Underglaze provides a vibrant color palette for ceramic artists, adding detail and depth to pottery pieces. However, it can present a challenge when firing, as it has the potential to stick to the kiln shelf, leading to damage or imperfections in the piece. Ensuring that underglaze does not adhere to the shelf is crucial for preserving the quality and integrity of ceramic creations. By understanding the properties of underglaze and employing specific techniques during the preparation and firing processes, artists can maintain the desired finish while preventing unwanted sticking. This guide will outline key steps and tips for how to prevent underglaze from sticking to the kiln shelf.
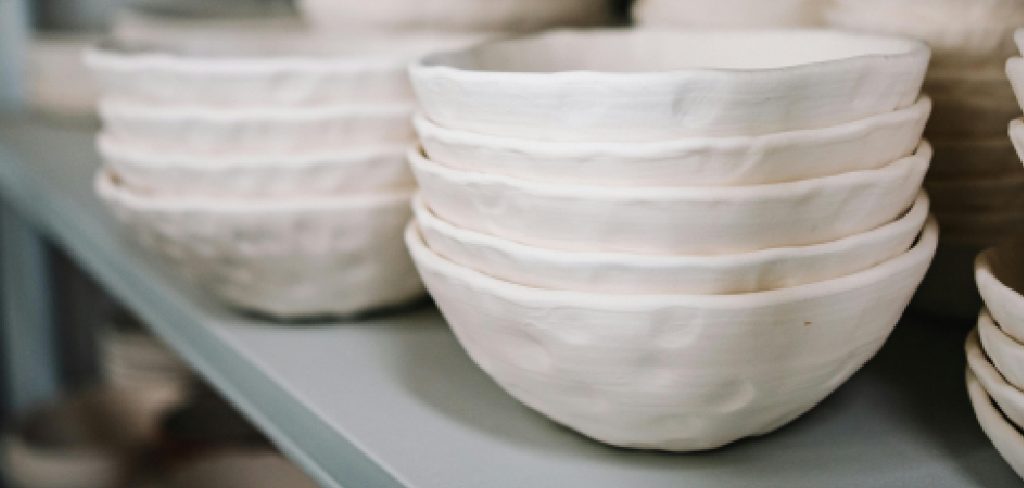
What is Underglaze?
Underglaze is a type of ceramic decoration applied to pottery before it is glazed and then fired in a kiln. Composed primarily of clay, pigments, and other additives, underglaze is specifically designed to withstand the high temperatures of firing without melting or losing its vibrant color. Unlike overglaze, which is applied on top of a glazed surface, underglaze is used directly on the pottery’s bisque surface. This allows artists to create intricate designs and patterns that are protected by the subsequent glaze layer. Moreover, underglaze can be applied using various techniques such as painting, spraying, or dipping, offering versatility and creative freedom for ceramic artists.
Importance of Proper Preparation
Proper preparation is essential in ensuring that underglaze does not adhere to the kiln shelf and that the final ceramic piece maintains its intended quality. The preparation process begins with selecting the right type of underglaze that suits the clay body and firing temperature. Artists should ensure their pottery is completely dry before applying underglaze to minimize moisture content, which can lead to expansion and sticking during firing.
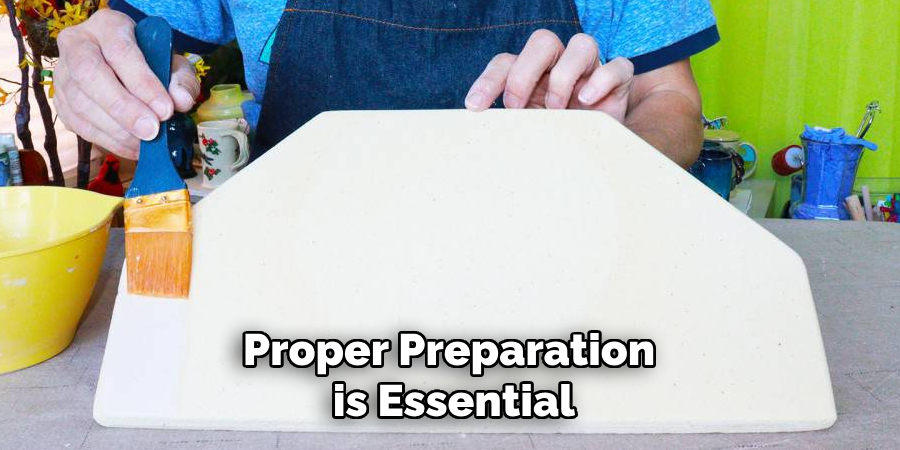
Applying a thin, even coat of underglaze and allowing it to dry thoroughly before bisque firing can greatly reduce the risk of adhesion. Additionally, using kiln wash on shelves or employing stilts can provide an extra barrier that prevents the glaze from sticking, preserving both the pottery and the kiln equipment. By taking these steps, ceramic artists can avoid common pitfalls and achieve smooth, flawless finishes in their work.
Why Underglaze Sticks to the Kiln Shelf
Underglaze sticking to the kiln shelf is primarily a result of factors related to the composition and interaction of materials during the firing process. One of the common reasons is over-application, where a thick layer of underglaze is more likely to become fluid and adhere to the shelf. Additionally, if the underglaze contains flux materials, they can lower the melting point, causing the underglaze to soften and stick as it becomes molten at high temperatures.
Moisture content in the pottery can also contribute to sticking; if the piece is not completely dry before firing, the expansion of moisture turning into steam can push the underglaze outward, leading to adhesion to the kiln shelf. Finally, uneven drying or firing conditions can exacerbate these problems by causing differential expansion and contraction in the clay body and underglaze. Understanding these factors can help ceramists avoid mishaps and preserve their artwork through careful preparation and firing control.
10 Methods How to Prevent Underglaze from Sticking to the Kiln Shelf
For pottery enthusiasts and ceramic artists, nothing is more frustrating than finding your beautiful creations stuck to the kiln shelf after firing. Not only can it damage the piece you worked so hard on, but it can also harm your kiln shelves.
1. Use Kiln Wash
Kiln wash is a protective layer applied to kiln shelves to prevent glaze and underglaze from adhering to them. To use kiln wash effectively, apply a thin, even coat to the shelf before firing. Ensure it is completely dry before setting your pieces on top. This method is cost-effective and widely used in pottery studios.
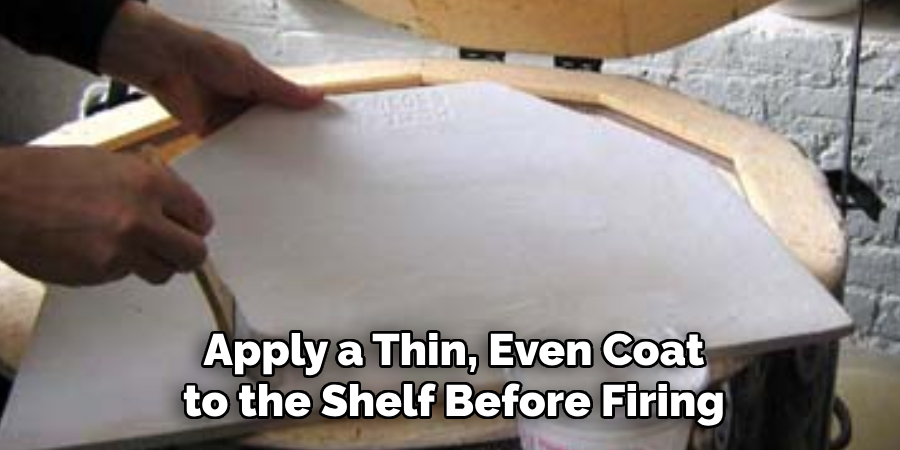
2. Apply Wax Resist
Wax resist is another great way to keep underglaze from sticking. By applying wax to the base of your pottery piece, you create a barrier that prevents the underglaze from coming into contact with the kiln shelf. Be sure to only apply the wax to areas that will touch the shelf.
3. Opt for Stilts or Bead Racks
Stilts and bead racks lift your pottery off the kiln shelf, minimizing direct contact and reducing the chance of sticking. Made from high-temperature resistant materials, these tools are perfect for small to medium-sized pieces.
4. Use Parchment Paper or Kiln Paper
Parchment paper and kiln paper are simple yet effective solutions. Place a sheet between your pottery and the kiln shelf to act as a buffer. Ensure you’re using materials designed for kiln use to avoid any melting or burning.
5. Adjust Firing Temperature and Schedule
Sometimes, sticking is caused by firing at inappropriate temperatures or schedules. Double-check the firing range of your underglaze and ensure your kiln settings match. Gradual heating and cooling cycles can also help prevent problems.
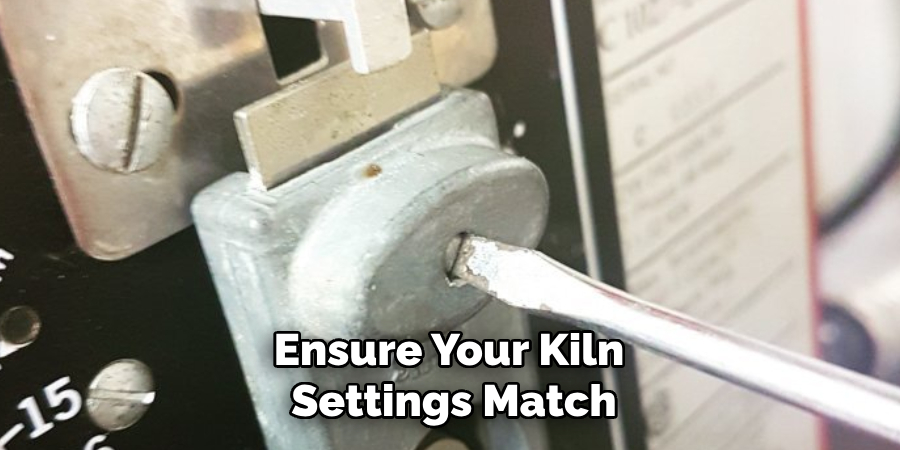
6. Avoid Over-Application of Underglaze
Applying too much underglaze can lead to drips and runs, increasing the chances of it sticking to the kiln shelf. Apply thin, even coats and allow each layer to dry before adding another.
7. Use Kiln Sand or Alumina Hydrate
These powders can be sprinkled onto the kiln shelf to act as a physical barrier against sticking. They create a slight cushion between the two surfaces, allowing for easy removal after firing.
8. Invest in Quality Underglazes
Not all underglazes are created equal—some are more prone to sticking than others. Investing in high-quality, well-reviewed products can minimize issues and improve your overall results.
9. Experiment with Underglaze Brands and Formulas
Different brands and formulas can behave differently in the kiln. If you encounter consistent issues, try switching up the brand or formula to find one that works better with your firing conditions.
10. Maintain and Clean Your Kiln Shelves Regularly
Regular maintenance and cleaning of your kiln shelves can prevent buildup that may cause sticking. After each firing, inspect the shelves for residue and gently scrape or sand them clean.
Maintenance and Upkeep of Kiln and Shelves
Ensuring the longevity and effectiveness of your kiln and shelves involves regular maintenance and upkeep, which are crucial for preventing underglaze from sticking and preserving the quality of your ceramics. First, routinely inspect your kiln shelves for signs of glaze drips or residue. Promptly scrape off any buildup with a rigid tool or sandpaper, taking care not to damage the shelf surface.
Applying a fresh layer of kiln wash periodically is essential to protect the shelves from future firing mishaps. Additionally, monitor your kiln’s performance by checking its elements, thermocouples, and other parts for any wear or damage. Replace these components as needed to maintain consistent firing temperatures and schedules. It’s also beneficial to keep detailed records of your kiln firings, noting the temperatures and outcomes, which can help identify patterns or issues over time. By diligently caring for your kiln and shelves, you can ensure a smooth firing process and produce high-quality ceramic pieces.
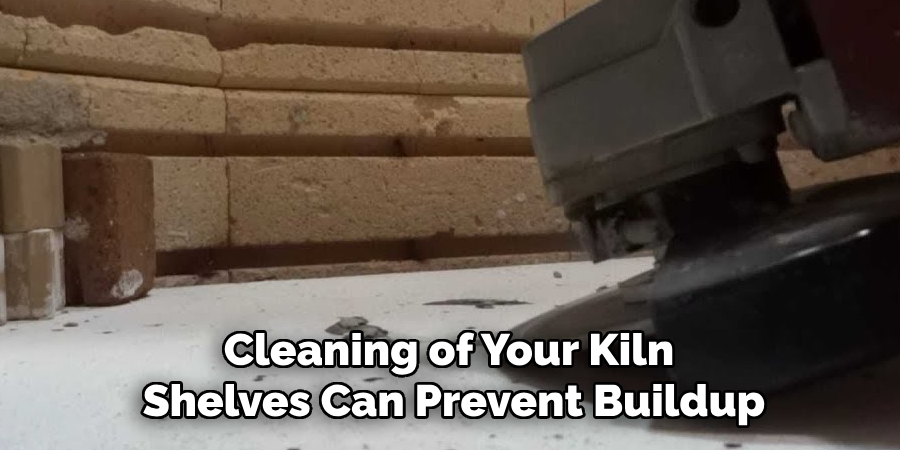
Troubleshooting Common Issues
Even with the best prevention methods, issues with underglaze sticking can occasionally arise. Here are some common problems and their solutions:
Problem 1: Glaze Runniness Leading to Sticking
Solution: If your underglaze is running and causing sticking, evaluate the thickness of your application. Ensure that the layers are thin and allow each coat to dry before adding another. You may also want to check if your firing temperature is appropriate for the underglaze used.
Problem 2: Uneven Heating Causing Differential Expansion
Solution: Ensure that your kiln is heating evenly and that the pieces are placed so that hot and cool spots are minimized. Adjust the placement of your kiln shelves and the arrangement of pieces to promote an even temperature distribution throughout the kiln.
Problem 3: Residual Moisture in the Clay
Solution: Make sure your clay pieces are completely dry before firing. A longer drying period or the use of a low-temperature pre-firing (or bisque firing) can help remove excess moisture and reduce expansion issues.
Problem 4: Inadequate Kiln Wash Coating
Solution: If pieces are sticking due to insufficient kiln wash, make sure to apply a thorough and even coating on your shelves. Allow the wash to dry completely before placing work on the shelves to ensure an effective barrier.
Problem 5: Inconsistent Underglaze Quality
Solution: If certain underglazes consistently cause problems, consider changing brands or formulas. Experimenting with other products might provide better results under your firing conditions.
Problem 6: Notching or Chipping of Shelves
Solution: Check and maintain the surface of your kiln shelves. Smooth out any rough areas with sandpaper and reapply kiln wash regularly to protect against surface damage that can promote sticking.
Conclusion
Achieving successful ceramic firing with underglaze requires a combination of proper techniques, tools, and vigilance. By adhering to best practices such as applying even underglaze layers, experimenting with different brands, and ensuring your kiln equipment is well-maintained, you can significantly decrease the likelihood of pieces sticking to the kiln shelves. Thanks for reading, and we hope this has given you some inspiration on how to prevent underglaze from sticking to the kiln shelf!
Specialization:
- Master of wheel-throwing, hand-building, and advanced glazing techniques
- Focus on creating both functional pottery and decorative art pieces
Recognition:
- Celebrated by collectors and art enthusiasts for creating one-of-a-kind pieces that blend artistry with functionality
- Participates in local and national exhibitions, earning accolades for his innovative designs and craftsmanship
Passion:
- Deeply committed to exploring and pushing the boundaries of ceramic artistry
- Continuously experiments with new materials, firing techniques, and artistic concepts to evolve his craft
Personal Philosophy:
- Believes in the transformative power of art, aiming to evoke emotions and connections through his ceramic creations
- Advocates for sustainability in ceramics, using eco-friendly materials and practices whenever possible