Test tiles are an essential tool in the world of ceramics and pottery, offering artists and potters a practical way to experiment with glazes and clay bodies. These small, manageable samples allow for a detailed exploration of the effects of different glazing techniques and clay mixtures. Understanding how to make test tiles is crucial, as they enable creators to make informed decisions about which materials and finishes will best suit their larger projects.
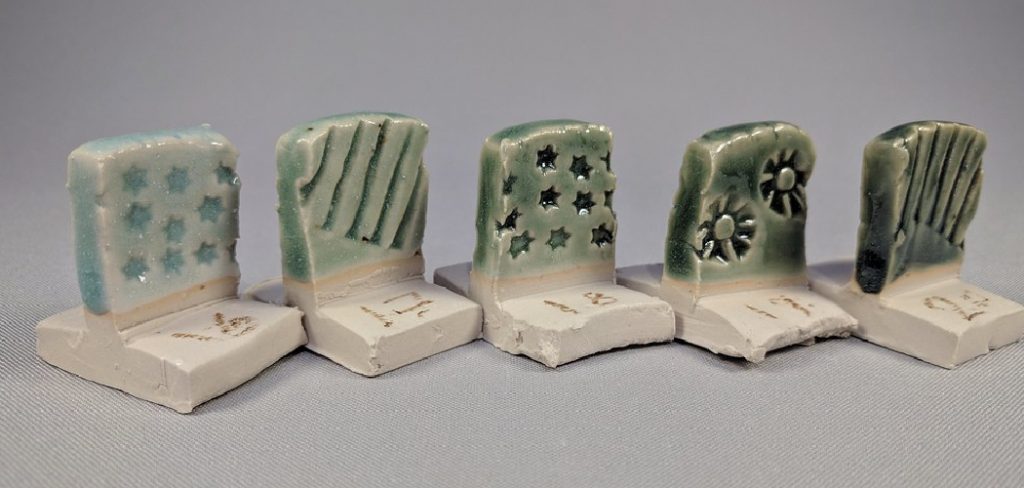
Potters can predict their creations’ final appearance and quality by observing how various glazes react with different clay bodies under specific firing conditions. In a studio setting, test tiles generally include glaze tests, which help evaluate color, texture, and finish, and clay body tests, which assess strength, shrinkage, and compatibility with glazes. Incorporating test tiles into the ceramic process ensures that artists can explore creative possibilities with confidence and precision.
Materials Needed
Creating test tiles requires selecting the appropriate materials and tools to ensure effective experimentation.
Clay: The type of clay used for test tiles significantly impacts the outcomes of glaze tests and overall ceramic quality. Common options include earthenware, stoneware, and porcelain. Earthenware, being more porous, fires at lower temperatures and is suitable for bright, colorful glazes. Stoneware offers a durable, versatile choice for medium to high firing ranges and is compatible with various glazes. Porcelain, known for its fine grain and transparency, requires high firing temperatures but yields a smooth, refined finish. Consider clay’s firing temperature and glaze compatibility to align with your project goals.
Tools: Essential tools for crafting test tiles include a sturdy rolling pin for flattening clay, precise cutting tools such as a knife or wire cutter, and a ruler for consistent sizing.
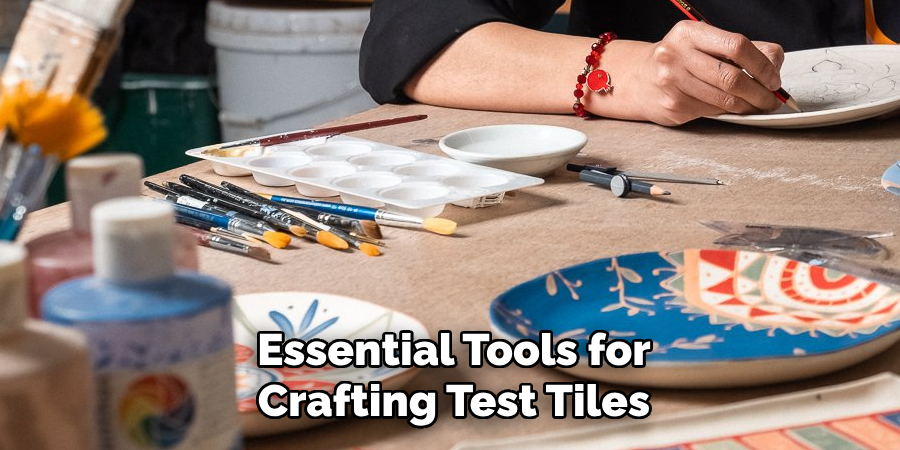
Glazes: Choose several glazes to test, ensuring each sample is labeled. Consider any additional ingredients or additives needed to achieve specific effects.
Kiln: Access to a kiln is crucial for firing test tiles. This equipment solidifies the clay and sets the glazes, revealing genuine results. Observing kiln safety protocols is necessary to ensure safe and successful firings.
Preparing the Clay
Step 1: Selecting the Clay
Choosing the appropriate clay body is the foundation for successful test tiles and impacts the ultimate results of your ceramic project. Begin by considering the desired properties of your finished pieces, such as durability, translucency, or aesthetic color after firing. Earthenware, stoneware, and porcelain each provide distinct characteristics.
Assess the firing temperature; earthenware typically fires at lower temperatures, while stoneware and porcelain require medium to high firing ranges. Consider shrinkage rates to predict dimensional changes and compatibility with your chosen glazes. The clay’s color post-firing can also influence the outcome, with some clays offering a natural tone that complements specific glaze selections. Ultimately, align your selection with your project goals to maximize effectiveness.
Step 2: Wedging the Clay
Wedging is crucial in preparing clay, as it ensures a uniform texture and removes air bubbles that can cause flaws during firing. Cut the clay into manageable pieces, then press the material down firmly on a wedging board. Both hands knead the clay into a spiral or ram’s head pattern. This process, akin to kneading dough, should be repeated until the clay achieves a smooth, consistent texture without lumps or air pockets. Proper wedging techniques enhance the quality of your test tiles and make the clay easier to work with.
Step 3: Rolling Out the Clay
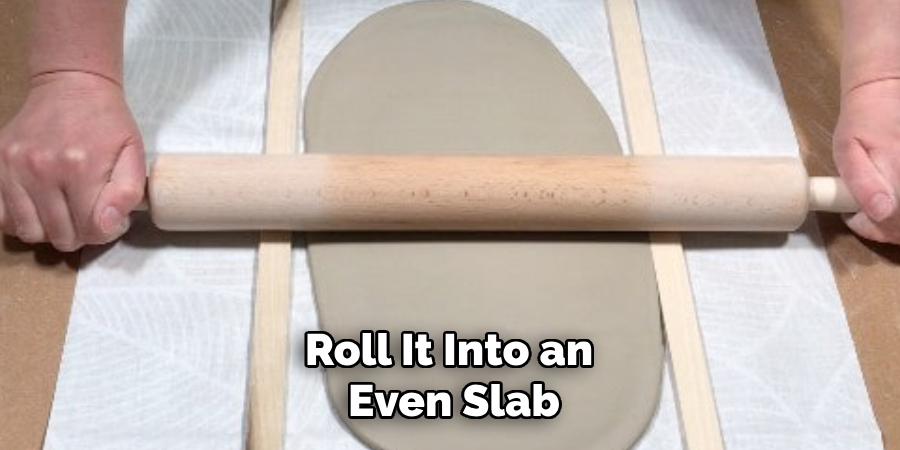
With the clay wedged and prepped, proceed to roll it into an even slab, ideally about 1/4 inch thick. Utilize a rolling pin alongside guide rails, such as wooden dowels, to ensure uniform thickness throughout. Start from the center of the clay mass and roll outward, applying even pressure to avoid irregularities. Consistently turn the clay slab to maintain shape and prevent sticking to the work surface. Uniform thickness is key for achieving consistent results during firing and glazing, as it ensures that shrinkage and glaze reactions remain predictable across each test tile.
How to Make Test Tiles: Cutting and Shaping the Tiles
Step 1: Measuring and Marking
To create uniform test tiles, measure and mark the desired size on your rolled clay slab, typically around 3 to 4 inches square. Use a ruler to define the dimensions clearly, ensuring each tile is consistent. A sharp tool, such as a needle or pencil, should be employed lightly to score the clay in straight lines. Clean, precise marking is essential, as it lays the groundwork for cutting without ragged edges, which can lead to uneven drying and firing results.
Step 2: Cutting the Tiles
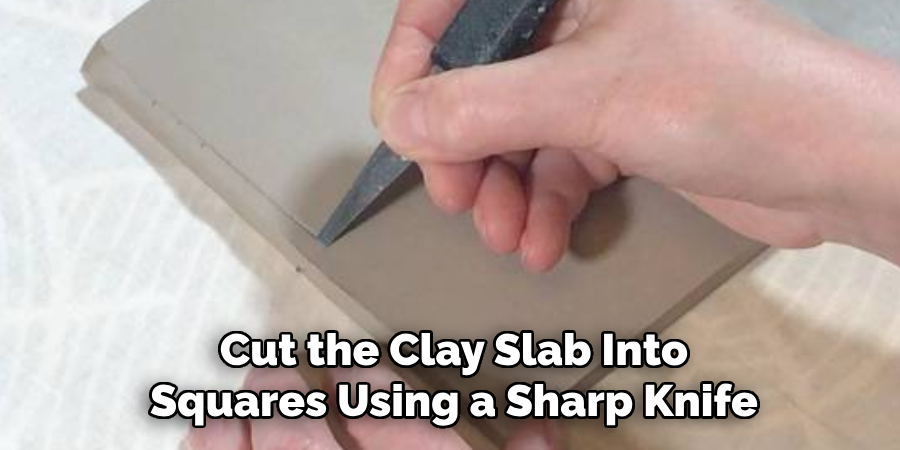
Once marked, cut the clay slab into squares using a sharp knife or a wire cutter. Hold the tool perpendicular to the slab to maintain straight, clean edges. Smooth, decisive movements will help avoid chipping or cracking, which might compromise the tile’s structural integrity during drying or firing. If needed, gently refine the edges with a damp sponge to enhance smoothness, ensuring each piece is ready for subsequent experimentation without imperfections.
Step 3: Texturing and Labeling
Adding texture or patterns to the test tiles can enhance glaze interaction and provide additional insight. Use stamps, combs, or household items like lace or cloth to imprint unique designs onto the moist clay surface. Such textures can reveal how glazes settle or pool differently. Don’t forget the crucial step of labeling each tile for future reference; inscribe identifying information such as glaze codes or clay body types onto the back or edge with a tool or underglaze. Accurate labeling ensures that you can track and compare results effectively, especially when testing a range of glazes or clay bodies.
How to Make Test Tiles: Drying the Tiles
Step 1: Initial Drying
The initial drying process is crucial to prevent cracks in your test tiles. Place the tiles on a flat, dry surface, preferably lined with cloth or newsprint, which absorbs excess moisture and promotes even drying. Ensure that the tiles are not in direct contact with too much airflow to maintain a gradual loss of moisture. This slow drying process helps in avoiding stress points that can lead to cracks or warping in the clay bodies.
Step 2: Controlled Drying Environment
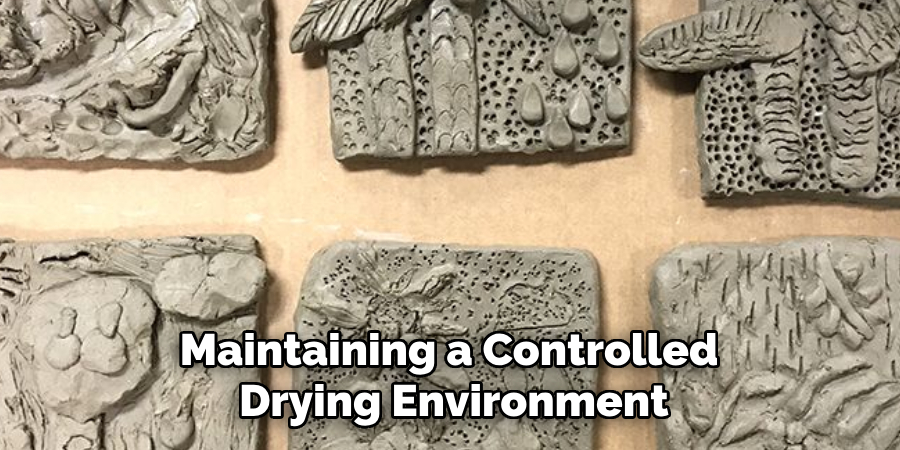
Maintaining a controlled drying environment is essential for consistent results. Avoid exposing the tiles to direct sunlight, which can cause rapid drying and lead to cracking or drafts that may result in uneven drying. Instead, place them in a stable environment, occasionally flipping each tile to ensure even drying on both sides. This practice helps maintain uniformity in drying rates, reducing the risk of surface tension issues.
Step 3: Checking for Dryness
Determining when the tiles are dry enough for firing requires careful attention. Visually, the tiles should appear light in color and uniform throughout, with no dark patches indicating moisture retention. Conduct a touch test by feeling the tiles’ surfaces; they should feel cool and dry. The tiles must reach a bone-dry state before firing to prevent explosions in the kiln due to trapped moisture rapidly turning into steam.
Firing the Test Tiles
Step 1: Loading the Kiln
Loading the kiln with your test tiles requires careful placement to ensure successful firing. Arrange the tiles with ample space between them to prevent sticking, and avoid placing tiles over each other to reduce stress. Utilize kiln furniture, such as shelves and posts, to create stable layers and ensure even heat distribution. This setup promotes safety and optimizes the results by facilitating uniform temperature exposure.
Step 2: Firing Schedule
Firing schedules depend on the clay type and desired glaze effects, typically involving two stages: bisque firing and glaze firing. Bisque firing is the initial stage, hardening the clay and preparing it for glazing. Follow it with a glaze firing, which matures the glaze and achieves the desired surface finish. Always adhere to the manufacturer’s guidelines for both clay and glaze, as they provide critical details on temperature settings and soak times essential for achieving optimal results without damaging the materials.
Step 3: Cooling Process
The cooling process is as critical as the firing itself to prevent thermal shock, which can cause cracking. Allow the kiln to cool down gradually by keeping it closed until it reaches a safe handling temperature. Depending on your kiln and materials, this may take several hours. As a guideline, wait until the kiln and its contents are warm but not hot to the touch before opening it. This slow cooling prevents abrupt temperature changes that could compromise the integrity of the fired tiles.
Applying Glazes to Test Tiles
Step 1: Preparing Glazes
Before applying glazes to your test tiles, it’s vital to ensure they are properly prepared. Mix them thoroughly to achieve a consistent suspension of the glaze materials. Depending on the type of glaze, straining the mixture through a fine sieve may be necessary to remove any lumps or particles, thus promoting a smooth finish. For efficiency and cost-effectiveness, prepare test amounts rather than full batches, especially if you are experimenting with new glaze recipes or testing different colorants. This approach minimizes waste and allows for multiple tests without excessive material use.
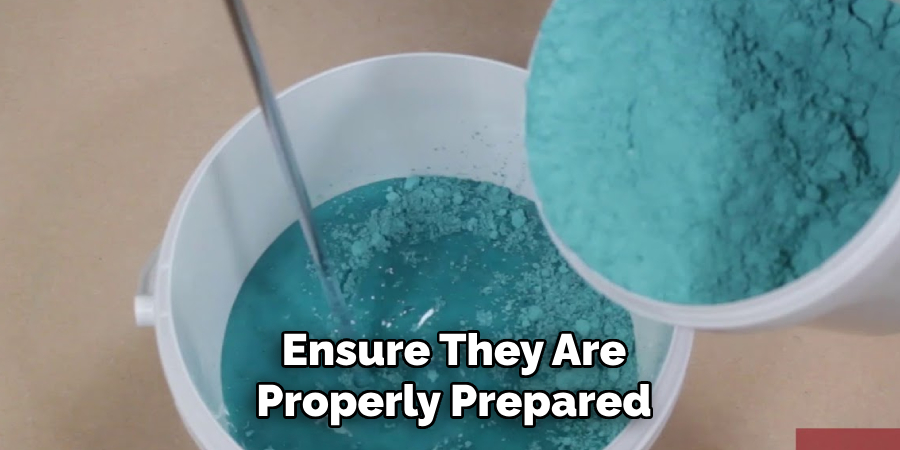
Step 2: Application Methods
There are various methods for applying glazes to tiles, each offering distinct results. Dipping is a popular technique where tiles are submerged briefly into the glaze to coat them evenly. Brushing allows for detailed application and control over specific areas, ideal for more intricate designs. Spraying, though more equipment-intensive, can offer a smooth and professional finish with minimal brush marks. Regardless of the method, aim for an even coating by applying multiple thin layers rather than a single thick layer to prevent drips and ensure consistent glaze flow over the surface.
Step 3: Labeling for Reference
After glazing, labeling each test tile with the glaze names and application methods is imperative. Use a permanent marker or label maker to clearly inscribe this information on the back or edges of the tiles. Accurate labeling is crucial for identifying glaze results and replicating techniques in the future. Proper documentation aids in understanding the interaction between the glaze and the clay body, providing valuable insights for ongoing experimentation.
Conclusion
In summary, learning how to make test tiles is an essential skill for any ceramic enthusiast, offering an organized approach to experimentation and discovery. Start by selecting suitable materials—appropriate clay bodies and glazes crucial for successful experiments. Follow with precision in shaping and drying tiles, ensuring they reach a perfectly dry state to prevent kiln mishaps.
Firing involves careful scheduling and cooling to arrive at desired results without compromising tile integrity. Applying glazes correctly involves understanding various methods, each contributing uniquely to the finish. Finally, documenting and analyzing outcomes helps make informed decisions in future projects. Incorporating test tile-making into your ceramic practice enhances learning and delivers immense satisfaction as you unveil an array of new glazes and techniques. Share your findings and experiences with fellow artists, enriching the collective knowledge and nurturing a supportive ceramic community.
Specialization:
- Master of wheel-throwing, hand-building, and advanced glazing techniques
- Focus on creating both functional pottery and decorative art pieces
Recognition:
- Celebrated by collectors and art enthusiasts for creating one-of-a-kind pieces that blend artistry with functionality
- Participates in local and national exhibitions, earning accolades for his innovative designs and craftsmanship
Passion:
- Deeply committed to exploring and pushing the boundaries of ceramic artistry
- Continuously experiments with new materials, firing techniques, and artistic concepts to evolve his craft
Personal Philosophy:
- Believes in the transformative power of art, aiming to evoke emotions and connections through his ceramic creations
- Advocates for sustainability in ceramics, using eco-friendly materials and practices whenever possible