Ceramic beads are a charming and versatile addition to any jewelry-making project, celebrated for their unique aesthetic and durability. Whether used as focal points or as supporting accents, these beads bring a touch of handcrafted elegance to necklaces, bracelets, and earrings. The process of how to make ceramic beads involves several meticulous steps, starting with shaping raw clay into the desired bead form. Once the shapes are formed, they undergo a glazing process that introduces vibrant colors and a glossy finish.
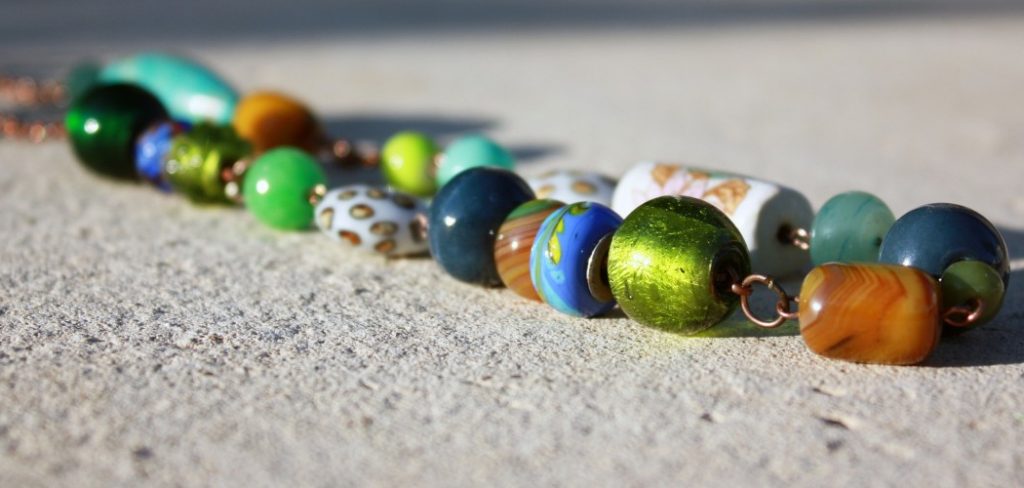
The final step, firing, is crucial as it solidifies the beads, endowing them with strength and longevity. Creating ceramic beads requires a basic toolkit, including a needle tool for piercing, a sculpting tool for shaping, and a kiln for firing. Additionally, rolling surfaces and a variety of glazes are essential for achieving different textures and finishes. Artisans can craft distinctive, personalized designs that reflect their creativity with these resources.
Tools and Materials Needed
Creating ceramic beads requires a combination of clay, tools, and equipment to attain the desired artistic finish and durability. Here is a detailed list of what’s essential for your bead-making journey:
Clay: The choice of clay significantly impacts the appearance and robustness of the finished beads. Earthenware clay offers a warm, rustic appearance and is quite easy to work with, making it ideal for decorative pieces. Stoneware, on the other hand, is more durable and presents a smooth finish suitable for everyday wear. Porcelain is highly prized for its delicate and translucent qualities, though it demands more skill and precision during crafting. For beginners, polymer clay offers an accessible starting point due to its malleability and the fact that it can be baked in a conventional oven. Air-dry clay is another alternative for those without kiln access, though it doesn’t offer the same strength as fired clay.
Tools for Shaping Beads: A rolling pin or clay roller is indispensable for flattening slabs of clay. Sculpting tools are invaluable to shape beads and create holes, as are common household items like toothpicks or skewers, which can also serve similar purposes. A needle or bead reamer is perfect for drilling clean, smooth holes.
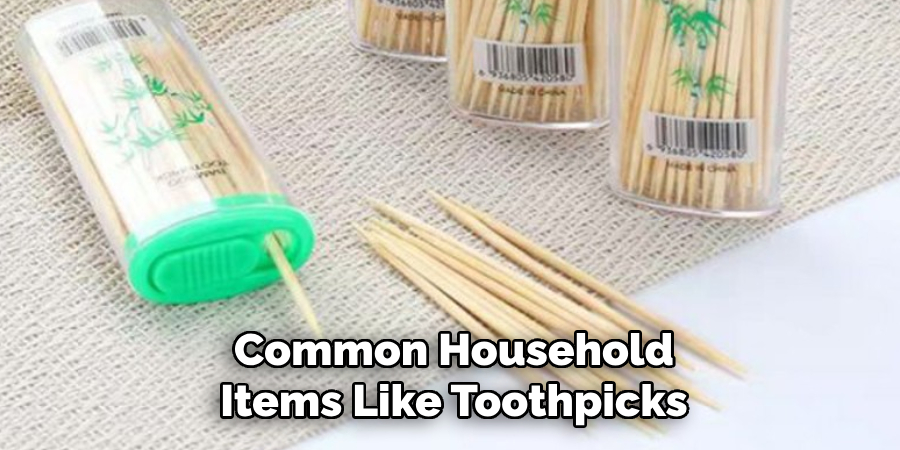
Glazing Materials: Food-safe ceramic glazes are recommended to add color and finish to the beads. Brushes or sponge applicators can be applied to create a personalized effect.
Kiln or Oven: A kiln is an essential part of the firing process, bringing the beads to the necessary temperatures that vary depending on the clay type—typically between 1,800°F and 2,400°F. For those using polymer or air-dry clay, a home oven offers a viable alternative, allowing beads to cure or harden at much lower temperatures yet truly capturing the essence of ceramic art.
Preparing the Clay for Bead Making
Conditioning the Clay
To begin the bead-making process, it’s crucial to condition the clay properly to ensure it’s soft, smooth, and free of air bubbles. Start by taking a manageable amount of clay and kneading it thoroughly. This process, known as wedging, is essential to eliminate air pockets, which can cause cracks during firing. Particularly with stoneware or porcelain, extra attention is required. Use a wedging technique by repeatedly pressing the clay down and rolling it forward. This motion aligns the clay particles and improves their plasticity, ensuring a smooth texture that’s easy to work with.
Shaping the Beads
Once the clay is well-conditioned, you can proceed to shape it into beads. Take small portions of clay and roll them between your palms to form balls or cylinders. For variety, experiment with different shapes by pressing some beads lightly to create disks or shaping them into ovals, teardrops, or even geometric forms like cubes. Adjusting the size and shape will add uniqueness to your jewelry pieces and allow for creative expression. Always keep the clay you are not using covered to prevent it from drying out while you work.
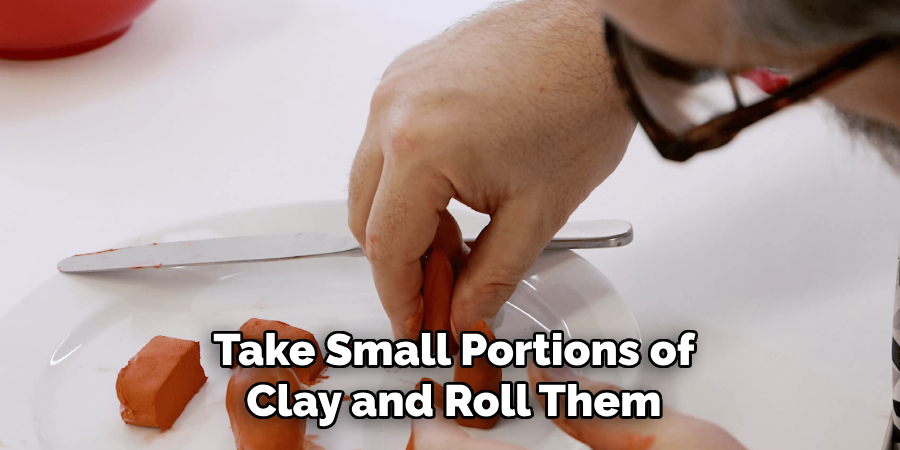
Creating Holes for Stringing
An essential step in bead preparation is creating holes for stringing. Use a needle, toothpick, or skewer to pierce each bead gently. Ensure that the hole is large enough to accommodate the stringing materials, like thread or wire, without compromising the bead’s structural integrity. A good practice is to rotate the tool slightly while piercing to help maintain a consistent round shape of the hole. Doing so prevents the hole from closing or altering size during the drying or firing process. Remember to smooth out any rough edges, as these can snag the stringing material once your beads are ready for assembly.
How to Make Ceramic Beads: Drying and Firing the Beads
1.Air-Drying the Beads (if Using Air-Dry Clay)
For crafters using air-dry clay, the drying process is straightforward yet requires patience. Once you have shaped your beads, leave them on a flat, non-stick surface to air-dry. This process can take anywhere from 24 to 48 hours, depending on the size of the beads and the humidity in your environment. To promote even drying and prevent warping, gently flip the beads every few hours. It’s important to ensure they are completely hard and dry before proceeding to any finishing techniques, as any remaining moisture can lead to weaknesses or defects in the final product. Patience during this stage is crucial, as rushing the process can compromise the quality and durability of the beads.
2.Firing Clay Beads in a Kiln
For traditional clay bead creators, firing is a critical step that transforms the clay into a solid, durable material capable of lasting generations. Once your clay beads are entirely dry, they are ready for the kiln. Firing beads in a kiln necessitates careful attention to temperature to prevent explosions caused by trapped moisture. Set your kiln to the appropriate temperature based on your clay type, generally ranging between 1800°F and 2300°F.
It’s advisable to fire in batches for consistent quality, particularly if you have a large collection of beads. Place the beads on kiln stilts or ceramic fiberboard to keep them from adhering to the kiln floor. This setup protects your beads from damage and ensures an even firing process throughout.
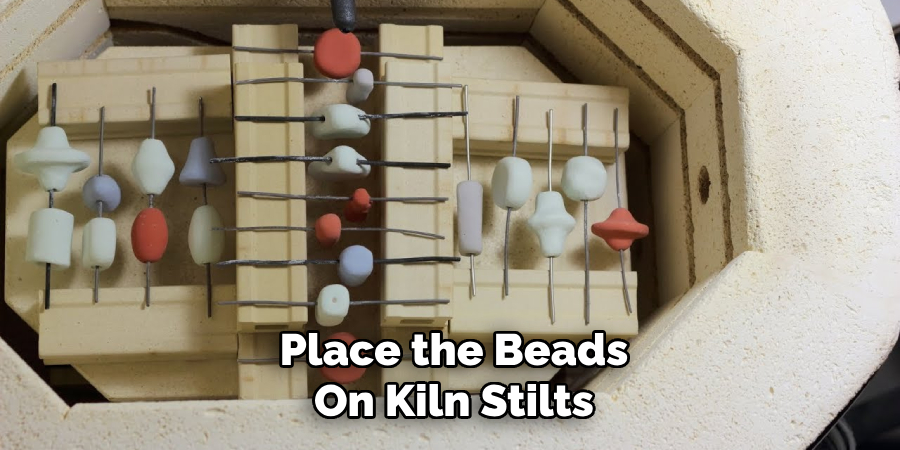
3.Alternative Oven-Baking for Polymer or Air-Dry Clay
Home ovens offer a practical alternative to kilns for those using polymer clay or choosing to replicate the look of ceramic beads with air-dry clay. Follow the specific manufacturer’s guidelines for baking polymer clay, typically at temperatures between 250°F and 300°F. As you bake your beads, pay close attention to ensure they do not overheat or crack. Small adjustments in position or temperature can prevent such issues.
Monitoring the beads during baking allows for any necessary interventions, ensuring that the finished product maintains its structural integrity and aesthetic appeal. Adjusting to your oven’s specifics can help achieve optimal results.
How to Make Ceramic Beads: Glazing and Decorating the Beads
Choosing and Mixing Glazes
When selecting glazes for ceramic beads, you have a variety of options—glossy, matte, and transparent finishes, each offering distinct aesthetic results. Glossy glazes provide a shiny, reflective surface, enhancing the vibrancy of the colors, while matte glazes offer a subtle, muted look that can add a sophisticated dimension to your beads. Transparent glazes allow the color of the base clay to shine through, making them excellent for showcasing natural clay tones. Understanding the difference between underglaze and overglaze techniques is crucial, as they significantly impact the final appearance.
Underglazes are applied before the final glaze coat and can be used for detailed patterns that will be sealed beneath a glossy layer, whereas overglazes are applied on top to create highlights and accents. When mixing glazes, aim for a consistency similar to heavy cream, adjusting with water as needed for smooth application.
Applying Glaze to Ceramic Beads
Begin by brushing or dipping your beads in glaze, ensuring even coverage. If brushing, use a soft brush and apply smooth, even strokes. Dipping the beads provides full coverage effortlessly, yet it’s important to shake off excess glaze. For a multi-layered effect, allow each glaze layer to dry fully before applying the next. Avoid clogging the stringing holes by using a toothpick or reamer to clear it after each layer.
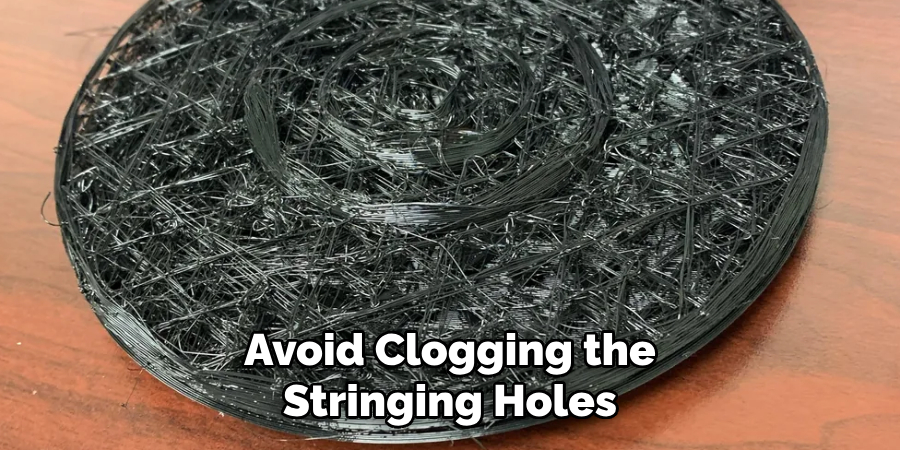
This practice ensures the beads can be strung without hindrance. If you wish to add intricate designs, consider using techniques like sponging, stippling, or employing fine brushes to craft patterns or detailed motifs that personalize your jewelry pieces.
Glazing Techniques for Unique Effects
Enhance your beads using advanced glazing techniques like marbling, which blends glazes to create swirling color patterns, or waxing, which uses a resist method to form intricate designs. Experiment with color combinations for marbled effects or create an ombre finish by layering gradients of color. For speckled finishes, employ a toothbrush or similar tool to flick glaze onto the beads.
Such methods not only elevate the aesthetics of your beads but also allow for creative expression and uniqueness in your jewelry.
Firing the Glazed Beads (Optional)
After glazing, an optional step is to fire the beads once more in a kiln to set the glaze. This process should occur at a lower temperature than the initial firing, typically around 1800°F. Careful positioning of beads on kiln stilts is crucial to avoid glaze drips that could cause them to stick to surfaces. By securely supporting each bead, you ensure that excess glaze drips away without causing adherence or damage, leaving your beads with the intended gloss and finish upon completion.
Polishing and Finishing Ceramic Beads
Polishing and Sanding
After your beads have been fired or completely dried, inspect them for any rough edges or imperfections. Use fine-grit sandpaper to gently sand these areas, ensuring a smooth and even surface. This step enhances the comfort and visual appeal of the beads when they are used in jewelry making. For beads with a glossy glaze, delicately polish the surface with a soft cloth to highlight the high shine. This polishing elevates the aesthetic and smooths out any minor inconsistencies in the glaze application.
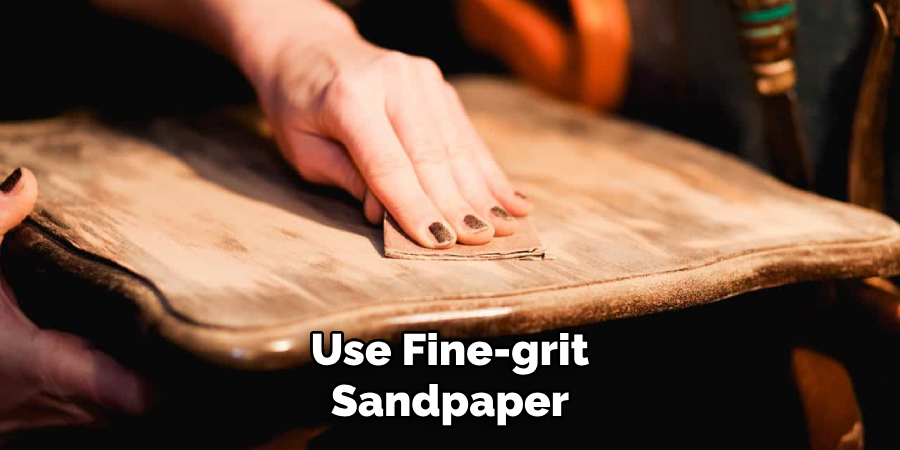
Sealing Non-Glazed Beads (Optional)
Unglazed beads can benefit from a layer of clear varnish or sealant. This additional step adds a protective coating and boosts their visual appeal. Sealing is particularly advantageous if the beads will experience frequent handling or environmental exposure as part of jewelry. The sealant forms a barrier against wear and tear, preserving the beads’ integrity and color over time.
Conclusion
Crafting ceramic beads is a rewarding process that begins with carefully shaping clay into the desired forms, followed by thorough drying and firing to achieve durability. Once bisque-fired, beads are meticulously glazed with finishes ranging from glossy to matte, with optional advanced techniques for effects like marbling and speckling. The firing of glazed beads ensures the setting of these finishes, after which the beads may be polished for enhanced shine. The final assembly of these beads into jewelry allows for expressing personal style and artistry.
Embracing experimentation with various shapes, glazes, and stringing methods can lead to truly unique and personalized creations. The journey of hand-crafting ceramic beads presents endless possibilities for creativity, offering the joy of making something tangible and the satisfaction of wearing or gifting pieces of art crafted with individual flair. Thanks for reading our blog post about how to make ceramic beads.
Specialization:
- Master of wheel-throwing, hand-building, and advanced glazing techniques
- Focus on creating both functional pottery and decorative art pieces
Recognition:
- Celebrated by collectors and art enthusiasts for creating one-of-a-kind pieces that blend artistry with functionality
- Participates in local and national exhibitions, earning accolades for his innovative designs and craftsmanship
Passion:
- Deeply committed to exploring and pushing the boundaries of ceramic artistry
- Continuously experiments with new materials, firing techniques, and artistic concepts to evolve his craft
Personal Philosophy:
- Believes in the transformative power of art, aiming to evoke emotions and connections through his ceramic creations
- Advocates for sustainability in ceramics, using eco-friendly materials and practices whenever possible