Black clay is a striking material often used in pottery to create bold, dramatic ceramics. The deep and mysterious hue of black clay offers an intriguing contrast to traditional clay colors and enhances the overall visual appeal of ceramic pieces. The unique color comes from the addition of specific minerals or oxides that turn the clay black during firing. This guide will teach you how to make black clay from standard pottery clay, providing detailed instructions on using different methods, such as natural additives or commercially available stains. Whether you are aiming to craft intricate art pieces or robust functional ware, mastering how to make black clay enables you to add a distinctive character to your creations. With the right techniques, you can tailor the intensity of the black hue to suit your artistic vision, creating pieces that truly stand out.
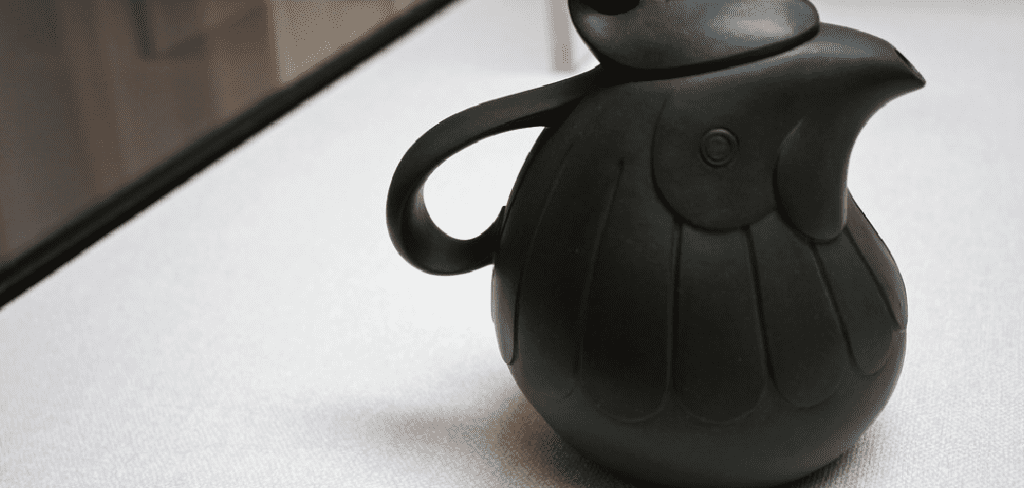
Understanding Black Clay
What is Black Clay?
Black clay refers to a type of pottery clay that transforms into a rich black color after being fired. It’s prized for its aesthetic appeal, making it a popular choice in both traditional and contemporary ceramics. The deep hue provides a visual depth that enhances the form and texture of ceramic pieces, offering artists a striking color option to complement their visions.
Why Make Your Own Black Clay?
Creating your own black clay presents the advantage of tailoring the color intensity to suit your specific needs. By adjusting the mixture of additives, such as manganese oxide, black iron oxide, or commercial black stains, you achieve complete control over the final appearance of your pottery. This customization ensures compatibility with various projects, allowing for a wide range of creative possibilities and uniformity in your work.
Types of Black Clay:
- Natural Black Clay: Naturally occurring in specific geographical areas, this clay already contains the minerals necessary to turn black during the firing process, offering an authentic and unaltered black finish.
- Man-Made Black Clay: This type combines regular pottery clay with particular oxides or stains. The controlled addition results in a black color post-firing, providing a versatile and predictable outcome suitable for a variety of ceramic styles.
Materials Needed
Creating black clay requires specific materials to ensure the desired color and quality. Here’s a list of the essential items you need to get started:
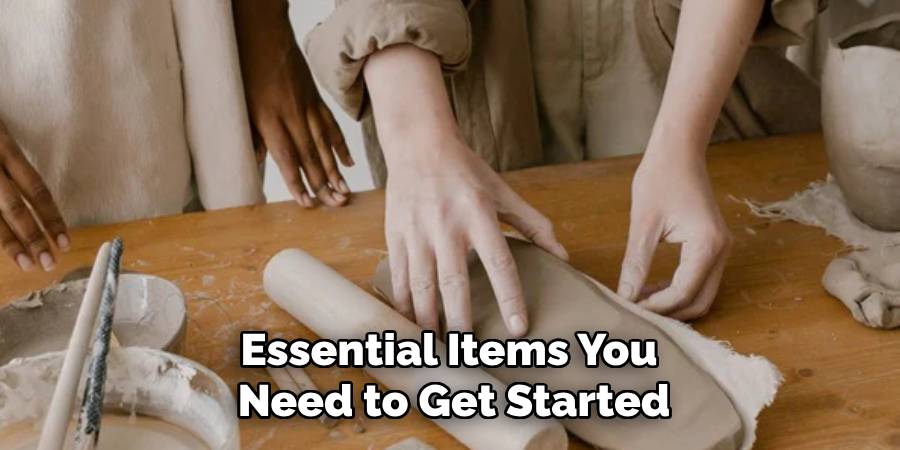
- Clay Body: You can use any clay body, such as stoneware or porcelain. Various additives will achieve the black coloration.
- Black Iron Oxide: This is a commonly used additive for creating black clay, providing a rich and deep black hue that enhances the visual appeal of the finished pieces.
- Manganese Dioxide: Another mineral option that can be mixed into the clay body to achieve a black color.
- Commercial Black Stains: These pre-made colorants are specifically designed for mixing with clay, offering a convenient and reliable method to achieve the desired shade of black.
- Water: Used to adjust the moisture level of the clay and ensure the consistency needed for your project.
- Blender or Mixer: Essential for ensuring even distribution of the additives throughout the clay body.
- Protective Gear: It is crucial to wear gloves and a mask when handling oxides and stains, as some of these materials can be hazardous to your health.
Preparing the Clay
Step 1: Choose a Clay Body
Begin by selecting a clay body that aligns with your intended firing temperature. Stoneware and porcelain are both excellent choices for making black clay due to their versatility and structural integrity. Opting for a white clay base will amplify the effect of the black colorants, resulting in a more intense final product. Consider the characteristics of the clay body you select, such as its plasticity and texture, ensuring they meet the requirements of your specific project.
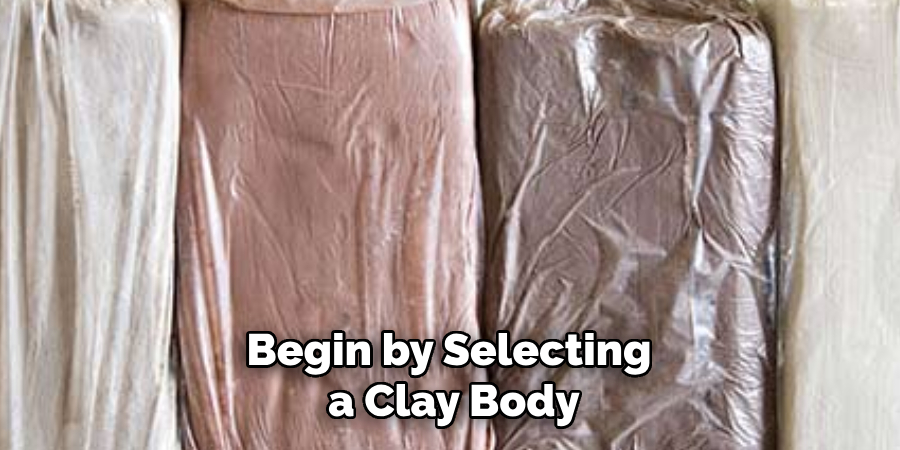
Step 2: Measure the Clay
Accurate measurement of materials is crucial in achieving consistent results. Start by weighing the amount of clay you intend to transform into black clay. This measurement is important not only for consistency but also to help you calculate the appropriate amount of oxide or stain required. Utilize a precise kitchen or laboratory scale to ensure accuracy. This systematic approach allows you to control the color intensity of your final product and guarantees that each batch you prepare will yield uniform results. Carefully document the weight of both the clay and the additives to facilitate adjustments and duplications in future projects, ensuring that your black clay creation aligns perfectly with your artistic expectations.
How to Make Black Clay: Adding Oxides or Stains to the Clay
Transforming your clay into a rich black hue requires careful incorporation of colorants. The process involves three main methods: using black iron oxide, manganese dioxide, or commercial black stains. Each method demands precision to achieve even coloration and desired intensity.
Using Black Iron Oxide
Step 1: Weigh Out the Black Iron Oxide
Begin by measuring the black iron oxide. Depending on the desired depth of color, you should add approximately 5% to 10% of the oxide based on the dry weight of your clay. This ensures a deep, consistent black once fired.
Step 2: Mix the Oxide Into the Clay Body
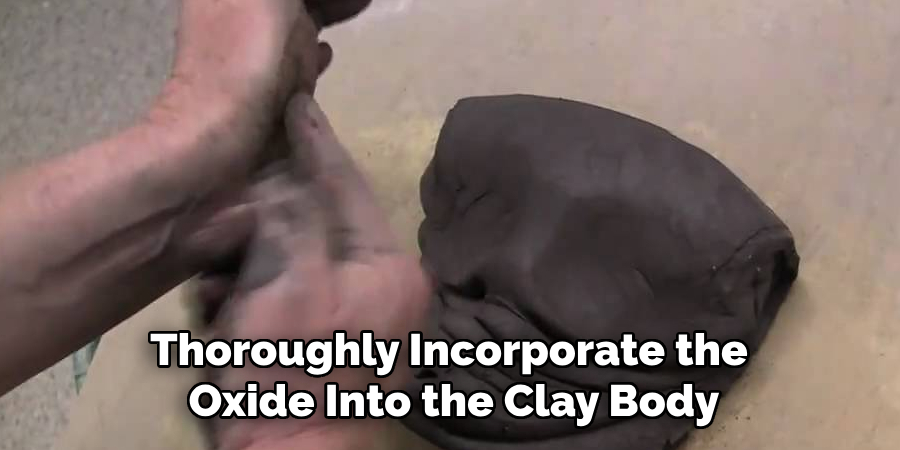
Thoroughly incorporate the oxide into the clay body. You can do this manually or with a blender to achieve a homogeneous mix. Ensure no streaks or patches remain, as these can disrupt the appearance of your final pottery piece.
Step 3: Adjust the Moisture Content
If the clay becomes too dry during mixing, add small amounts of water to reach the desired consistency. It’s crucial to maintain the right moisture level to make the clay workable.
Step 4: Wedge the Clay
Proceed to wedge the clay by kneading it repeatedly. This process further integrates the oxide into the clay, ensuring an even texture and color consistency throughout.
Using Manganese Dioxide
Step 1: Add Manganese Dioxide
Introduce manganese dioxide to the clay, typically around 5% to 8% of its dry weight. This will allow for a subtle variation in the black shade achieved, which is different from that with iron oxide.
Step 2: Mix the Manganese Thoroughly
Thoroughly blend the manganese dioxide into the clay body, ensuring that it is evenly distributed. Uneven mixing can lead to inconsistent coloring in your pottery.
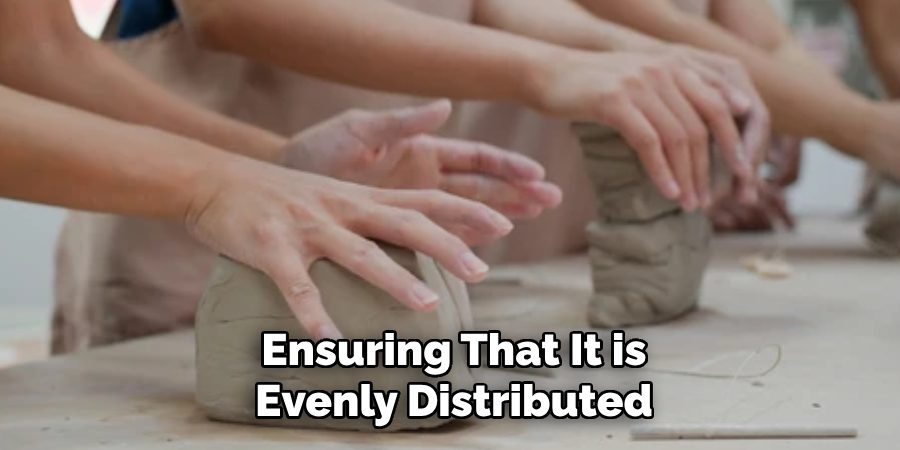
Step 3: Handle with Care
Manganese dioxide can be hazardous in large volumes, so always wear gloves and a mask to mitigate health risks. Proper handling ensures safety during the clay preparation process.
Step 4: Wedge the Clay
After mixing, knead or wedge the clay to achieve uniformity in color and texture. This step is vital to evenly distribute the black hue throughout the clay body.
Using Commercial Black Stains
Step 1: Purchase a Black Ceramic Stain
Select a black ceramic stain from a reliable pottery supplier. These products are formulated to provide consistent coloring across various types of clay.
Step 2: Follow Manufacturer’s Instructions
Adhere to the manufacturer’s guidelines regarding the stain-to-clay ratio, typically 5% to 10% by weight. Correct proportions are key to achieving optimal coloring.
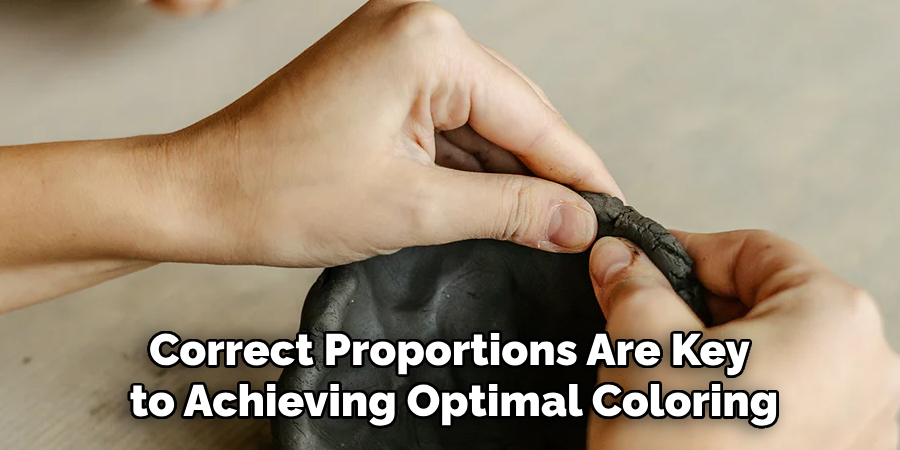
Step 3: Blend Thoroughly
Incorporate the stain into the clay using a mixer or blender. This ensures the pigment is evenly distributed, preventing any fading or patchiness in the final product.
Step 4: Adjust Moisture and Wedge
Finally, adjust the clay’s moisture as needed and wedge thoroughly. Uniform consistency is crucial for the clay’s workability and the success of your pottery endeavors.
Tip: For experimenters, try adjusting the amount of oxide or stain added to create darker or lighter shades. Always test small batches first to refine your color techniques before committing to larger quantities.
Testing the Black Clay
1. Make Test Tiles
Before committing your black clay to larger projects, creating a few small test tiles is important. This preliminary step allows you to evaluate the clay’s behavior and color development during firing. Mold several uniform, flat tiles from your prepared batch of black clay. Label each tile with an indelible marker to track the specific mixture of additives used, which will be essential for accurate comparisons later.
2. Drying the Test Tiles
Once the test tiles are formed, let them dry completely at room temperature. This drying phase is crucial as it helps reveal any irregularities in color consistency prior to firing. Monitor the tiles to ensure the color remains uniform throughout, and avoid placing them in direct sunlight, which may cause color variations or warping.
3. Firing the Test Tiles
After the test tiles are completely dry, proceed to bisque fire them at a low temperature, typically around cone 06 to 04. Bisque firing solidifies the clay and prepares it for glaze application. Following the bisque firing, apply a glaze of your choice, then proceed with the glaze firing according to your preferred cone. The culmination of the glaze firing will reveal the final color of the black clay, which is essential for assessing the visual appeal and quality of your clay mixture.
4. Evaluating Results
Once the glazed test tiles have cooled, carefully evaluate each one for color consistency and overall quality. The color of the black clay should be deep and uniform across all tiles. Inspect for any inconsistencies, such as a color that is too light, indicating a need to increase the amount of oxide or stain in future batches. Conversely, reducing the additives might be necessary if the color is excessively dark. An additional tip for successful testing is to maintain a detailed record of each test. Include specifics such as the types and amounts of additives used, the firing temperatures, and the glaze types. These meticulous notes will serve as an invaluable reference for perfecting your black clay formula, ensuring consistency in your future ceramic endeavors.
Safety Precautions
Handling Oxides and Stains
When handling oxides like iron oxide, manganese dioxide, or commercial stains, wearing protective gloves and a dust mask is crucial. These materials can pose health risks if inhaled or absorbed through the skin. Proper hand protection prevents direct contact, reducing the risk of irritation or harmful exposure.
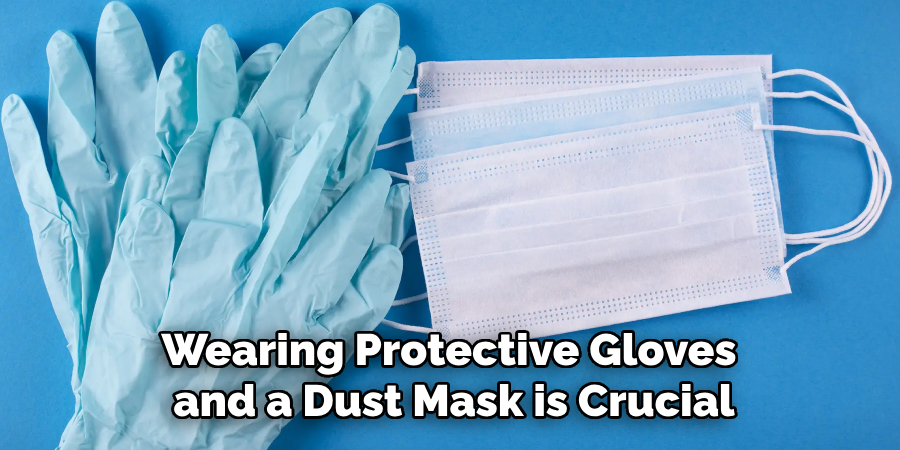
Ventilation
Always work in a well-ventilated area. This precaution helps minimize the inhalation of fine particles or fumes that may be released during the mixing and firing processes. Good airflow reduces the concentration of airborne hazards, thus protecting your respiratory health.
Storage
Store your black clay in an airtight container to prevent it from drying out. Ensure that the container is clearly labeled to distinguish it from other clay bodies. Proper storage also helps avoid potential mix-ups or misapplications in your pottery projects.
Storing and Using Black Clay
Storage:
Store black clay in plastic bags or airtight containers to prevent it from drying out. This measure ensures that the clay remains pliable and ready for immediate use. If the clay dries out, rehydrate it by adding small amounts of water and kneading it until it returns to a workable consistency. Proper storage preserves the quality and workability of the clay for future projects.
Usage:
Black clay can be used in the same way as any other clay, making it versatile for various pottery techniques. Whether you are wheel-throwing, hand-building, or slip-casting, black clay serves as an excellent medium. The deep final black color enhances the aesthetic of your pieces, offering striking contrasts, especially when paired with white or colored glazes. This unique color brings a bold and modern touch to your ceramic creations.
Conclusion
Understanding “how to make black clay” provides potters with the opportunity to explore a unique aesthetic in their creations. By incorporating oxides such as black iron oxide or manganese dioxide or opting for commercial stains, artists can tailor the depth and intensity of the black tone to their liking. Testing and adjusting the mixture is vital for achieving the desired visual outcome and ensuring project consistency.
Adhering to safety precautions is crucial when handling these materials, safeguarding both the artisan and the environment. Potters can produce striking black clay pieces by meticulously following each step, crafting the clay and evaluating and refining each batch. These pieces offer bold contrasts and create an eye-catching addition to any pottery collection, enriching artistic expression and allowing for innovation in ceramic design.
Specialization:
- Master of wheel-throwing, hand-building, and advanced glazing techniques
- Focus on creating both functional pottery and decorative art pieces
Recognition:
- Celebrated by collectors and art enthusiasts for creating one-of-a-kind pieces that blend artistry with functionality
- Participates in local and national exhibitions, earning accolades for his innovative designs and craftsmanship
Passion:
- Deeply committed to exploring and pushing the boundaries of ceramic artistry
- Continuously experiments with new materials, firing techniques, and artistic concepts to evolve his craft
Personal Philosophy:
- Believes in the transformative power of art, aiming to evoke emotions and connections through his ceramic creations
- Advocates for sustainability in ceramics, using eco-friendly materials and practices whenever possible