Gabardine is traditionally known as a tightly woven fabric characterized by its distinctive diagonal pattern, offering both durability and a sleek appearance. This textile has been a popular choice for suits, coats, and trousers for its strength and smooth finish. Translating gabardine’s unique texture into ceramics draws inspiration from this iconic fabric, aiming to infuse pottery with its classic woven aesthetics.
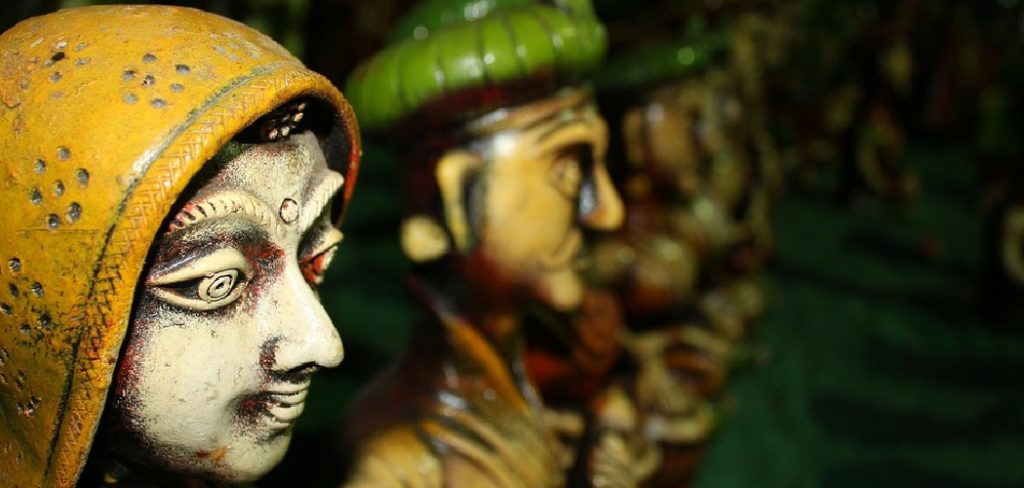
This intriguing fusion of fabric and clay challenges artisans to replicate gabardine’s tactile and visual appeal through ceramics. The purpose of this article is to provide “how to make a ceramic gabardine” as a comprehensive step-by-step guide, assisting crafters in creating ceramic pieces that artfully mimic the textured elegance of gabardine. By blending the timeless appeal of fabric patterns with the enduring quality of ceramics, artisans can explore innovative possibilities in their creative ventures.
Materials and Tools Needed
Creating a ceramic piece that mimics the classic gabardine texture requires specific materials and tools to achieve the desired outcome.
Clay Options
For texture work, selecting the right type of clay is crucial. Earthenware and stoneware are both excellent choices due to their workability and versatility. Earthenware is known for its smooth texture and pale color, making it suitable for applying intricate patterns. Stoneware, on the other hand, offers greater durability and a richer, earth-toned finish. When choosing your clay, consider its plasticity, which refers to how easily it can be shaped and molded without breaking. Clays with higher plasticity are preferred for texture work as they can hold detailed impressions and subtle patterns replicating the gabardine weave.
Tools and Accessories
Certain tools are essential for crafting the distinctive pattern of gabardine in ceramics. Sculpting tools such as needle tools and loop tools allow for precise and controlled carving, while textured rollers and custom stamps can imprint the diagonal lines characteristic of gabardine. Additionally, optional items like texture mats featuring gabardine-like patterns can enhance the detail of your work. Brushes and sponges are useful for smoothing and refining surfaces, ensuring a polished finish that captures the elegance of the original fabric design.
Preparing the Clay for Texturing
Conditioning the Clay
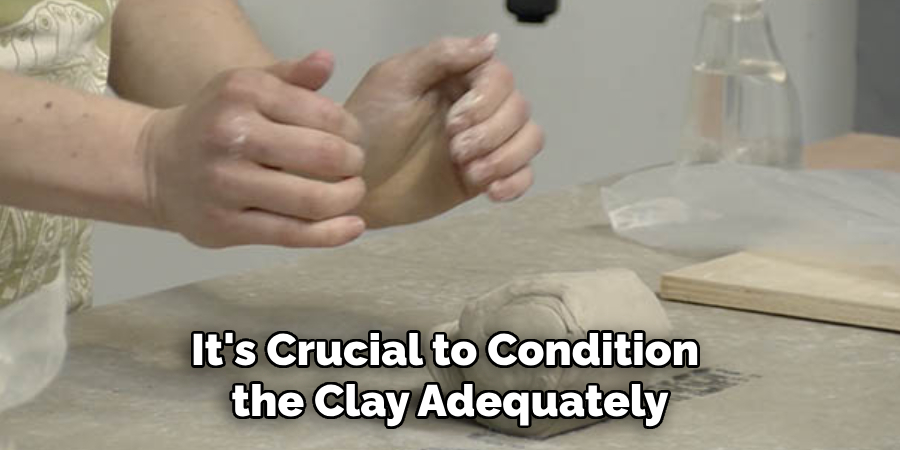
Before you begin texturing, it’s crucial to condition the clay adequately. Start by wedging the clay, a process similar to kneading dough, to remove any air bubbles trapped within. This step ensures uniform consistency and prevents cracking during firing. Effective wedging involves pressing and folding the clay repeatedly until it feels smooth and pliable. Achieving the right consistency is essential for texturing, as it allows the clay to hold intricate patterns and details that emulate the gabardine weave without losing structural integrity.
Shaping the Base Form
Once conditioned, roll out a slab of clay or mold it into a basic vessel shape, depending on your project goals. To create a slab, use a rolling pin and guides to achieve an even thickness. Gently coil or pinch the clay into your desired form for vessel shapes. Maintaining a smooth, even surface is important as this provides the perfect canvas for the gabardine texture, ensuring your final piece captures the elegance and detail reflective of the iconic fabric.
How to Make a Ceramic Gabardine: Creating the Gabardine Texture
Using Texture Mats or Rollers
Using texture mats or rollers is an efficient way to imprint the gabardine pattern onto your ceramic piece. Begin by selecting a pre-made gabardine-like texture mat that features the characteristic diagonal weave of the fabric. Position the mat or roller onto the conditioned clay surface, ensuring alignment to maintain the continuity of the pattern. Press or roll the tool across the clay, applying consistent pressure as you move along the entire surface. Maintaining a steady hand is crucial to prevent distorting the design. Check the impression regularly to ensure an even and deep imprint is achieved. Reapply the texture mat or roller if any areas lack definition, blending the edges seamlessly to preserve the pattern’s intricacy.
Hand-Creating the Gabardine Effect
You can hand-carve the gabardine pattern into your ceramic piece for a more personalized touch. Start by sketching light guidelines across the clay surface to outline the diagonal pattern typical of gabardine. Using tools such as needles or small loop tools, carve along these lines, maintaining uniform depth and spacing to replicate the fabric’s weave accurately. When carving, hold the tool at a slight angle to create clean and defined lines. To add realism, slightly vary the line widths and depths to mimic the subtly varied texture of woven fabric. Regularly evaluate your work to ensure the lines intersect correctly and remain consistent throughout, adjusting your technique to achieve a lifelike texture that resembles the classic gabardine.
Combining Techniques for a Unique Look
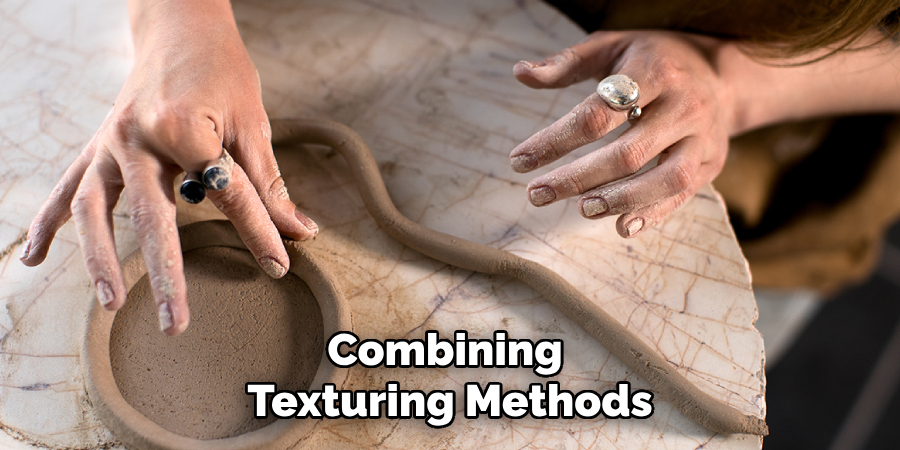
Combining texturing methods can enhance the visual interest of your ceramic gabardine and personalize its appearance. Start by layering textures, applying a stamped or rolled baseline pattern before hand-carving additional details over it. This approach allows you to build depth and complexity, blending the precision of stamps or rollers with the nuanced touch of hand carving. Experiment with different tools and techniques to introduce subtle variations within your pattern, such as altering the direction of diagonal lines or varying line thickness.
Test small sections before committing to your entire piece to ensure the effect meets your artistic vision. Explore the creative possibilities by integrating multiple textures, allowing the fusion of structured patterns and organic carvings to produce a dynamic and original ceramic gabardine piece.
How to Make a Ceramic Gabardine: Shaping and Refining the Piece
Trimming and Smoothing Edges
Once the gabardine texture is imprinted or carved, it’s essential to trim and smooth the edges of your ceramic piece to enhance its overall form. Begin by using a sharp trimming tool to carefully remove any excess clay around the edges, not disturbing the texture. Hold the tool at a slight angle and apply gentle pressure to achieve clean, precise cuts. For areas without texture, like smooth borders or flat surfaces, use a damp sponge or soft brush to gently refine the surface, subtly contrasting the textured sections. This softening technique ensures a polished finish while maintaining the integrity of your crafted intricate gabardine pattern.
Adding Structural Details
Incorporating structural elements like handles, rims, or additional decorative features can enhance your ceramic piece’s functionality and aesthetic appeal. Add handles and fashion clay coils that complement the design, ensuring they are proportional to the overall work. Score both the attachment points on the main body and the ends of the handle, applying slip to create a firm bond. Similarly, when adding rims or decorative borders, ensure these elements blend into the textured surface by smoothing the junction points with tools or fingers. Pay close attention to transitions, aiming for a seamless appearance that integrates these features into the gabardine motif naturally and harmoniously.
Drying and Firing the Ceramic Gabardine
Proper Drying Techniques
Allowing the textured ceramic gabardine piece to dry slowly and evenly is crucial to prevent cracks. Place the piece in a well-ventilated area with a stable temperature to ensure uniform drying. Consider covering the design loosely with plastic wrap for complex or large pieces. This slows down the drying process, reducing the risk of cracking due to rapid moisture loss. Maintain a careful balance between airflow and humidity, periodically checking the piece’s progress. This method helps retain the intricate gabardine textures, ensuring they remain sharp and well-defined until firing.
Bisque Firing
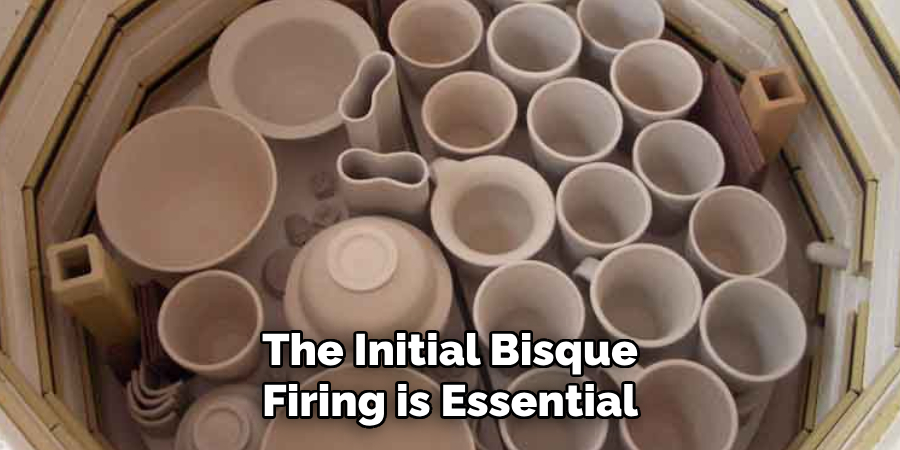
The initial bisque firing is essential to harden your ceramic piece without glazing. Start by placing the thoroughly dried piece in a kiln, ensuring it is dry to the touch and free of cold spots. Depending on the clay type, adjust the kiln temperature accordingly—typically between 1832°F (1000°C) and 1940°F (1060°C) for earthenware and slightly higher for stoneware. Gradually increase the temperature to prevent thermal shock and allow the clay to mature properly. This stage firmly sets the gabardine details in the clay, preparing it for glazing or further firing stages.
Glazing and Finishing
Choosing the Right Glaze
Selecting an appropriate glaze is crucial to showcase the gabardine texture’s depth and intricacy. Opt for translucent glazes that allow the underlying pattern to shine through, enhancing its visual complexity. Matte finishes are also excellent choices, as they add a refined, subtle touch that accentuates the fabric-like relief without overwhelming it. Test different glazes on sample textures before committing to a glaze for your final piece. This testing phase lets you observe how each glaze interacts with the gabardine pattern, providing insight into color differentiation and texture enhancement, ensuring your final selection aligns with your artistic vision.
Applying Glaze and Final Firing
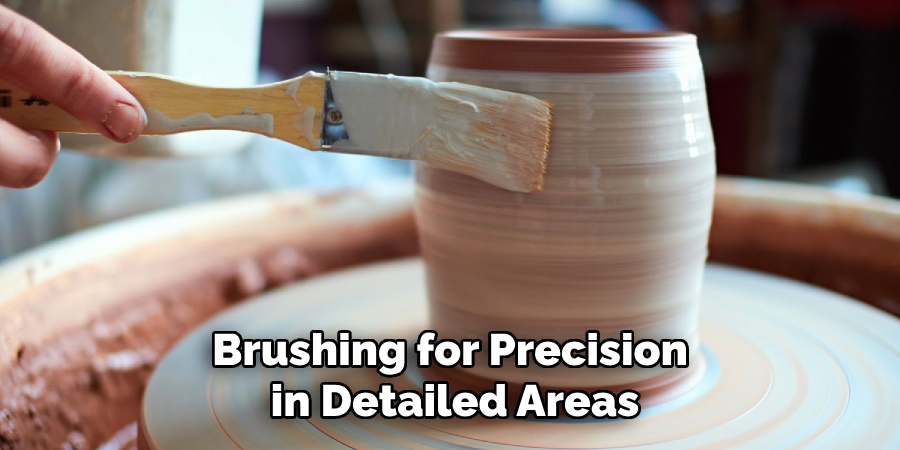
When applying glaze, consider methods like brushing for precision in detailed areas, dipping for even coverage, or spraying to achieve soft, blended transitions. Ensure the entire surface is evenly coated without overloading, which can obscure the texture. Once glazed, place the piece in the kiln for the final firing. Gradually raise the kiln temperature, following the glaze manufacturer’s recommendations to prevent defects. Aim for a firing cycle that ensures a durable finish that is capable of withstanding use while maintaining the polished appearance of the gabardine texture. This final stage solidifies the piece, finishing it with a strong and visually appealing surface.
Conclusion
Creating a ceramic gabardine involves a meticulous process, from imprinting and carving textures to trimming, drying, bisque firing, and applying the perfect glaze. Learning how to make a ceramic gabardine opens the door to experimentation with various tools and techniques that personalize your work. Each step offers opportunities to infuse your unique style and creativity, creating truly captivating pieces. The combination of fabric-inspired textures and ceramics creates a compelling aesthetic, highlighting the beauty of intricate details and the tactile appeal of the medium. Embrace creativity and craft your ceramic masterpiece with gabardine flair.
Specialization:
- Master of wheel-throwing, hand-building, and advanced glazing techniques
- Focus on creating both functional pottery and decorative art pieces
Recognition:
- Celebrated by collectors and art enthusiasts for creating one-of-a-kind pieces that blend artistry with functionality
- Participates in local and national exhibitions, earning accolades for his innovative designs and craftsmanship
Passion:
- Deeply committed to exploring and pushing the boundaries of ceramic artistry
- Continuously experiments with new materials, firing techniques, and artistic concepts to evolve his craft
Personal Philosophy:
- Believes in the transformative power of art, aiming to evoke emotions and connections through his ceramic creations
- Advocates for sustainability in ceramics, using eco-friendly materials and practices whenever possible