Colored ceramic clay offers an incredible opportunity to bring vibrancy and personality to pottery and ceramic art. This versatile medium allows artists to infuse their creations with dynamic hues, enriching both functional ware and sculptural pieces.
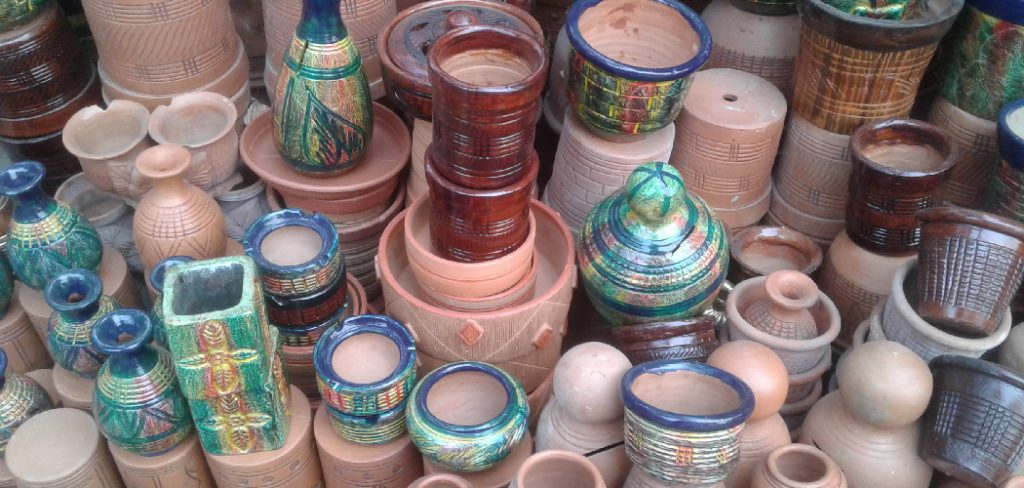
Whether you are crafting intricate tiles or everyday dinnerware, colored clay can transform ordinary objects into eye-catching works of art. The two main methods for adding color to ceramic clay are mixing pigments directly into the clay body or applying surface decorations like slips, stains, or underglazes. Each technique provides unique visual effects and requires careful attention to detail for optimal results.
Properly understanding how to color ceramic clay ensures the colors remain rich and durable through the firing process. By mastering these methods, artists can unlock limitless creative possibilities and produce captivating pieces through their texture, design, and vivid aesthetic appeal.
Understanding Types of Ceramic Clay
Earthenware
.Earthenware is a porous and highly workable ceramic clay, making it a popular choice for beginners and artists seeking vibrant, bold colors. Due to its lower firing temperature, earthenware pairs well with bright glazes and underglazes that maintain their vibrancy without the risk of color dulling. However, its porous nature requires a clear glaze to seal the surface, ensuring durability and preventing water absorption.
Stoneware
Stoneware is dense and incredibly durable, requiring higher firing temperatures to vitrify. Its strength allows for both functional and decorative pieces that stand the test of time. The natural hues of stoneware, typically dark brown to gray, can affect how certain colors appear post-firing.
Artists often use opaque glazes or darker tones to complement the natural shades of the material, emphasizing earthy and muted aesthetics.
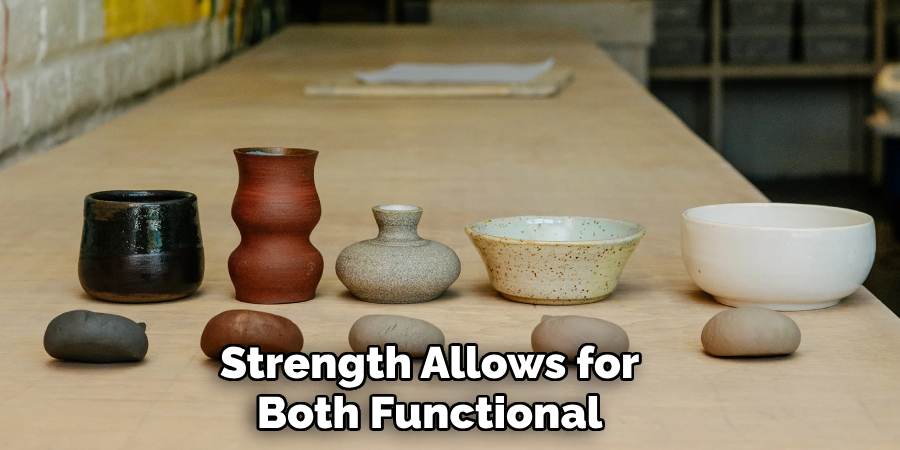
Porcelain
Porcelain is known for its fine texture and translucent quality, offering an elegant base for soft, subtle color applications. Its light, almost white surface allows delicate glazes, washes, or stains to stand out with exceptional clarity.
Due to its smooth and sensitive nature, working with porcelain demands precision, as surface details and colors are more pronounced than other clays. Artists often choose pastel tones or minimalist designs to highlight their refined characteristics.
Each clay type significantly influences an artist’s color choices and techniques, consistently considering the surface texture, firing temperature, and desired aesthetic results shaping the creative process.
Choosing the Right Coloring Agents
Oxides and Stains
Coloring agents like oxides and stains are crucial in crafting unique and vibrant ceramic works. Oxides, such as iron oxide, cobalt oxide, and chrome oxide, are commonly used to produce rich, earthy reds, deep blues, and natural greens, respectively.
Pre-made ceramic stains are an excellent option for more consistent and vibrant results. These stains are formulated to provide reliable colors across different firing conditions, making them a favorite among ceramicists seeking precision.
Underglazes and Engobes
Underglazes and engobes are useful for surface decoration before the glazing stage. Underglazes allow for detailed painting and vivid colors that remain visible under transparent glaze layers.
Engobes, which are liquid clay slips mixed with coloring agents, can be applied to create smooth, even finishes or textured designs depending on the desired effect. Both underglazes and engobes offer versatility and expand the range of artistic expression on ceramic surfaces.
Natural Additives
For those who love to experiment, natural additives like ash, sand, or even plant materials can yield fascinating and unpredictable results. Testing is essential when working with any coloring agent, as factors like firing temperature and glaze application can alter the final outcome. Small test tiles ensure the intended effect is achieved without surprises.
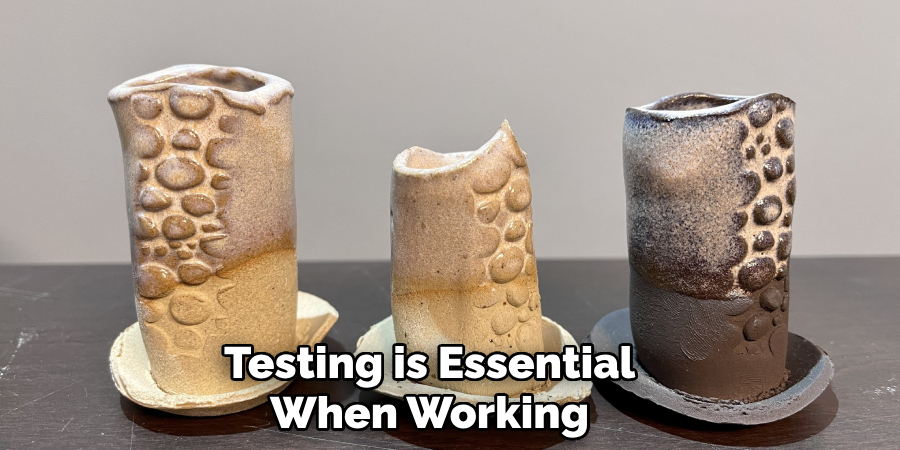
How to Color Ceramic Clay: Methods for Coloring Ceramic Clay
Coloring ceramic clay opens up endless possibilities for artistic expression, allowing creators to experiment with various techniques to achieve unique and vibrant results. Below are several approaches to incorporating color into ceramic work.
Mixing Color into the Clay Body
One of the most direct methods for coloring clay is mixing oxides or stains into the clay body itself. This involves thoroughly kneading the chosen coloring agent into the clay to achieve a uniform color. Care must be taken to ensure even distribution, as insufficient mixing may result in streaks or inconsistencies.
This approach allows the color to permeate the entire clay body, making it ideal for sculptural work or pieces where the surface is carved or altered.
Layering Colors
For striking marbled or striated effects, layering contrasting colors is an excellent technique. This involves stacking thin layers of differently colored clays and then manipulating the layers through techniques such as cutting, folding, or twisting.
The layered clay can then be reassembled, revealing intricate patterns within the material. Artists can experiment with various combinations of colors and patterns to achieve stunning visual results that enhance the texture and interest of their pieces.
Surface Decoration
Surface decoration offers another effective method for adding color. Leather-hard clay provides the perfect stage for applying slip or underglaze to paint designs or patterns. These materials sit atop the surface, allowing for vivid, detailed decoration that remains prominent after glazing.
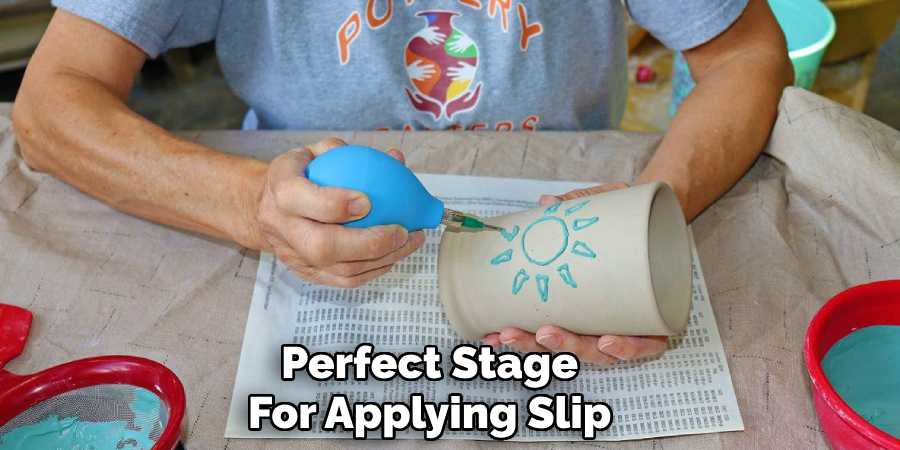
Additionally, carving or etching into the surface can reveal underlying layers of color for a dynamic, multi-dimensional effect. These techniques allow for an impressive level of control and creativity, ensuring a finished piece that is both unique and visually captivating.
Through these varied methods, ceramicists can create works that showcase their artistic vision while leveraging the interplay of color and texture.
Firing Techniques for Colored Clay
Firing is critical in working with colored clay, as it solidifies the form and brings colors to life. Proper techniques ensure the clay retains its vibrancy while achieving the desired finish.
Bisque Firing
Bisque firing is the first step in the process and involves firing the colored clay at low temperatures, typically around 1,800°F (982°C). This initial firing sets the shape and is the foundation for subsequent glazing and decoration. Ensuring the clay is completely dry before bisque firing is essential to prevent cracking or explosions in the kiln.
Glaze Firing
Once the clay has been bisque-fired, a glaze firing can enhance the colors. Transparent or complementary glazes work especially well with colored clay, highlighting the natural hues and layering effects. Before applying glazes to the final piece, testing them on small samples of the same clay body is recommended.
Testing ensures compatibility and helps avoid unexpected color changes during the firing process. Glaze firings are typically carried out at higher temperatures, depending on the type of clay and glaze used.
Oxidation vs. Reduction Firing
The firing atmosphere plays a significant role in the final appearance of colored clay. Oxidation firing, often achieved in an electric kiln, results in consistent, bright colors as oxygen is freely available throughout the process.
On the other hand, reduction firing, commonly done in gas or wood kilns, creates a unique and unpredictable effect by limiting oxygen, which can alter the clay and glaze colors in fascinating ways. Both methods offer opportunities for experimentation and varied artistic expressions.
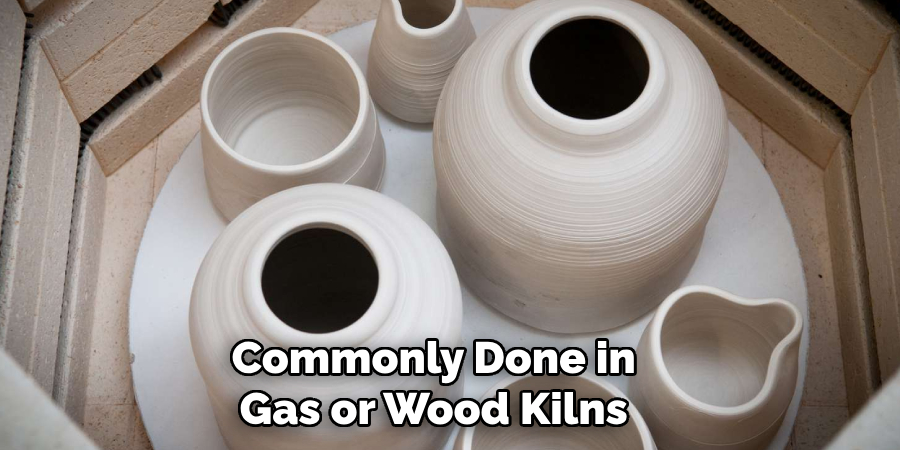
Safety Considerations
Handling kilns and firing materials requires strict adherence to safety protocols. Always ensure proper ventilation in the kiln area and use protective gear, such as heat-resistant gloves and eye protection, when operating kilns. Understanding the firing process not only enhances the final outcome but also ensures a safe and enjoyable ceramics experience.
Tips for Vibrant and Durable Colors
Achieving vibrant and durable colors in ceramics requires careful attention to detail and technique. Here are some essential tips to help you enhance your work:
Proper Proportions
Using the right proportions is crucial when incorporating stains or oxides into your clay or glazes. Aim for 5-10% stain or oxide in your mixture for optimal results. Correct measurements ensure consistency and prevent over-saturation, which can lead to defects or muted tones.
Test Tiles
Before committing to a full project, test your color mixtures on small test tiles. This step lets you preview how the colors will look after firing and help avoid unexpected results. Testing is particularly important when experimenting with new combinations or materials.
Layering Techniques
Adding multiple layers of slip or underglaze can create depth and rich hues in your designs. Allow each layer to dry partially before applying the next for better adhesion and a more vibrant final appearance.
Avoiding Fading
Proper firing and sealing are essential to preserving the brightness of your ceramics over time. Ensure the firing temperature matches the requirements of your clay and glaze to prevent dullness. Additionally, applying a clear sealant can protect colors from wear and fading, maintaining their brilliance.
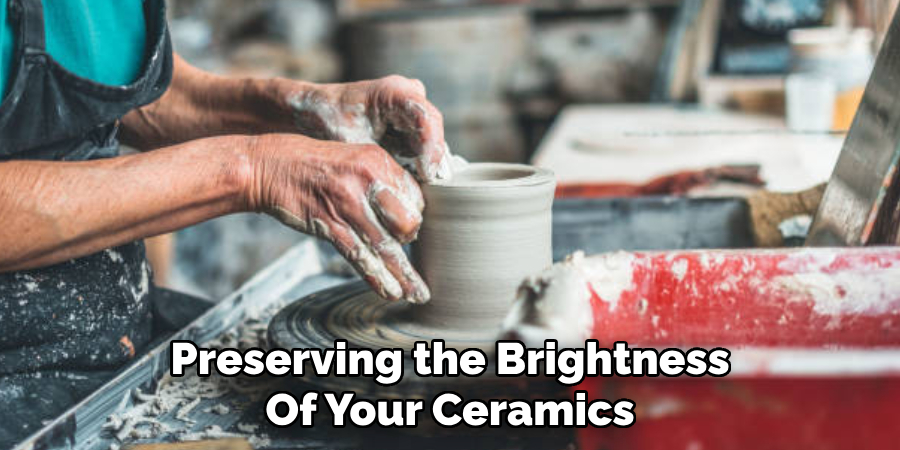
Creative Projects with Colored Clay
Colored clay opens up a world of creative possibilities for ceramic artists. Here are some project ideas to inspire your next masterpiece:
Marbled Bowls and Vases
Combine multiple colors of clay to create stunning marbled patterns. The process begins by layering and twisting different colored clays, then shaping them into bowls or vases. Each piece is entirely unique, as the patterns emerge through the movement of the clay during the forming process.
Carved Tiles
Use contrasting layers of colored slip or clay to craft decorative wall tiles. Begin by layering slabs of colored clay, then carve through the layers to expose the underlying hues. This technique produces intricate patterns and textures, perfect for adding an artistic touch to any space.
Functional Ware
Create colorful plates, mugs, and serving dishes that are practical and beautiful. Use vibrant slips, underglazes, or marbled clay to craft one-of-a-kind everyday items. These projects add a pop of color to daily routines and make for thoughtful handmade gifts.
Sculptural Art
Colored clay is an excellent medium for enhancing sculptural works. Bold tones emphasize dramatic contours, while subtle hues reveal delicate textures. Experiment with layering or inlay techniques to elevate your design. The result is a harmonious blend of color and form that captivates any observer.
Troubleshooting Common Issues
Uneven Coloring
Uneven coloring is a frequent challenge when working with colored clay. Ensure the colorant is thoroughly kneaded into the clay body to avoid this. Uneven mixing may result in streaks or patches. Take time to wedge the clay properly, distributing color consistently throughout.
Color Fading After Firing
If colors appear dull or faded after firing, the cause could be an inappropriate firing temperature or incompatible stains or oxides. Always verify that the stains or oxides you use suit your kiln’s firing range. Testing on a small sample before applying it to a final piece can help gauge results accurately.
Surface Cracks or Bubbles
Surface issues like cracks or bubbles often stem from improper application of slip or underglaze. For best results, apply a thin and even layer, as over-thinning the mixture can compromise the surface quality. Allow layers to dry adequately before additional applications or firing.
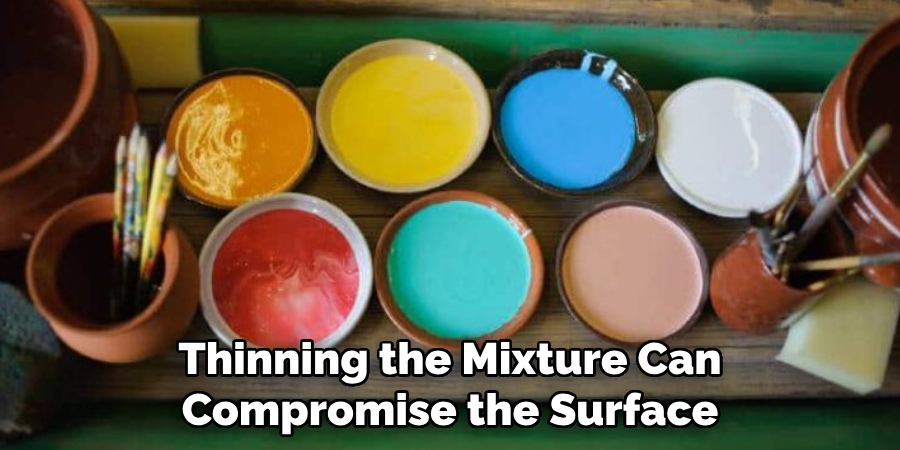
Conclusion
When learning how to color ceramic clay, two primary methods stand out: mixing colorants directly into the clay body and using surface decoration techniques like slips, underglazes, or stains. Both approaches require careful attention to detail, proper technique, and experimentation to achieve the desired results.
Thorough testing is essential to ensure compatibility with firing temperatures and to avoid potential issues such as uneven coloring or surface defects. By exploring these methods, artists can unlock endless creative possibilities and add vibrant touches to their ceramic creations. Step out of your comfort zone and test new ideas to enhance your projects.
Specialization:
- Master of wheel-throwing, hand-building, and advanced glazing techniques
- Focus on creating both functional pottery and decorative art pieces
Recognition:
- Celebrated by collectors and art enthusiasts for creating one-of-a-kind pieces that blend artistry with functionality
- Participates in local and national exhibitions, earning accolades for his innovative designs and craftsmanship
Passion:
- Deeply committed to exploring and pushing the boundaries of ceramic artistry
- Continuously experiments with new materials, firing techniques, and artistic concepts to evolve his craft
Personal Philosophy:
- Believes in the transformative power of art, aiming to evoke emotions and connections through his ceramic creations
- Advocates for sustainability in ceramics, using eco-friendly materials and practices whenever possible