Drilling into ceramic can be a daunting task for both amateurs and professionals alike, but with the right tools and techniques, it becomes much more manageable. Ceramic materials are renowned for their durability and aesthetic appeal, often used in tiles, pots, and various household items.
However, their hard and brittle nature requires careful handling to avoid cracking or breaking during the drilling process. This guide aims to provide you with a step-by-step approach for how to drill into ceramic, ensuring a smooth and efficient process that preserves the integrity and appearance of your ceramic pieces.
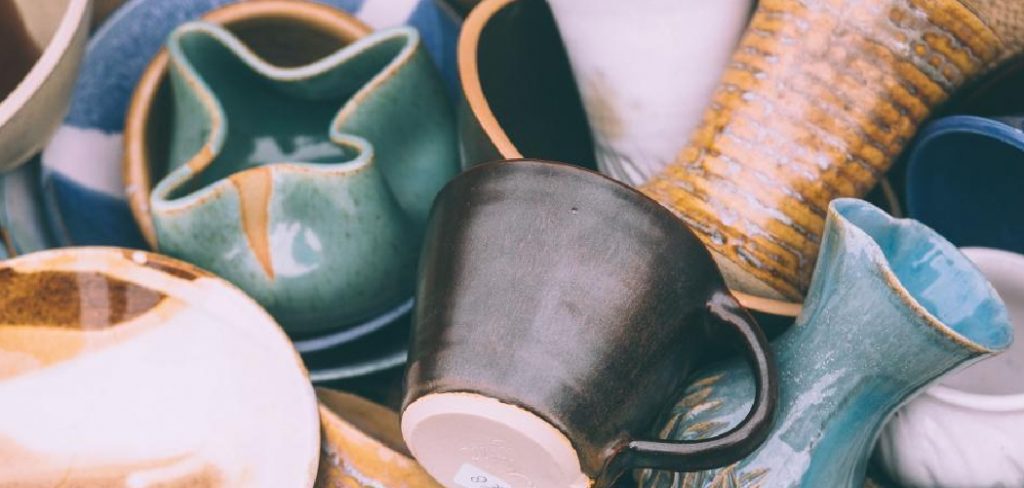
Why You Might Need to Drill into Ceramic
Drilling into ceramic is often necessary for various home improvement and creative projects. One common reason is during the installation of fixtures and fittings on tiled surfaces, such as hanging towel racks, showerheads, or shelving units, which require securing screws into the wall. Additionally, creating drainage holes in ceramic pots is essential for plant health, allowing excess water to escape and preventing root rot. Craft enthusiasts might also find themselves drilling into ceramic to customize or personalize decorative pieces, enhancing their aesthetic value. In each case, careful drilling ensures the project’s success while maintaining the ceramic’s structural integrity.
Materials Needed
To successfully drill into ceramic, you’ll need to gather a few essential materials and tools to ensure the job is done effectively and safely:
- Ceramic Drill Bit: Specifically designed to cut through hard surfaces like ceramic, these bits are typically made from carbide or diamond-tipped for increased durability.
- Drill: A variable-speed electric drill is ideal, as it allows you to start slowly to help prevent cracking.
- Masking Tape: Applying this on the surface where you’ll be drilling helps to prevent the drill from slipping and to mark the location.
- Safety Goggles: Essential to protect your eyes from ceramic dust and any debris produced during drilling.
- Dust Mask: To safeguard against inhaling harmful ceramic dust particles.
- Spray Bottle with Water: Helps to keep the drill bit cool and minimizes dust buildup.
- Marker or Pencil: For marking the exact drilling spot on the ceramic.
- Clamp: If drilling into a loose ceramic piece, a clamp can stabilize the item to prevent movement.
Having these materials on hand will prepare you to drill into ceramic effectively, minimizing the risk of damage and ensuring a clean result.
Choose the Right Drill Bit
Selecting the appropriate drill bit is crucial for a successful ceramic drilling project. Not all drill bits are created equal, and using the wrong type can lead to cracked ceramics or inefficient drilling. For ceramic materials, opt for either a carbide-tipped or diamond-tipped drill bit. Carbide-tipped bits are durable and sufficient for many ceramic projects, providing a balance of cost and performance. However, if you’re working with particularly hard or thick ceramic, a diamond-tipped drill bit is recommended, as it offers superior cutting capabilities and longevity.
Regardless of the type you choose, ensure the bit is intended for use with ceramics to avoid mishaps and achieve the best results. Additionally, always check that your drill bit is in good condition without any signs of wear or damage, as a sharp, intact bit will significantly enhance drilling performance.
10 Effective Methods for Drilling into Ceramic
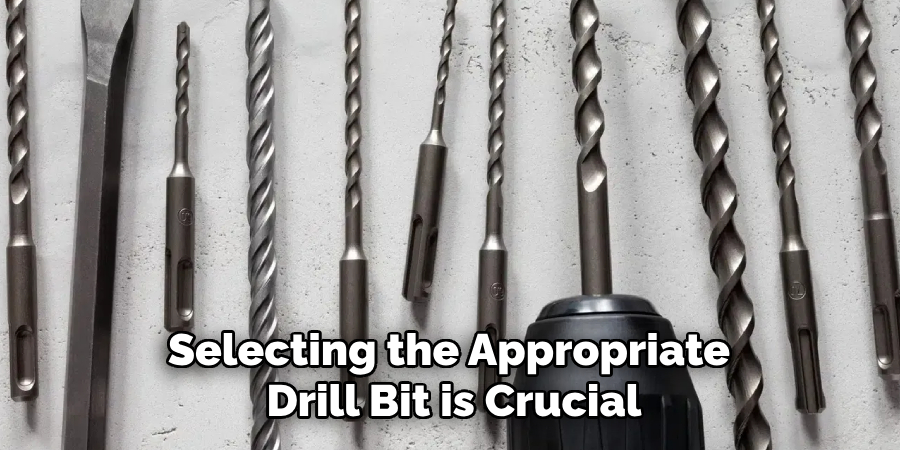
Are you ready to tackle a ceramic project but unsure how to drill without cracking or damaging your material? Whether you’re planning a home improvement task or a craft project, drilling into ceramic requires the right technique and tools. In this listicle, you’ll discover ten effective methods that will empower you to drill into ceramic like a pro, ensuring a smooth and successful outcome.
1. Choose the Right Drill Bit
Selecting the correct drill bit is crucial for achieving a clean hole in ceramic. Carbide-tipped masonry drill bits are ideal as they are specifically designed to penetrate hard surfaces like tiles. Avoid using regular wood or metal bits since they can easily break or cause chipping on ceramic surfaces.
2. Use Painter’s Tape
To prevent the drill bit from slipping on the smooth ceramic surface, apply a piece of painter’s tape over the spot you intend to drill. This will provide extra grip for the drill bit and help avoid scratches. Mark your drilling spot directly on the tape for precision.
3. Start with a Small Pilot Hole
Initiating the process with a small pilot hole helps guide the larger drill bit into place and minimizes the risk of cracking. Use a small drill bit to create this initial hole before proceeding with your final size.
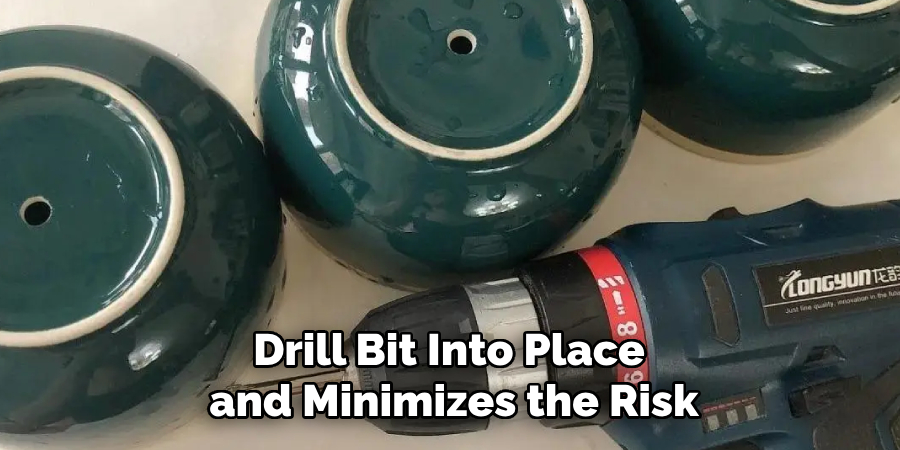
4. Apply Moderate Pressure
Exerting too much pressure can cause the ceramic to crack. Instead, apply moderate, steady pressure as you drill. Allow the drill bit to do the work, and be patient as it gradually penetrates the ceramic.
5. Maintain a Low Speed
Drilling at a low speed reduces heat buildup, which can weaken ceramic and cause cracks. Set your drill to the lowest speed setting and gradually increase if necessary. This approach ensures better control and minimizes the risk of damaging the material.
6. Keep the Drill Perpendicular
Hold the drill at a perfect right angle to the surface to ensure a straight, even hole. Drilling at an angle increases the chances of skidding and uneven edges. Use a drill guide or level if needed to maintain alignment.
7. Cool the Drill Bit
Ceramic can overheat quickly when drilled. To prevent this, periodically cool the drill bit with water. You can use a damp sponge or a spray bottle to moisten the drilling area, which helps dissipate heat and prolongs the life of your drill bit.
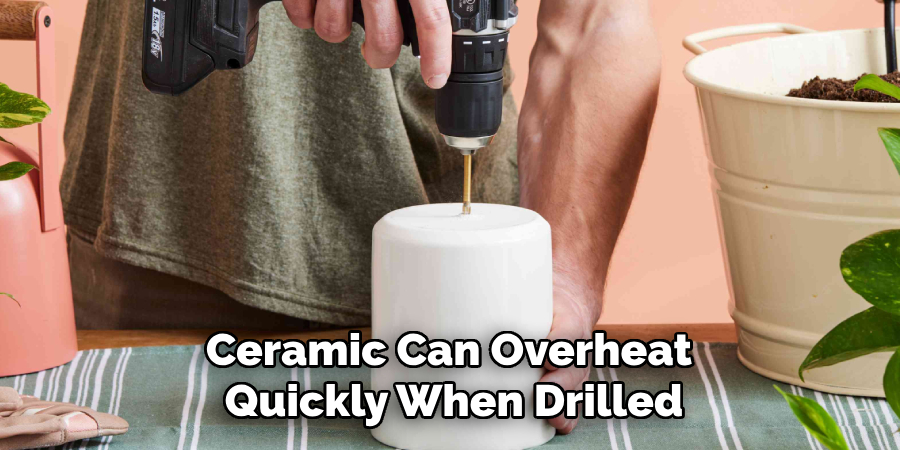
8. Work in Short Bursts
Drilling continuously can generate excessive heat and stress on the ceramic. Instead, drill in short intervals, taking breaks between sessions. This technique reduces the risk of overheating and allows you to remove any debris accumulated in the hole.
9. Use a Backing Material
Placing a piece of wood or similar backing material behind the ceramic piece provides support and prevents cracking as the drill bit exits the other side. This backing absorbs the drill’s impact, ensuring a clean exit point.
10. Clean the Hole
Once your hole is drilled, clean it thoroughly to remove dust and debris. A simple wipe with a damp cloth or brush ensures your ceramic surface remains pristine and ready for further work or installation.
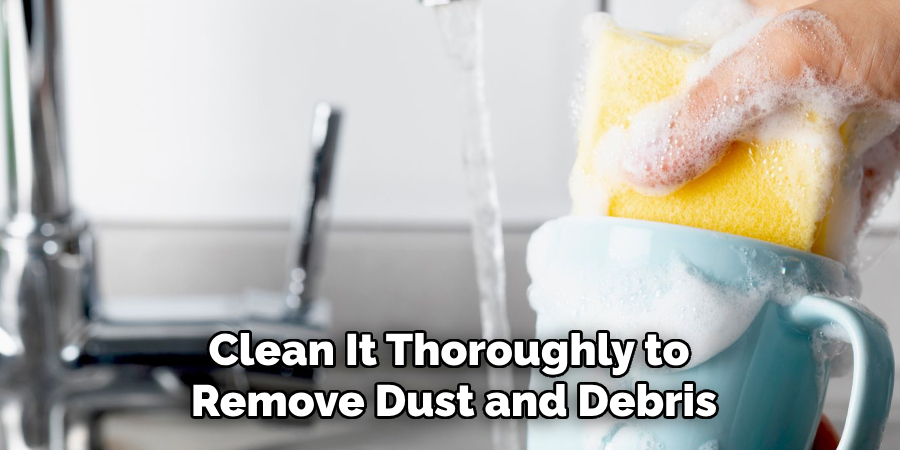
Maintenance and Upkeep
Proper maintenance and upkeep are critical to ensuring the longevity and safety of your ceramic drilling tools and surfaces. After completing your drilling project, clean the drill bits thoroughly with a soft cloth to remove any ceramic dust and debris, which can cause wear and reduce performance. Regular inspection of the drill bits for signs of dullness or damage is essential; sharpen or replace them as necessary to maintain efficient cutting abilities.
Additionally, store your tools in a dry, secure location to prevent rust and other environmental damage. When dealing with ceramic surfaces, periodically check for any signs of cracks or chips around drilled areas. If identified, address them promptly to prevent further damage. Proper care and maintenance not only extend the life of your tools and materials but also guarantee the success of future projects.
Things to Consider When Choosing a Drill for Ceramic Projects
When embarking on a ceramic drilling project, selecting the right drill is as important as choosing the proper drill bit. There are several factors to keep in mind to ensure efficiency and safety:
- Drill Type: Opt for a corded drill if you’re dealing with extensive or repetitive drilling tasks, as they offer consistent power and are generally more durable. For smaller projects or hard-to-reach areas, a cordless drill may be more convenient due to its flexibility and portability.
- Power Output: Ensure the drill provides sufficient power to handle dense ceramic materials. A drill with variable speed settings is ideal, as it allows you to adjust the speed to prevent overheating and cracking.
- Ergonomics: Choose a drill with a comfortable grip and weight that suits your handling preference, minimizing fatigue during extended use. Additionally, a drill with a side handle can provide extra stability, especially when operating at low speeds.
- Speed Control: Look for drills with settings that allow for precise control over drilling speed. This will help maintain accuracy and reduce the risk of damage to the ceramic surface.
- User-Friendly Features: Consider features like a built-in level to maintain the correct angle and a clutch setting for controlling torque. These can significantly ease the drilling process and improve outcomes.
By carefully evaluating these factors, you can select a drill that complements your project needs and enhances your ability to create clean, precise ceramic holes.
Conclusion
Drilling into ceramic surfaces can seem daunting, but with the right tools and techniques, it becomes a manageable and rewarding task. By utilizing specialized ceramic drill bits and adopting strategies such as using painter’s tape, starting with a pilot hole, and maintaining moderate pressure, you can achieve clean, precise results without damaging the material. Thanks for reading, and we hope this has given you some inspiration on how to drill into ceramic!
Specialization:
- Master of wheel-throwing, hand-building, and advanced glazing techniques
- Focus on creating both functional pottery and decorative art pieces
Recognition:
- Celebrated by collectors and art enthusiasts for creating one-of-a-kind pieces that blend artistry with functionality
- Participates in local and national exhibitions, earning accolades for his innovative designs and craftsmanship
Passion:
- Deeply committed to exploring and pushing the boundaries of ceramic artistry
- Continuously experiments with new materials, firing techniques, and artistic concepts to evolve his craft
Personal Philosophy:
- Believes in the transformative power of art, aiming to evoke emotions and connections through his ceramic creations
- Advocates for sustainability in ceramics, using eco-friendly materials and practices whenever possible