Creating a Raku kiln can be an exciting and rewarding project for pottery enthusiasts who wish to embark on the journey of crafting Raku ceramics. Originating from Japan, Raku pottery is celebrated for its distinctive finishes and unpredictable outcomes, making each piece a unique work of art. Building your own kiln allows for a personalized approach to the Raku firing process, affording you more creative control and flexibility in your artistic endeavors.
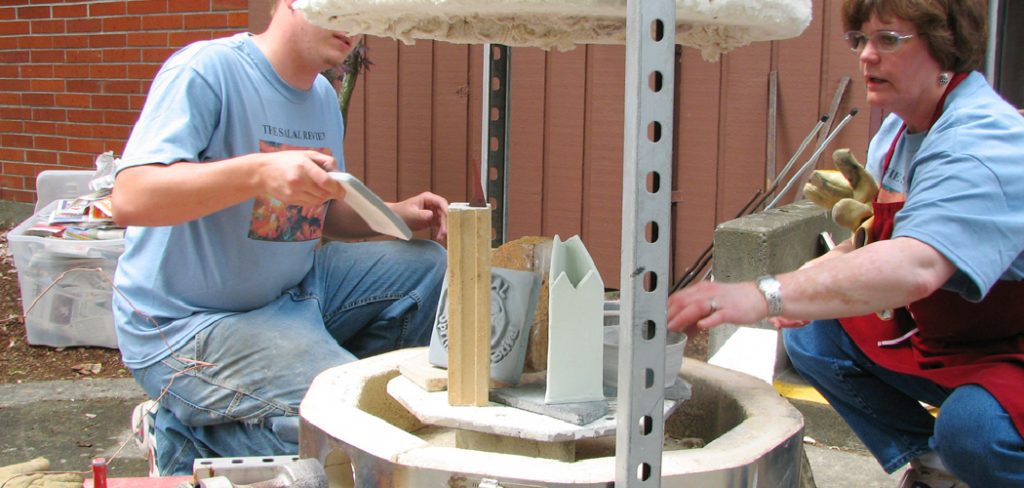
This guide on how to make a raku kiln will walk you through the essential steps and materials needed to construct your very own Raku kiln, facilitating the exploration of this captivating ceramic tradition.
What is a Raku Kiln?
A Raku kiln is a specialized type of kiln used specifically for Raku firing, a pottery technique that involves removing ceramics from the kiln while they are still glowing hot. This is done to produce unique finishes and patterns through rapid cooling and interaction with various elements. Unlike traditional kilns, a Raku kiln is typically designed for quick temperature changes and ease of access, allowing for the rapid firing and cooling processes that are crucial to Raku.
These kilns are often smaller, portable, and can be built from readily available materials such as metal drums, ceramic fiber, and insulating bricks. Their construction is tailored to withstand the high temperatures and thermal shocks associated with the Raku process, enabling potters to experiment with a range of glazes and surface treatments.
Needed Materials
- A Metal Drum or Similar Container (Around 10-15 Gallons)
- Ceramic Fiber Blanket or Insulation Board
- Insulating Fire Bricks
- Propane Burner or Gas Regulator and Hose
- Kiln Shelf or Kiln Posts and Shelves
- Rigidized Refractory Cement
- Welded Wire Mesh
- Welding Equipment (if Using a Metal Drum)
- Pulley and Rope (Optional for Lid Mechanism)
8 Step-by-step Guidelines on How to Make a Raku Kiln
Step 1: Prepare Your Container
The first step in creating your Raku kiln is finding a suitable container. A popular choice among potters is a metal drum, as it can easily be found at hardware stores or repurposed from industrial sites. Ensure that the drum has a tight-fitting lid and is free of any flammable residues or materials.
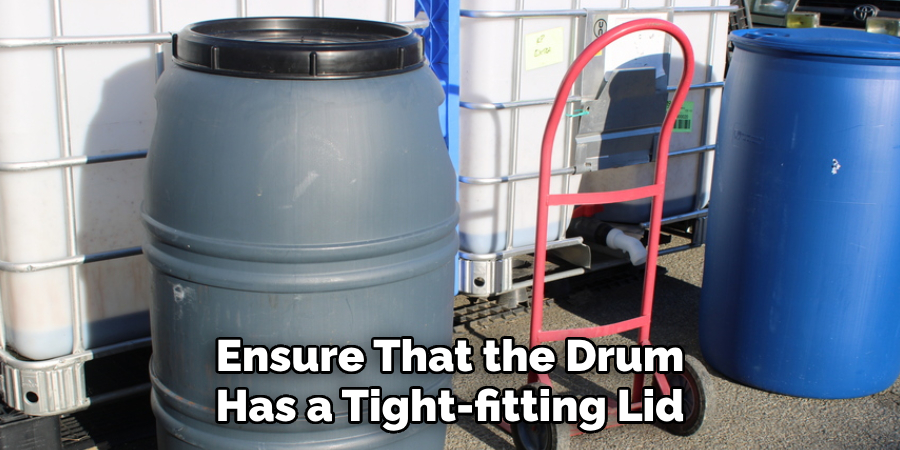
If you opt for a different type of container, such as an old oil tank or steel box, make sure it is made of heat-resistant material and does not have any plastic or rubber parts that could melt.
Step 2: Cut Holes for Ventilation and Propane Burner
Using a drill or jigsaw, carefully cut two holes on opposite sides of the drum; one hole should be around 3-4 inches in diameter for ventilation, and the other should be big enough to fit your propane burner. These holes will allow oxygen to enter the kiln and gas to escape during firing, ensuring a controlled and safe environment.
If you are using a metal drum, make sure to remove any coatings or paint from the inside before cutting.
Step 3: Install Ceramic Fiber Blanket/Insulation Board
Once the ventilation and burner holes are cut, the next step is to line the inside of your kiln container with a ceramic fiber blanket or insulation board. This lining serves as the primary insulator for your kiln, helping to retain heat while protecting the metal container from excessive temperatures. Measure the interior dimensions of your container and cut the insulation to fit snugly within.
Start by covering the sides of the drum, ensuring there is a tight fit with no gaps through which heat could escape. Secure the insulation in place using ceramic buttons or high-temperature adhesive suitable for such materials. For added insulation, you may also choose to cover the base and the lid of the drum, making sure the blanket or board does not obstruct any of the holes previously cut for the burner and ventilation. This layer of insulation is crucial to the effective functioning of your Raku kiln, allowing it to reach and maintain the high temperatures necessary for Raku firing.
Step 4: Create a Base for Your Kiln Shelf
To prevent your kiln shelf from coming into direct contact with the burner, which could lead to damage or warping, create a base using insulating fire bricks. These bricks are specially designed to withstand high temperatures and will act as a barrier between the shelf and burner. Arrange them in a square shape near the bottom of your kiln, making sure there is enough room for air to circulate around and underneath.
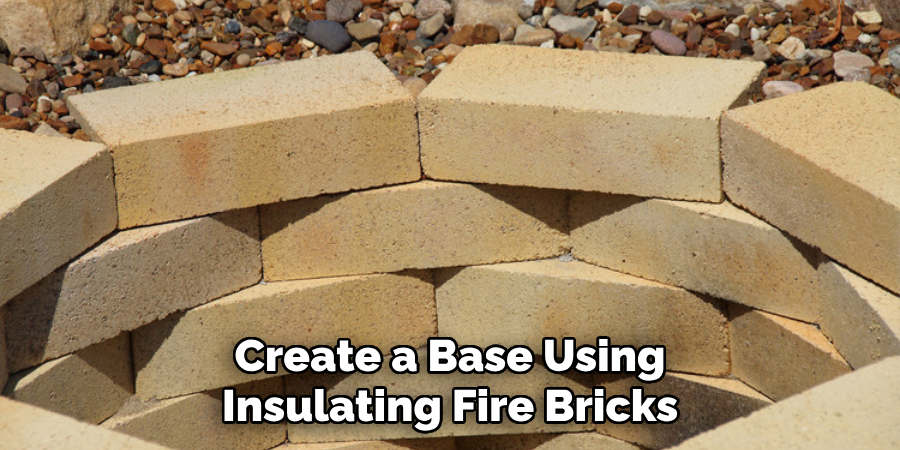
The kiln shelf or posts and shelves should be placed on top of this base, ensuring they are securely supported and do not obstruct the ventilation holes.
Step 5: Construct Lid Mechanism (Optional)
If you wish to have a lid that can be easily removed during firing, construct a mechanism using a pulley and rope attached to both sides of the kiln. This will allow you to lift the lid without having to remove it completely, minimizing heat loss and facilitating quick access for removal of the pieces during firing.
It is also important to create a small opening for the lid that will allow you to monitor the temperature inside the kiln without having to open it fully.
Step 6: Install Welded Wire Mesh
A layer of welded wire mesh should be placed over the kiln shelf or posts and shelves, acting as a support for your ceramics during firing. This mesh will also prevent them from touching the insulating materials and potentially damaging them. Cut the mesh to size and secure it in place using metal clips or wires.
The mesh should be positioned close to the top of your kiln, leaving enough space for air and heat to circulate.
Step 7: Apply Refractory Cement
To protect the metal container from extreme temperatures and thermal shocks, apply a layer of rigidized refractory cement over all exposed surfaces. This will also help seal any gaps or cracks in the insulation and create a more uniform heat distribution within the kiln. Follow the manufacturer’s instructions for mixing and applying the cement properly.
If you are using a metal drum as your kiln container, you may want to consider welding steel reinforcement rods across the lid and base of the drum for added durability.
Step 8: Connect the Propane Burner and Test Kiln
Finally, connect your propane burner to the hole in the side of the kiln using a gas regulator and hose. Make sure all connections are secure before testing the kiln by lighting the burner. Adjust the flame as needed to reach and maintain desired temperatures for Raku firing.
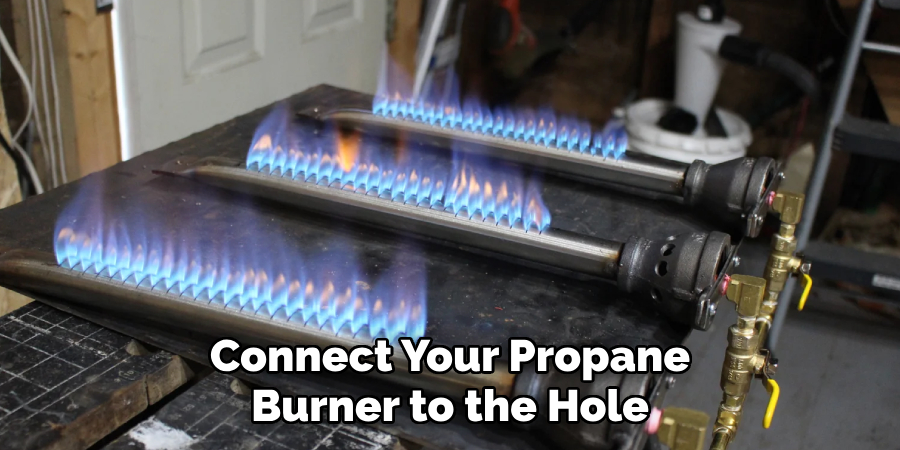
It is important to monitor the temperature inside the kiln throughout the firing process, making adjustments to airflow and flame intensity as necessary.
Following these step-by-step guidelines on how to make a raku kiln, you can easily create your own Raku kiln and enjoy the unique and beautiful results of this traditional Japanese firing technique. Remember to always follow proper safety precautions when working with high temperatures and open flames. Happy firing!
Do You Need to Get Help From an Expert?
Building a Raku kiln can be a rewarding project, but it also requires a clear understanding of the materials and processes involved. If you’re unfamiliar with metalworking, ceramic materials, or working with propane burners, it might be wise to seek assistance from an expert. Experienced potters, metalworkers, or kiln builders can offer valuable insights and guidance, ensuring that your project is successful and safe.
Additionally, consulting with a professional can help you troubleshoot any issues that may arise and provide peace of mind as you embark on this creative endeavor. While DIY projects are fulfilling, expertise from knowledgeable sources ensures a solid foundation for your Raku kiln masterpiece.
Frequently Asked Questions
Q: Can I Build a Raku Kiln Using Other Materials Besides a Metal Drum?
A: Yes, there are various designs and methods for building a Raku kiln using different materials such as brick, clay, or even an old oil drum. However, the steps outlined in this guide specifically pertain to constructing a Raku kiln from a metal drum.
Q: Can I Use Any Type of Insulation for My Kiln?
A: No, it is important to use insulation materials that can withstand high temperatures and are suitable for kiln firing. Commonly used materials include ceramic fiber blankets or boards, refractory bricks, and rigidized refractory cement.
Q: How Hot Does a Raku Kiln Get?
A: A Raku kiln typically reaches temperatures between 1,600-2,000°F (871-1093°C) during firing. These high temperatures are essential for the unique effects achieved through Raku firing.
Q: Is It Safe to Build and Operate a Raku Kiln?
A: While building and operating a Raku kiln involves working with high temperatures and open flames, it can be done safely by following proper precautions. Always wear protective gear such as heat-resistant gloves and eye protection, and make sure to have a fire extinguisher nearby. It is also important to have proper ventilation in your workspace when using propane burners. Consult with local regulations or experts for any specific safety guidelines related to building and firing a Raku kiln in your area.
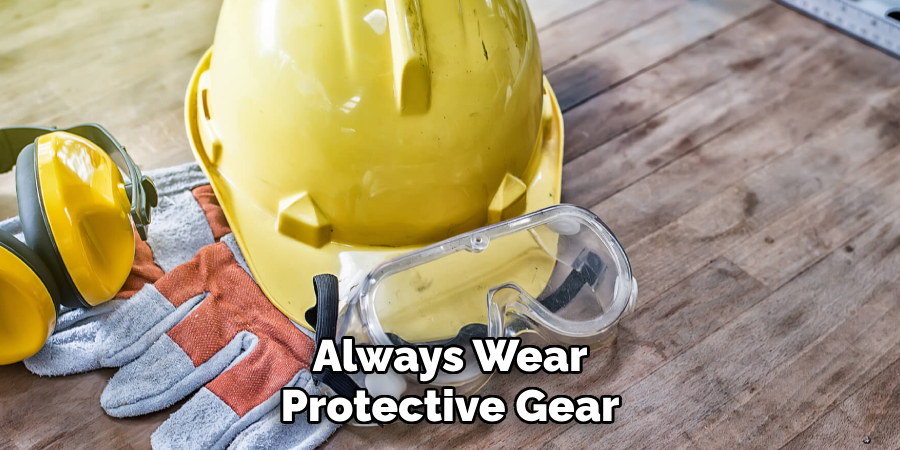
Conclusion
Making your own Raku kiln can be a fun and rewarding project that allows you to have complete control over your ceramics’ firing process. By following these step-by-step guidelines on how to make a raku kiln and using high-quality materials, you can create a durable and efficient Raku kiln that produces stunning results.
Remember to always prioritize safety and follow proper guidelines for firing ceramics to ensure a successful and enjoyable experience. Happy creating!
Specialization:
- Master of wheel-throwing, hand-building, and advanced glazing techniques
- Focus on creating both functional pottery and decorative art pieces
Recognition:
- Celebrated by collectors and art enthusiasts for creating one-of-a-kind pieces that blend artistry with functionality
- Participates in local and national exhibitions, earning accolades for his innovative designs and craftsmanship
Passion:
- Deeply committed to exploring and pushing the boundaries of ceramic artistry
- Continuously experiments with new materials, firing techniques, and artistic concepts to evolve his craft
Personal Philosophy:
- Believes in the transformative power of art, aiming to evoke emotions and connections through his ceramic creations
- Advocates for sustainability in ceramics, using eco-friendly materials and practices whenever possible