheres properly and creates a uniform finish. Wipe away any excess sealant immediately with a damp cloth to maintain a neat appearance.
Step 4: Allow the Sealant to Cure
After applying the sealant, it is crucial to allow it sufficient time to cure. Refer to the manufacturer’s instructions for the recommended curing time, which typically ranges from 24 to 48 hours. To ensure the sealant sets properly, avoid exposing the sealed area to water, dirt, or heavy use during this period. Proper curing will help achieve a durable, long-lasting seal that effectively protects against moisture and wear.
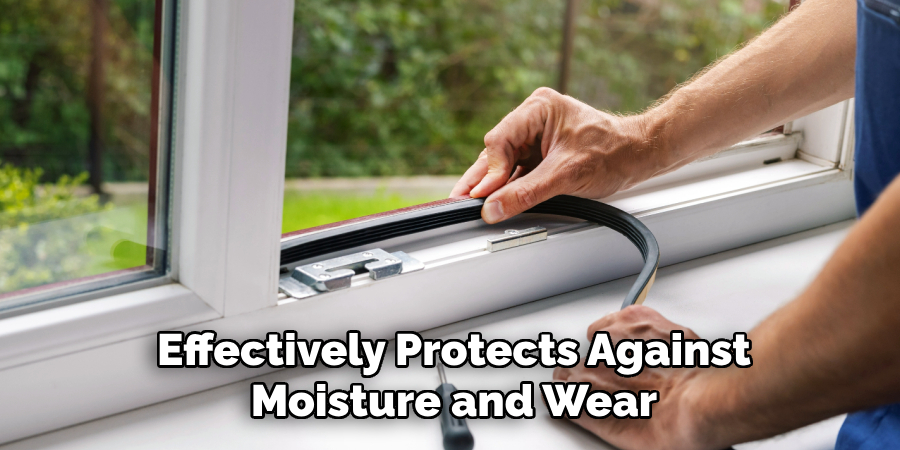
Step 5: Test the Seal
Once the sealant has fully cured, inspect the sealed area to ensure no gaps, cracks, or weak points. Gently test the seal by applying light pressure or small amounts of water, checking for any leaks or movement. If the seal appears secure and intact, the application process is complete. If issues are detected, reapply the sealant to the affected areas, following the same steps to ensure a proper seal.
Step 6: Maintain the Sealed Area
After ensuring the seal is secure, clean up any excess sealant or tools used during the application process. Dispose of any waste materials according to local regulations. To maintain the sealed area, periodically inspect it for signs of wear, cracks, or damage, especially in high-exposure environments. Promptly address any issues by reapplying sealant as necessary to extend the life and effectiveness of the seal. Routine maintenance will ensure long-term protection and durability.
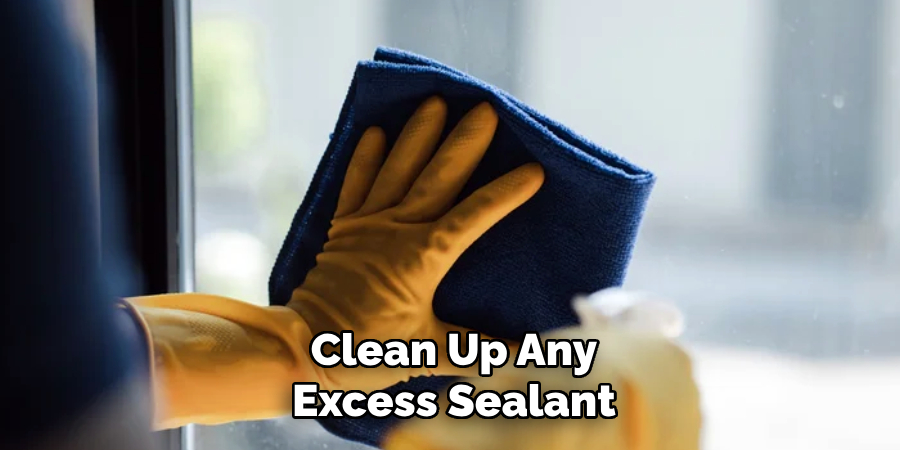
Step 7: Final Inspection and Testing
Once the cleanup process is complete, a final inspection of the sealed area will be conducted. Look for any overlooked gaps, uneven application, or inconsistencies in the sealant. If the seal will be exposed to water or other elements, perform a small-scale test, such as spraying water or simulating the conditions the seal will face. This step ensures the sealant is fully practical and ready to withstand its intended use. Make any final adjustments as needed to guarantee optimal performance.
Step 8: Documentation and Recordkeeping
Keep detailed records of the sealing project for future reference. Document the type and quantity of sealant used, the date of application, and any specific environmental conditions during the process. Take clear photographs of the sealed area before and after the application. This documentation can be helpful for warranty claims, future repairs, or maintenance schedules. Proper recordkeeping ensures that all necessary information is easily accessible if issues arise later.
Step 9: Keep Safety in Mind
Throughout the sealing process, prioritize safety by wearing appropriate protective equipment. If you are using a sealant with strong fumes or chemicals, work in a well-ventilated area and wear a mask and gloves to protect yourself from inhaling or coming into contact with harmful substances. Always read and follow the manufacturer’s instructions for safe handling and use of the sealant.
Step 10: Dispose of Materials Properly
Once you have completed the sealing process, dispose of any remaining materials according to local regulations. If your chosen sealant is hazardous waste, take it to an approved disposal facility or consult your local waste management department for proper disposal methods. Do not pour sealant down drains; it can cause clogs and harm the environment. Proper disposal is essential for maintaining a healthy and safe workspace and minimizing potential environmental impact.
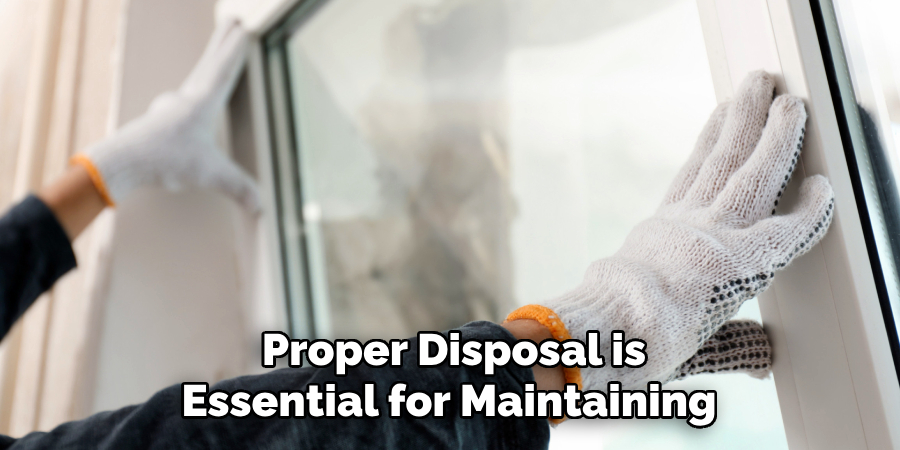
By following these steps and precautions, you can successfully seal various surfaces in your home or workplace.
5 Things You Should Avoid
1. Applying Glaze on a Dirty Surface: Ensure the surface is clean and free of dust, grease, or contaminants. Neglecting this step can lead to poor adhesion and an uneven finish.
2. Skipping the Curing Time: Allow the glaze to cure correctly as recommended by the manufacturer. Not giving adequate time may affect the durability and appearance of the seal.
3. Using the Wrong Tools: Using inappropriate brushes, rollers, or applicators can result in streaks, bubbles, and a subpar finish. Choose tools designed explicitly for glazing work.
4. Overloading the Glaze: Applying too much glaze in one coat can lead to drips, pooling, and extended drying times. Always aim for thin, even coats to achieve the best results.
5. Ignoring Environmental Conditions: Humidity, temperature, and airflow can drastically affect the glaze’s performance. Avoid sealing in extreme conditions, such as high humidity or freezing temperatures, to prevent compromised results.
Conclusion
Properly sealing a glaze is a meticulous process that requires attention to detail, patience, and the correct tools.
You can achieve a professional and long-lasting finish by ensuring the surface is clean, respecting curing times, selecting the right applicators, applying thin, even coats, and being mindful of environmental conditions. Taking the time to follow these steps will not only enhance the appearance of your project but also improve its durability, ensuring a polished and enduring result.
Hopefully, the article on how to seal a glaze properly has provided you with the necessary information and guidance to complete any glazing project successfully. So go ahead and confidently seal your next glazing project! Happy sealing!