Are you someone who loves the art of pottery and wants to create your own kiln at home?
How to set up a kiln at home can transform your creative projects and significantly expand your artistic capabilities. Whether you’re an aspiring ceramicist, a glass artist, or simply interested in exploring new crafts, having your kiln allows for limitless experimentation and convenience. However, setting up a kiln involves careful consideration of space, safety, and the specific requirements of your chosen kiln model. Ensuring proper ventilation, an appropriate power supply, and adherence to local safety regulations is essential to create a safe and functional workspace.
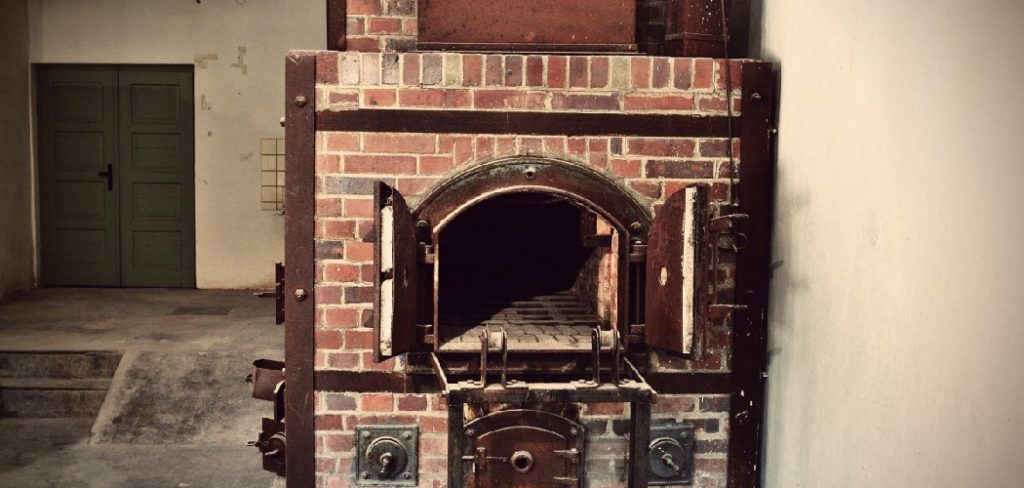
With the right preparation and knowledge, you can successfully set up a kiln in your home to support your creative endeavors.
What Will You Need?
Before setting up a kiln at home, it’s essential to gather all the necessary materials and tools. This will not only streamline the process but also ensure that you have everything you need on hand. Some of the essential items you’ll need include:
- A Kiln: This is the main component of your setup, and there are various types available in the market such as electric, gas, or wood-fired kilns. Choose one that fits your budget and artistic needs.
- Appropriate Space: Kilns require a designated area with proper ventilation and enough room for loading and unloading pieces. Consider using a garage, shed, or outdoor space if you don’t have a dedicated room for your kiln.
- Power Supply: Most electric kilns require a 240-volt outlet, so make sure you have the appropriate power supply in your space. Gas or wood-fired kilns may also need additional plumbing connections.
- Kiln Furniture and Accessories: This includes shelves, posts, stilts, and other accessories that support and protect your pieces during firing.
- Safety Equipment: To protect yourself from potential hazards, it’s crucial to invest in safety equipment such as gloves, eye protection, and heat-resistant clothing.
10 Easy Steps on How to Set Up a Kiln at Home
Step 1. Choose the Right Location:
When choosing the right location for your kiln, consider multiple factors to ensure a safe and effective workspace. Begin by identifying a space that offers adequate ventilation; proper airflow is critical to managing fumes and heat generated during the firing process. An outdoor area, such as a covered patio or a generously sized garage, can accommodate these needs. Additionally, the location should be free from flammable materials and have sufficient clearance on all sides of the kiln to prevent overheating. Ensure that the floor can support the weight of the kiln and can withstand any potential heat exposure.
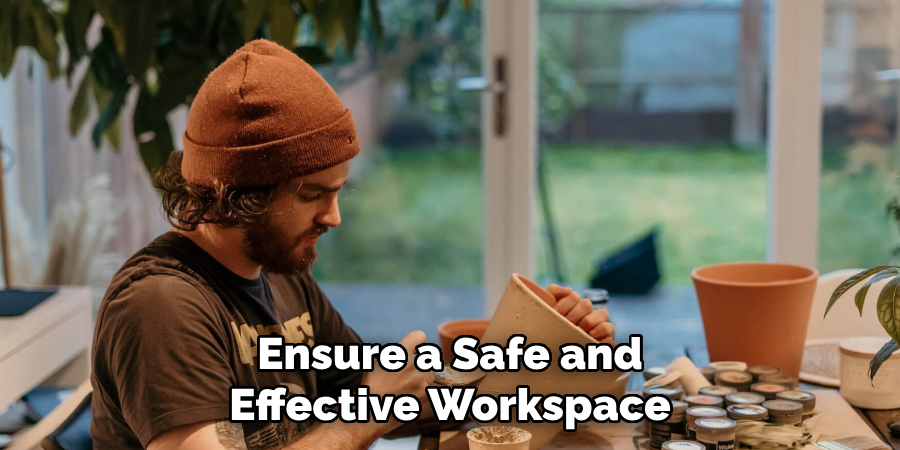
If your chosen spot is within a residential area, be sure to check any local building codes and homeowner association regulations, as some areas may have specific restrictions or requirements for operating a kiln. Once you’ve selected an appropriate location, make arrangements for the necessary electrical or gas connections, verifying that they meet the specifications for your kiln model. Planning thoroughly at this stage can prevent inconvenient setbacks and create a smoother setup process.
Step 2. Prepare the Workspace:
Once you have chosen the location for your kiln, the next step is to prepare the workspace to ensure it’s ready for installation. Start by clearing the area of any clutter and removing flammable materials to create a safe environment. If your kiln is in a garage or basement, lay down a heat-resistant mat or tile flooring to protect the surface from heat damage. Ensure the space is well-lit to facilitate the loading and unloading of pieces. Assess the ventilation setup and make necessary modifications to improve airflow, such as installing additional fans or openable windows. With a clean and adequately prepared workspace, you lay the foundation for efficient and safe kiln operation.
Step 3. Install Required Power Connections:
Ensuring your kiln has the necessary power supply before proceeding with the installation. For electric kilns, verify that your chosen space has a 240-volt outlet capable of providing the necessary power. If not, consult a professional electrician to install the required outlet safely. For gas kilns, ensure that the gas lines are connected and operational while following specific local regulations regarding their use. Whichever power source your kiln employs, double-check all connections for safety and compliance with the kiln’s manufacturer guidelines to avoid potential hazards.
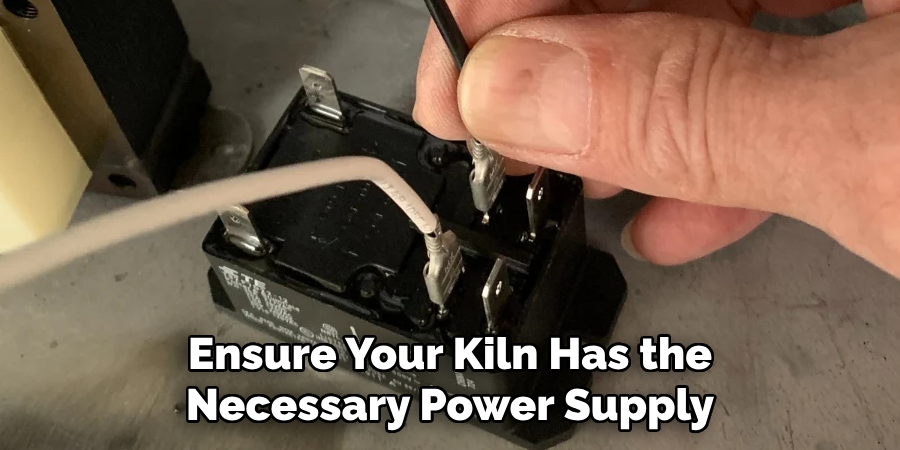
Step 4. Position the Kiln:
Now that your workspace is ready and the necessary power connections are in place, it’s time to position the kiln. Carefully move the kiln into its designated spot, leaving sufficient clearance on all sides to prevent heat buildup. Collectively refer to the manufacturer’s recommendations regarding spacing to help maintain optimal airflow. Having an assistant to help maneuver the kiln into place is advisable, as they can be pretty heavy. Once in position, double-check that the kiln doors can fully open without obstruction and that the control panel is easily accessible.
Step 5. Assemble Kiln Furniture:
With the kiln now positioned, it is time to prepare its interior by assembling and arranging the kiln furniture. Begin assembling shelves, posts, and stilts to accommodate the size and shape of your typical projects. Balance stability and airflow by leaving gaps between shelves and ensuring they are level. This setup supports your artwork and maximizes the kiln’s capacity and efficiency. Remember to use kiln wash on the shelves to prevent glaze drips from sticking to the surfaces, preserving your kiln furniture for long-term use.
Step 6. Calibrate and Test the Kiln:
Before you begin firing your work, you must ensure that the kiln is functioning correctly by calibrating and testing it. Start by familiarizing yourself with the control panel and any digital settings specific to your kiln model. Run a test fire without any art pieces inside to confirm that the kiln reaches the desired temperatures and maintains them consistently. Monitor the heating elements for even heat distribution, and check for any unusual sounds or smells that might indicate a problem.
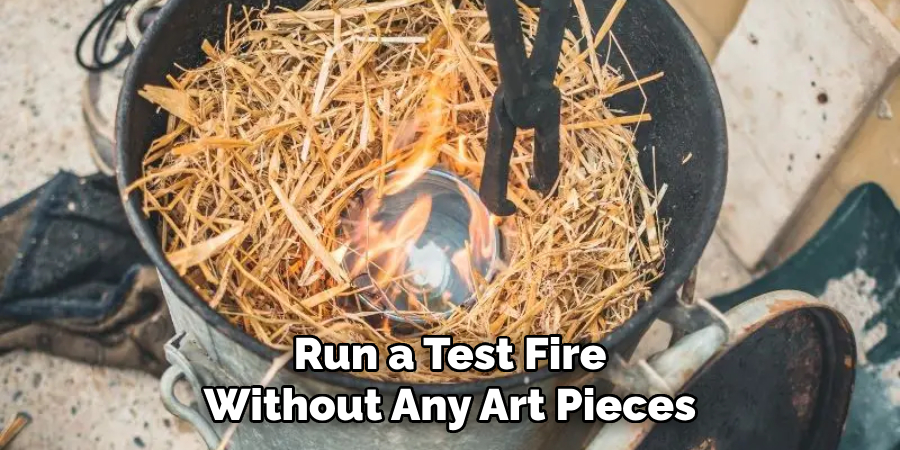
By completing this test run, you can identify and troubleshoot potential issues, ensuring a smooth operation when you fire your actual projects.
Step 7. Load the Kiln:
It’s time to load your ceramic pieces once you are confident that the kiln is calibrated correctly. Carefully arrange the items on the shelves, ensuring ample space between them for uniform heat circulation. Consider the size and thickness of each piece, arranging heavier or bulkier items at the bottom. If needed, use stilts to elevate pieces, especially those with glaze on the bases, to prevent sticking. Double-check that none of the pieces are in contact with each other or the kiln walls, which could result in damage during firing.
Step 8. Fire the Kiln:
With the kiln fully loaded and ready, program the firing schedule according to your project’s needs. Each type of clay and glaze has different requirements, so consult clay and glaze manufacturers for recommended temperature settings and ramp rates. Start the kiln and monitor the firing process as needed, ensuring that all safety protocols are followed during operation. As the kiln reaches the peak temperature, be attentive to any automatic hold times or cooling cycles programmed in it.
Step 9. Cool Down Process:
After completing the firing cycle, allow your kiln to cool down gradually and naturally. Opening the kiln too soon can shock the ceramic pieces, causing cracks or breakage. Most kilns have recommended cooling times, so adhere to these guidelines to protect your work. Wait until the kiln reaches a temperature safe to the touch, typically around room temperature, before opening the door. Patience during this stage aids in the longevity and durability of your fired pieces.
Step 10. Unload and Inspect:
Carefully unload the fired pieces once the kiln and its contents have cooled adequately. Handle each item carefully as you inspect for any imperfections or damage that may have arisen during the firing process. Take note of any unexpected results, which could inform adjustments for subsequent firings. Cleaning up kiln furniture and your workspace after unloading contributes to a tidy and efficient environment for your next project. Finally, celebrate the completion of your work and appreciate the beautiful transformations achieved through the kiln.
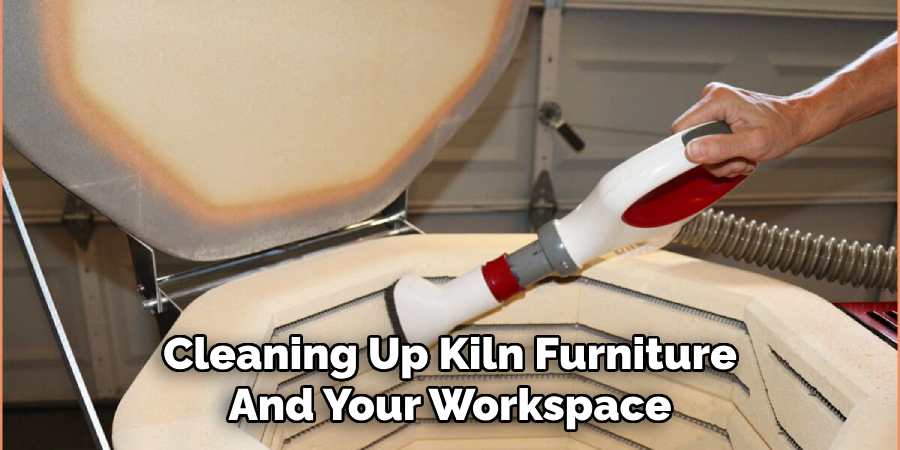
By following these steps for installing and using your kiln, you can ensure safe and successful firings of your ceramic pieces.
Conclusion
Setting up a kiln at home can be rewarding and greatly enhance your ceramic crafting capabilities.
By following the detailed steps on how to set up a kiln at home, from securing power connections to finalizing the cooling of your kiln, you ensure a smooth and effective installation. Maintaining safety standards throughout the process is important, including consulting professionals when necessary, adhering to manufacturer guidelines, and being meticulous about proper setup and operation. With careful attention to each step, you safeguard your equipment and workspace and maximize the potential of your ceramic creations.
Whether for professional artistry or personal enjoyment, a well-installed kiln can open new horizons in ceramics, allowing for greater creative expression and precision in every piece you create.
Specialization:
- Master of wheel-throwing, hand-building, and advanced glazing techniques
- Focus on creating both functional pottery and decorative art pieces
Recognition:
- Celebrated by collectors and art enthusiasts for creating one-of-a-kind pieces that blend artistry with functionality
- Participates in local and national exhibitions, earning accolades for his innovative designs and craftsmanship
Passion:
- Deeply committed to exploring and pushing the boundaries of ceramic artistry
- Continuously experiments with new materials, firing techniques, and artistic concepts to evolve his craft
Personal Philosophy:
- Believes in the transformative power of art, aiming to evoke emotions and connections through his ceramic creations
- Advocates for sustainability in ceramics, using eco-friendly materials and practices whenever possible