Crafting tiles from clay is an intriguing blend of art and skill. These versatile tiles, perfect for floors, walls, or decoration, start as raw clay and are meticulously shaped, dried, and fired to ensure both strength and beauty. Mastering the basics of clay work allows you to create stunning and practical tiles that can transform any space. This guide will take you through the key steps on how to make tiles from clay, from choosing the perfect clay to applying finishing techniques for a polished, professional result.
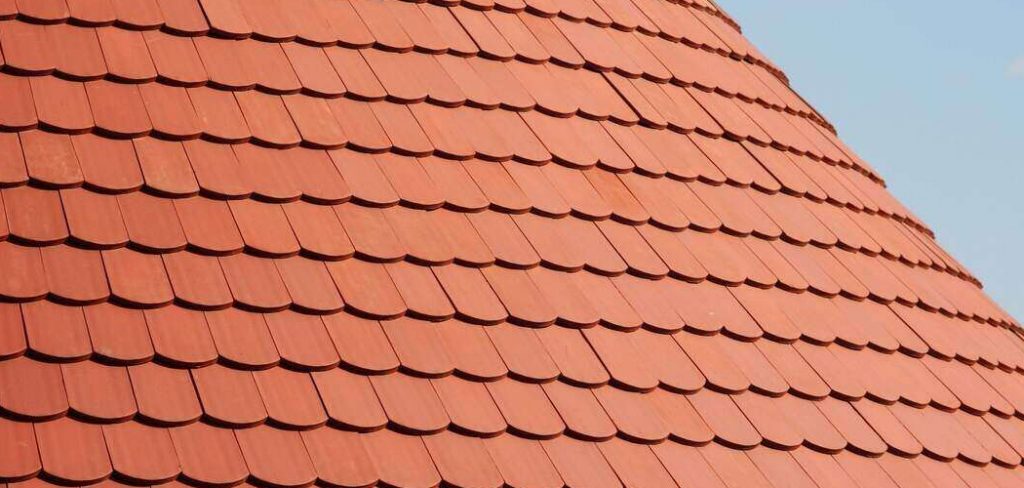
Types of Clay Suitable for Tile Making
Selecting the right type of clay is crucial for creating durable and attractive tiles. Three primary types of clay are commonly used in tile making: earthenware, stoneware, and porcelain.
- Earthenware Clay: This type of clay is widely used due to its availability and ease of workability. It fires at a lower temperature and has a natural red or brown color. Earthenware tiles are typically porous, making them ideal for decorative tiles but less suitable for areas with high moisture.
- Stoneware Clay: Known for its strength and durability, stoneware is a popular choice for functional tiles such as flooring and countertops. It fires at a higher temperature, resulting in a dense and less porous finish. Stoneware can also come in a range of natural colors, offering versatility in design.
- Porcelain Clay: Porcelain clay is prized for its fine grain and high firing temperature. It creates a very hard and dense tile that is both stain-resistant and waterproof. While more challenging to work with due to its delicate nature before firing, porcelain tiles are perfect for bathrooms and kitchens due to their durability and sleek appearance.
Each type of clay brings its own advantages and aesthetic qualities, making it essential to choose based on the intended use of your tiles.
Materials and Tools Needed
Before you begin crafting your own tiles, it’s important to gather all necessary materials and tools to ensure a smooth and efficient process. Here’s a rundown of what you’ll need:
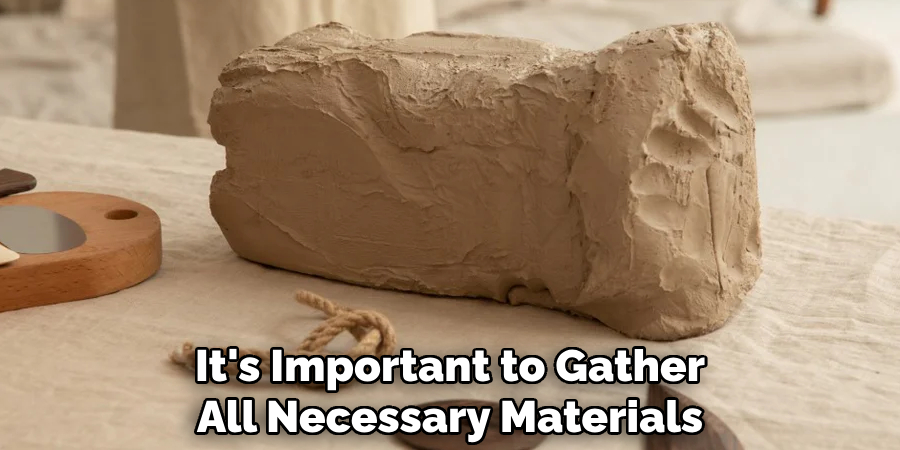
Materials
- Clay: Depending on the tile type you wish to create, choose earthenware, stoneware, or porcelain clay.
- Water: Used for moistening the clay as needed during the shaping and smoothing phases.
- Glazes: Various colors and finishes available for applying to your tiles for color and protection.
Tools
- Rolling Pin: Used for flattening the clay to the desired tile thickness.
- Tile Cutters or Rulers: Essential for cutting the clay into consistent tile shapes and sizes.
- Sponge: For smoothing edges and surfaces, ensuring a professional finish.
- Kiln: Required for firing the tiles, transforming them from raw clay to a hardened product.
- Work Surface: A sturdy, clean area for working with clay, preferably covered in cloth or paper to prevent sticking.
- Brushes: For applying glazes or decorative details to the tiles.
Having these materials and tools on hand will prepare you to embark on your tile-making journey, ensuring that each step of the process is manageable and enjoyable.
10 Methods How to Make Tiles from Clay
1. Choose the Right Clay
Selecting the right clay is fundamental in creating tiles with good durability and aesthetic appeal. Earthenware clay is popular for tile-making due to its workability and low firing temperature, though stoneware is also a good choice for its strength and resilience. Each type of clay has its own shrinkage rate and firing requirements, so understanding these will ensure tiles that are durable and less prone to cracking or warping. Testing small samples of different clays before committing can help determine which best suits your project.
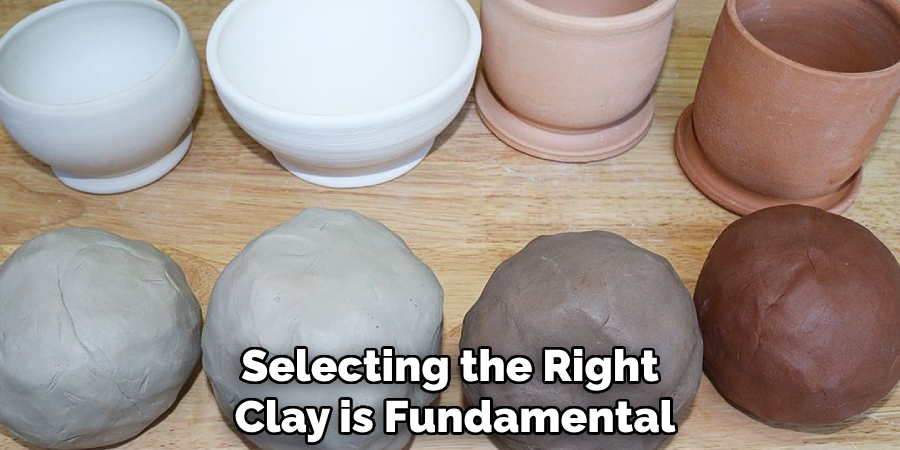
2. Prepare the Clay Properly
Before shaping tiles, thoroughly prepare the clay to eliminate air bubbles, which can cause cracks during firing. Start by wedging the clay—kneading it in a rolling and folding motion—to remove trapped air and improve its plasticity. Properly wedged clay is smooth, pliable, and consistent in texture, making it easier to shape and reducing the risk of imperfections. Spending extra time on preparation ensures a smoother, more workable material for uniform tiles.
3. Roll the Clay to an Even Thickness
Using a rolling pin or slab roller, roll the clay out to the desired tile thickness, generally around ¼ inch for regular tiles and ½ inch for thicker, more durable tiles. To maintain an even thickness, place wooden guide sticks of the same height on either side of the clay. Rolling to an even thickness is essential for consistent firing and a professional finish. Uneven tiles may crack, warp, or not fit together well, so precision here is key.
4. Cut the Clay into Tile Shapes
Once the clay is rolled evenly, use a metal ruler and a sharp clay-cutting tool or knife to cut out square, rectangular, or custom shapes. Press firmly to achieve clean edges and ensure consistent dimensions. Alternatively, use a cookie-cutter or tile template for uniformity, especially for intricate designs. Neat, well-cut shapes create a cohesive look and help tiles fit seamlessly together during installation, giving a polished result.
5. Smooth the Edges and Surface
After cutting, smooth the edges with a damp sponge or clay tool to remove roughness or small imperfections. Smoothing prevents sharp edges and gives the tile a refined look, which is especially important for tiles that will be handled or touched frequently. Run the sponge lightly over the surface as well, removing minor irregularities and preparing the tile for any decorative additions. Taking time for these finishing touches adds to the overall quality of each tile.
6. Create Texture or Design Impressions
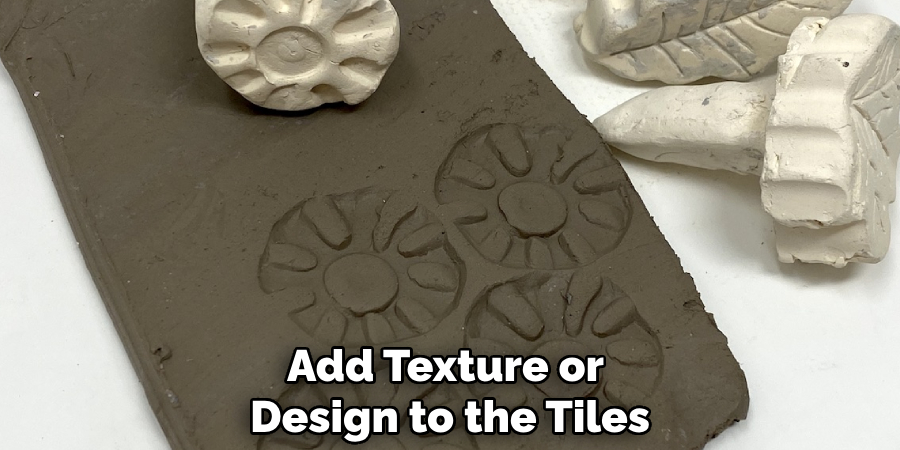
If you wish to add texture or design to the tiles, do so while the clay is still damp but firm. Use stamps, leaves, or fabric to press patterns into the clay, or carve designs with a pottery tool for custom detailing. Patterns can range from simple lines to complex shapes, allowing you to create a unique set of tiles that adds personality to your space. Experimenting with textures and designs gives each tile character and transforms them into functional pieces of art.
7. Dry the Tiles Slowly and Evenly
Drying clay tiles too quickly can cause warping or cracking, so place them on a flat, absorbent surface and cover them lightly with plastic to slow down the drying process. Allowing tiles to dry gradually and flipping them every day or so helps distribute moisture evenly and reduces the chance of bending. Aim for at least a week of drying time, depending on the tile thickness and climate. Patience here leads to more durable, crack-resistant tiles ready for firing.
8. Bisque Fire the Tiles for Durability
Once fully dried, fire the tiles in a kiln for the first round, known as bisque firing. This initial firing hardens the clay, preparing it for glazing or final decorative steps. Bisque firing typically ranges between 1730°F and 1940°F, depending on the clay type. After this step, the tiles are more resilient and ready to absorb glaze. Bisque firing also makes the tiles more manageable and less prone to accidental breakage, making it essential in the tile-making process.
9. Apply Glaze for Color and Protection
Glazing not only adds color but also provides a waterproof, durable finish for the tiles. Use a brush to apply glaze in even layers, or dip the tiles into the glaze for a more consistent coating. Make sure the glaze is compatible with the clay type and firing temperature to avoid issues during the final firing. Glazing allows for endless creative freedom, from vibrant colors to subtle finishes, and it protects the tiles from moisture, making them suitable for kitchens, bathrooms, and other high-use areas.
10. Final Fire to Set the Glaze
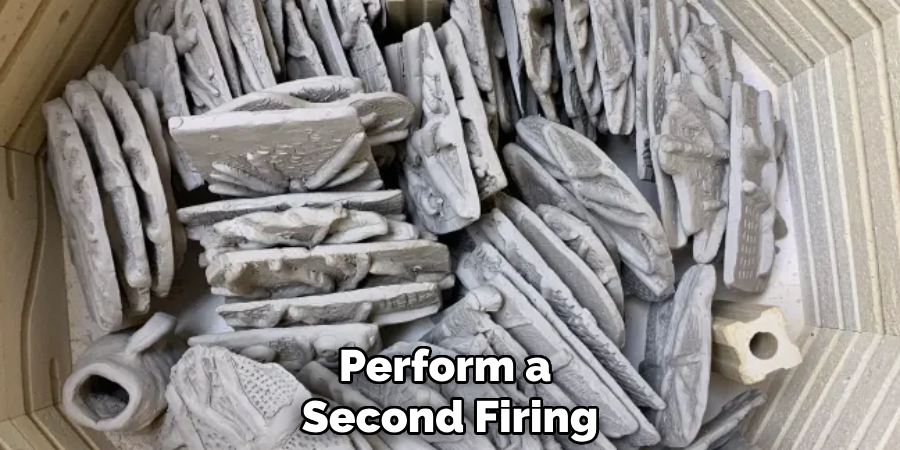
After glazing, perform a second firing, known as the glaze firing, at a higher temperature than the bisque fire. This final firing melts the glaze, forming a glass-like coating that is durable and visually appealing. Glaze firing temperatures vary but typically range from 2100°F to 2300°F, depending on the type of glaze. Allow the kiln to cool gradually after firing to prevent thermal shock, which can damage the tiles. The second firing completes the tile-making process, yielding a strong, beautiful, and ready-to-install product.
Common Mistakes to Avoid
When making clay tiles, there are several common mistakes that can compromise the quality and durability of the end product. One frequent error is insufficient clay preparation, which can lead to air bubbles and subsequent cracking during firing. Always wedge the clay thoroughly before shaping. Uneven rolling is another mistake to avoid. It crucially impacts the tile’s consistency, so be diligent in maintaining even thickness with guide sticks.
Rushing the drying process is also detrimental, often causing warping and cracking. Instead, allow ample time for the tiles to dry slowly and evenly, covering them lightly with plastic and ensuring regular flipping. Additionally, not allowing the glaze to dry adequately before firing can result in blistering or uneven finishes.
Conclusion
Crafting clay tiles is an intricate process involving careful selection of materials, precise shaping, texturing, and controlled firing. By following these steps, from clay preparation to final firing, you can create stunning, functional tiles with a professional finish that will enhance any space with their handmade charm and durability. Whether for a small project or a large installation, these methods offer a comprehensive guide to making tiles from clay that are both beautiful and built to last.
Specialization:
- Master of wheel-throwing, hand-building, and advanced glazing techniques
- Focus on creating both functional pottery and decorative art pieces
Recognition:
- Celebrated by collectors and art enthusiasts for creating one-of-a-kind pieces that blend artistry with functionality
- Participates in local and national exhibitions, earning accolades for his innovative designs and craftsmanship
Passion:
- Deeply committed to exploring and pushing the boundaries of ceramic artistry
- Continuously experiments with new materials, firing techniques, and artistic concepts to evolve his craft
Personal Philosophy:
- Believes in the transformative power of art, aiming to evoke emotions and connections through his ceramic creations
- Advocates for sustainability in ceramics, using eco-friendly materials and practices whenever possible