Are you worried your kiln might not give you the correct temperature readings? Accurate temperature measurement is crucial for successful results in pottery and ceramic projects.
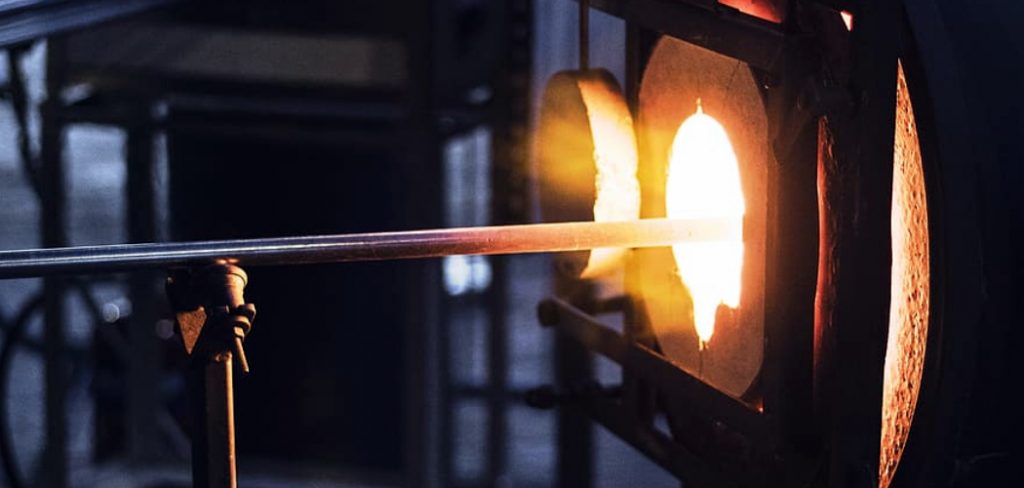
Testing the accuracy of your kiln’s temperature is critical in ensuring consistent and reliable results for your projects, whether in ceramics, glasswork, or metalwork. Over time, kilns can experience temperature variations due to wear, calibration issues, or faulty components. By regularly verifying and adjusting the temperature settings, you can prevent under-firing or over-firing, which can compromise the quality of your work.
This guide on how to test kiln temperature accuracy will walk you through practical methods to assess your kiln’s temperature accuracy and ensure optimal performance for your creations. Let’s get started!
What Are the Benefits of Testing Kiln Temperature Accuracy?
Before we dive into the testing methods, let’s first understand why it’s essential to check your kiln’s temperature accuracy regularly.
- Consistent Results: Accurate temperature control is crucial for achieving consistent pottery and ceramic work results. Regularly testing your kiln’s temperature ensures that your pieces are fired at the correct temperatures, resulting in consistent quality and appearance.
- Prevents Damage to Work: Over-firing or under-firing can cause damage to your pieces, such as warping, cracking, or discoloration. You can avoid these issues by testing and adjusting the temperature settings.
- Saves Time and Money: Inaccurate temperature readings can lead to wasted time and money on projects that don’t turn out as desired. By testing and calibrating your kiln, you can avoid costly mistakes and ensure efficient use of materials.
- Safety: A malfunctioning kiln with inaccurate temperature readings can be a safety hazard. Regularly testing the accuracy ensures that your kiln functions correctly and reduces the risk of accidents or fires.
These are just a few benefits of testing your kiln’s temperature accuracy. Now, let’s look at practical methods for assessing and adjusting your kiln’s temperature.
What Will You Need?
To test your kiln’s temperature accuracy, you will need the following items:
- An infrared thermometer or temperature probe
- A pyrometer (optional)
- Small pieces of Cone 04 clay
- Kiln safety gear (gloves, goggles, etc.)
Once you have gathered these materials, you’re ready to begin testing.
10 Easy Steps on How to Test Kiln Temperature Accuracy
Step 1. Prepare Your Kiln
Begin by ensuring your kiln is clean and free of debris or obstructions. This is crucial for obtaining accurate temperature readings and preventing any material from interfering with the test. Remove leftover glaze, clay, or other residues from previous firings. Inspect the kiln shelves and bricks for signs of wear or damage that could affect heat distribution.
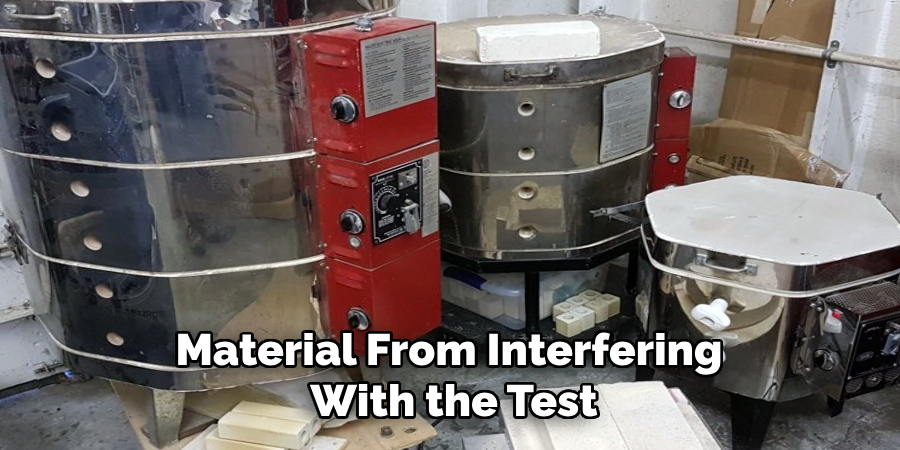
Next, confirm that all electrical connections and kiln components, such as the heating elements, are in good condition. Any damage or deterioration could lead to uneven heating or unreliable results. Also, double-check that your kiln’s thermocouple (the device that measures the internal temperature) is properly installed and free from damage, as this will play a vital role in ensuring temperature accuracy.
Lastly, position any tools or equipment, such as the infrared thermometer or temperature probe, close to the kiln for easy access during testing. Having your testing tools ready and within reach will streamline the process and minimize any disruptions once the kiln is active.
Step 4: Perform a Test Firing
Before using the kiln for a project, conduct a test firing to ensure everything functions correctly. Start by setting the kiln to a low temperature and gradually increase it according to the manufacturer’s recommendations. Monitor the heating process closely, keeping an eye on the temperature readings to confirm they align with the intended settings. During the test firing, listen for unusual noises and watch for any signs of malfunction, such as uneven heating, error messages, or abnormal odors. Once the firing is complete, allow the kiln to cool fully and inspect the results to verify that the test was successful.
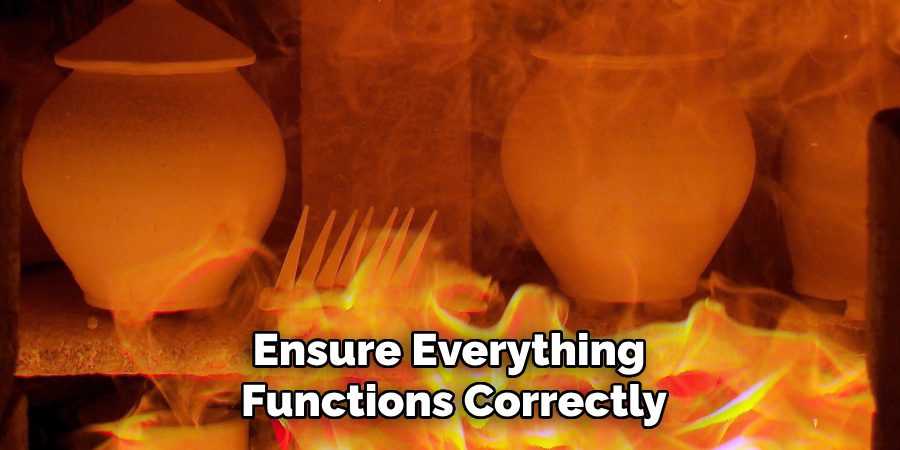
Step 5: Load the Kiln Properly
You are ready to load your materials once you have completed the test firing and confirmed that the kiln is functioning correctly. Begin by arranging the items inside the kiln to ensure even heat distribution. Use kiln shelves and supports if necessary to prevent any pieces from touching each other or the walls of the kiln, as this could cause damage during firing. Be mindful of spacing to allow proper airflow and consistent heating.
Step 6: Set the Firing Schedule
With the kiln adequately loaded, the next step is to program the firing schedule. Select the appropriate firing profile for your materials, such as bisque, glaze, or specialized firing programs. Input the required temperature, ramp rates, and hold times as specified for the pieces you are working on. Ensure the schedule matches the material and glaze requirements to avoid defects like cracking or under-firing. Double-check the settings before starting the kiln to ensure accuracy. A well-planned firing schedule is essential for achieving consistent and high-quality results.
Step 7: Start the Kiln and Monitor the Process
Once the firing schedule is set, you can start the kiln and begin the firing process. Regularly monitor the kiln, especially during the initial phase, to ensure it functions correctly and reaches the desired temperatures as programmed. Monitor any warning indicators or odd behaviors that may signal an issue with the kiln. Maintaining a safe distance and following all safety protocols during the firing process is also essential. Avoid opening the kiln while it is firing, as sudden changes in temperature can damage the pieces inside and pose a safety hazard. Monitoring the process ensures that the firing proceeds smoothly and allows quick action if any adjustments or interventions are needed.
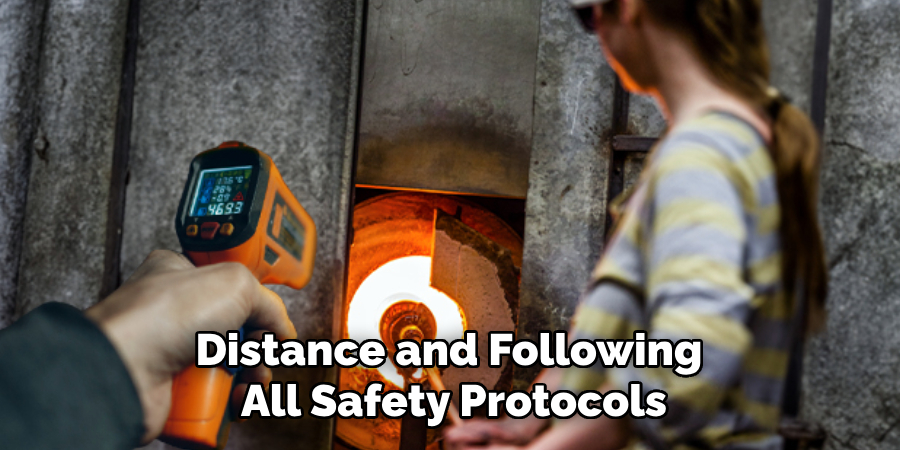
Step 8: Cool Down and Unload the Kiln
After the firing process is complete, allow the kiln to cool down completely before opening it. This cooling phase is crucial, as sudden temperature changes can lead to cracking or other damage to the fired pieces. Be patient and follow the recommended cooling schedule for your specific kiln and materials. Once the kiln has reached a safe temperature, carefully open it and inspect the pieces. Use protective gloves to handle the items, especially if they are still slightly warm. Take note of the results and document any observations for future firings, as this can help improve your process over time.
Step 9: Finishing and Storing Your Pieces
Once the pieces have been fully cooled from the kiln, inspect them thoroughly for any imperfections, cracks, or surface issues. You can apply additional finishes such as glazing, polishing, or painting to enhance their appearance and durability. Ensure the pieces are clean and debris-free before applying any final touches. After finishing, store your pieces in a dry and safe location to protect them from potential damage. Proper storage will ensure that your creations remain in good condition and are ready for use or display.
Step 10: Cleaning and Maintaining Your Kiln
Properly maintaining your kiln is essential to ensure consistent performance and longevity. After each use, allow the kiln to cool completely before cleaning. Remove debris, such as broken pieces or residual materials, from the kiln chamber using a soft brush or vacuum designed for high-temperature equipment. Inspect the heating elements and interior surfaces for signs of wear or damage and address any minor issues before they escalate into more significant problems. Regularly check and replace any damaged kiln shelves or supports, as these can affect the quality of your firings. A consistent maintenance routine will help keep your kiln in optimal condition for future projects.
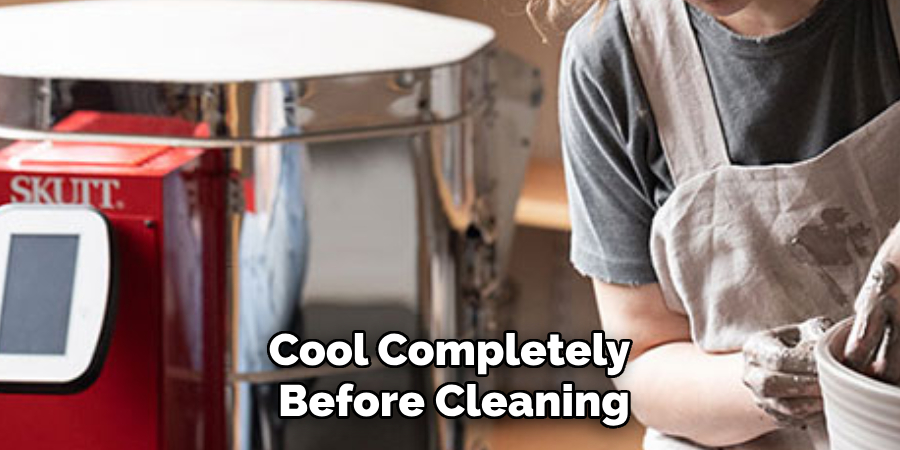
Following these steps and maintaining your equipment can ensure successful and safe firings for all your ceramic projects.
5 Things You Should Avoid
1. Skipping Calibration: Avoid skipping the regular calibration of your kiln. Even minor inconsistencies in temperature readings can lead to inaccuracies over time, potentially ruining your projects.
2. Using Improper Tools: Do not use tools or thermometers not explicitly designed for high heat or kiln testing. Improper tools can fail to provide accurate measurements and may get damaged.
3. Ignoring Maintenance: Neglecting routine maintenance and cleaning can affect the performance of your kiln. Dust and debris can obstruct sensors, throwing off temperature accuracy.
4. Relying Solely on Built-In Thermometers: Built-in thermometers, while helpful, can sometimes give misleading readings. Always cross-check with an external thermocouple or pyrometer for better accuracy.
5. Testing with an Empty Kiln: Avoid testing the temperature accuracy of an empty kiln, as this does not reflect normal operating conditions. Always conduct tests with a load similar to what you would typically fire.
Conclusion
How to test kiln temperature accuracy is a crucial step to ensure the success and quality of your firing projects.
By avoiding common mistakes such as neglecting maintenance, using improper tools, or relying solely on built-in thermometers, you can significantly enhance the reliability of your temperature readings. Always cross-check measurements, use appropriate tools designed for high-heat environments, and mimic real operating conditions during tests.
Following these practices will help maintain consistent results, prolong the life of your kiln, and improve the overall outcome of your work.
Specialization:
- Master of wheel-throwing, hand-building, and advanced glazing techniques
- Focus on creating both functional pottery and decorative art pieces
Recognition:
- Celebrated by collectors and art enthusiasts for creating one-of-a-kind pieces that blend artistry with functionality
- Participates in local and national exhibitions, earning accolades for his innovative designs and craftsmanship
Passion:
- Deeply committed to exploring and pushing the boundaries of ceramic artistry
- Continuously experiments with new materials, firing techniques, and artistic concepts to evolve his craft
Personal Philosophy:
- Believes in the transformative power of art, aiming to evoke emotions and connections through his ceramic creations
- Advocates for sustainability in ceramics, using eco-friendly materials and practices whenever possible